Choosing the right brazing rod for stainless steel can significantly impact the quality and durability of your finished project. With years of experience in metalworking, understanding this crucial component can set your projects up for success from the outset. Here’s an insightful exploration into the intricacies of selecting brazing rods for stainless steel, ensuring you make informed decisions with authority and trustworthiness.
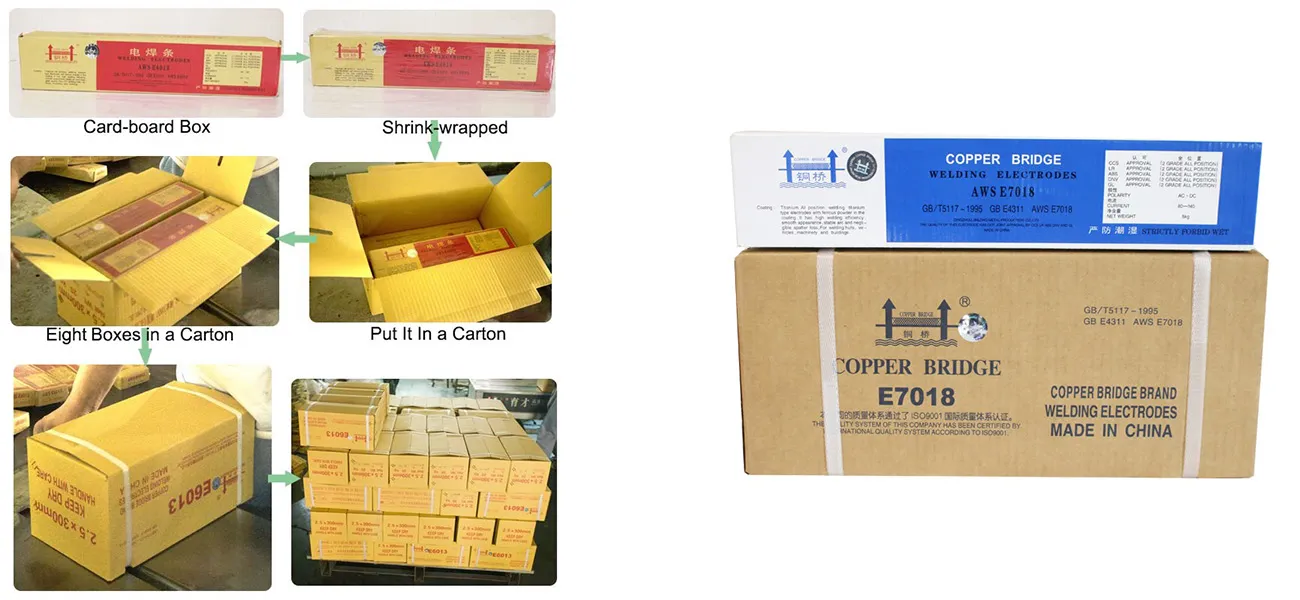
Stainless steel is a preferred choice in industries ranging from aerospace to culinary, owing to its outstanding corrosion resistance and aesthetic appeal. However, its distinctive properties necessitate specific considerations when brazing. The core principle lies in compatible thermal expansion and maintaining corrosion resistance at the joint.
One of the most effective choices for brazing stainless steel is the use of silver-based brazing rods. Silver alloys offer excellent flow properties and electrical conductivity, which help in forming strong joints that can withstand mechanical stresses.
A typical silver brazing alloy contains a mix of silver, copper, and zinc. This combination provides optimal performance with a melting temperature conducive to preserving the integrity of stainless steel.
