Choosing the right TIG (Tungsten Inert Gas) electrode for welding stainless steel is a critical decision that directly impacts the quality, durability, and precision of the weld. For those working with stainless steel, the intricacies of this decision cannot be overstated, especially given its widespread use in sectors requiring high corrosion resistance and aesthetic appeal like food processing, medical equipment, and architectural structures. This article delves into the factors that influence the choice of the TIG electrode for stainless steel, providing insights drawn from experience and expertise in the field.
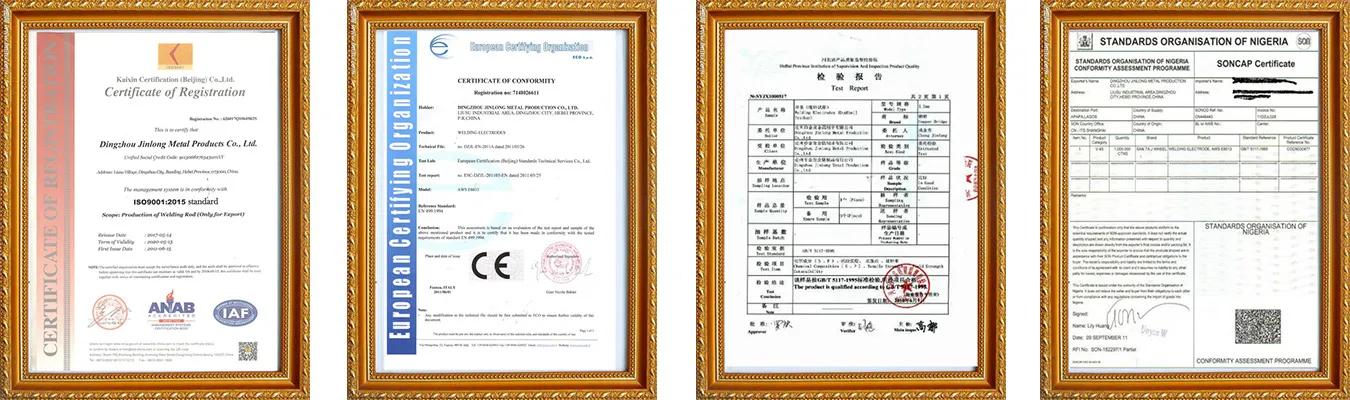
TIG welding, known for its precision and cleanliness, requires careful selection of electrodes to ensure optimal results. The electrode is the central element around which the entire welding process revolves, literally melting and bonding materials together with finesse. For stainless steel, the most commonly recommended electrode types include thoriated, ceriated, and lanthanated tungsten electrodes.
Thoriated Tungsten Electrodes (EWTh-1 and EWTh-2) These electrodes have been a staple in the welding community for decades, primarily for their arc stability and longevity. Thoriated tungsten contains thorium oxide, which enhances electron emission properties, making them ideal for DC welding applications. However, due to the radioactivity of thorium, alternatives are often sought in environments demanding higher safety protocols or where health concerns could pose a considerable risk.