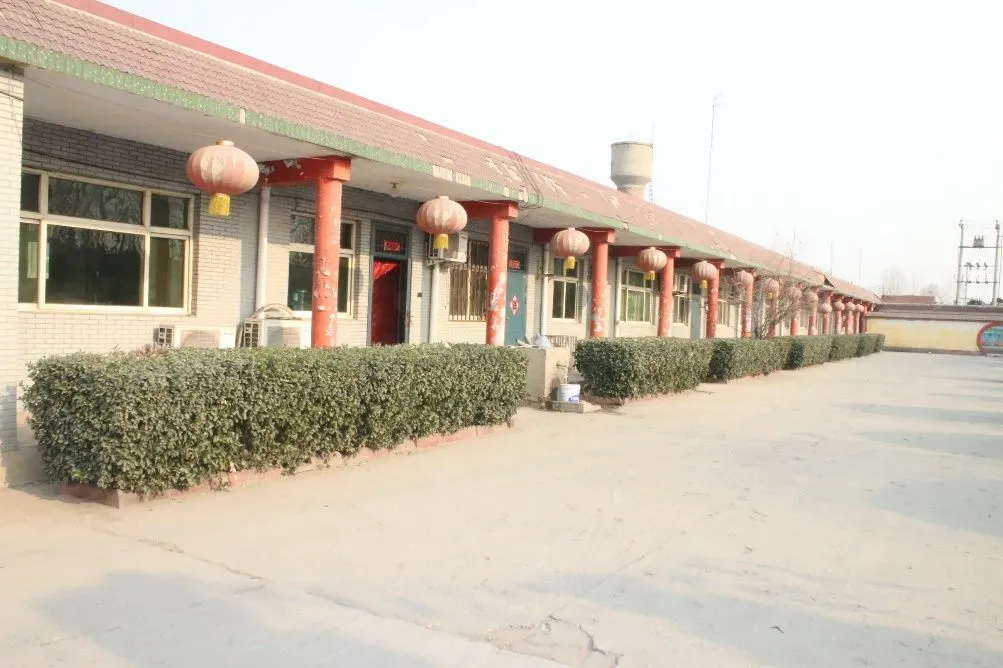
Nickel-based alloys represent another preferable option when working with stainless steel, particularly in high-temperature applications. Nickel brazing alloys provide excellent resistance to oxidative environments and can withstand extreme temperature cycles without losing joint integrity. This makes them ideal for use in environments where the joint might be exposed to fluctuating temperatures.
Professionals often prefer phosphor bronze brazing rods for their cost-effectiveness without significantly compromising on performance. These rods, made from a combination of copper, tin, and phosphorous, offer robust mechanical properties suitable for bonding stainless steel, especially in plumbing applications. They are renowned for their capacity to bond dissimilar metals, making them versatile for a variety of projects.
what type of brazing rod for stainless steel
For general-purpose applications, copper-based brazing rods can be a practical choice, although they require the use of a proper flux to resolve any wetting issues associated with stainless steel’s chromium oxide layer. The flux serves the crucial purpose of stripping away surface oxides at higher temperatures, providing a clean surface for the brazing alloy to adhere. A boron-modified flux is often utilized with copper-based rods to enhance their performance with stainless steel.
Tools specializing in ensuring precise temperature control are indispensable when working with brazing rods for stainless steel. Precision in temperature management minimizes thermal stress within the joint, preventing material distortion and guaranteeing the longevity of the brazed connection.
The choice is not merely dependent on the base materials alone but also on the specific application, operational environment, and esthetic considerations. For instance, in aerospace applications, where weight and strength are critical, a proper balance of material properties and brazing filler metals should be selected. Similarly, for marine applications, corrosion resistance against saltwater takes precedence.
Equally important is the adherence to safety standards and industry regulations, which assures reliability and peace of mind for end-users. The AWS (American Welding Society) and ASME (American Society of Mechanical Engineers) provide comprehensive guidelines that should be followed to ensure compliance and heightened quality assurance.
In all cases, consulting with an experienced metallurgist or brazing specialist can provide tailored advice tailored to the specific details of your project. Achieving expertise in selecting and applying brazing rods not only enhances trustworthiness but also solidifies one's professional authority in the field. With these insights, your stainless steel fabrication projects will achieve the highest levels of quality, precision, and durability, setting a benchmark in metalworking excellence.