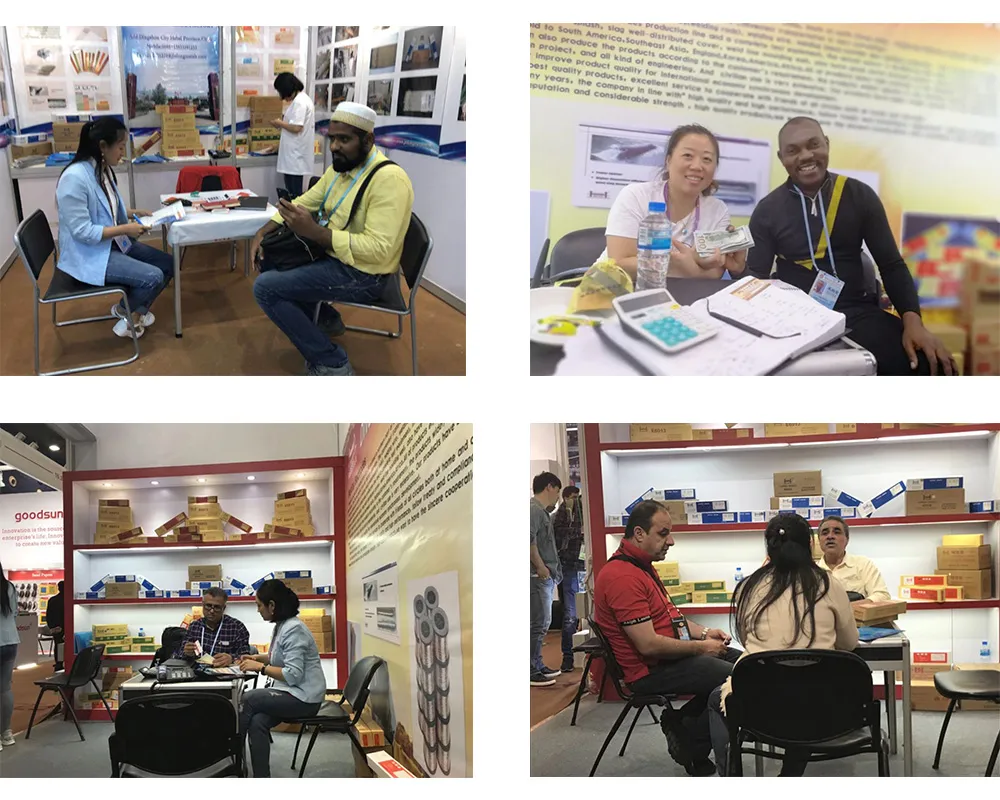
Ceriated Tungsten Electrodes (EWCe-2) The 2% ceriated tungsten electrode is a preferable choice for many professionals aiming for a lower risk substitute to thoriated electrodes. Known for offering excellent arc starts at low amperages and superior performance on DC welding processes, ceriated electrodes maintain an edge in welding thin stainless steel sheets or when intricate welding requiring a soft start and focused arc is necessary.
Lanthanated Tungsten Electrodes (EWLa-1 and EWLa-2) Another popular selection, the lanthanated tungsten electrodes blend well with the characteristics required for both AC and DC welding. With enhanced stability and electron emission qualities similar to thoriated, without the radioactivity, they are the go-to for hybrid applications, handling various stainless steel alloys with aplomb. Choosing lanthanated electrodes ensures a robust, steady arc while minimizing contamination risks in the weld pool.
what tig electrode for stainless
Size Matters In addition to the type of tungsten chosen, the diameter of the electrode is equally important. Common sizes include 1/16 inch, 3/32 inch, and 1/8 inch, each suitable for different amperage ranges and material thicknesses. Opting for a 1/16 inch electrode works best with thin materials requiring lower amperage, while thicker sections are better served with a 3/32 or 1/8 inch electrode to handle higher current without degrading the electrode's lifespan.
Preparation and Maintenance Maintenance of the electrode is crucial in ensuring optimal performance. Proper storage in a clean, dry environment prevents contamination. Equally, sharpening or tapering the electrode to a specific angle— typically between 30 to 45 degrees for most applications— allows for a focused, consistent arc, reducing arc wander and ensuring a more accurate weld.
Balancing Act Ultimately, choosing the right TIG electrode comes down to balancing performance needs with practical workplace considerations such as safety, environmental impact, and cost. Opting for a trusted brand or manufacturer can significantly boost confidence in the electrode's reliability and performance metrics. High-quality electrodes also minimize the likelihood of requiring frequent replacements, reducing downtime and increasing productivity.
The choice of tungsten electrode is foundational to achieving a precise, aesthetically pleasing, and durable stainless steel weld. By understanding the advantages of each type and maintaining expert handling practices, welders can optimize their techniques and consistently produce results that meet industry standards. Whether a seasoned professional or novice, investing the time in selecting the right electrode is crucial for the seamless integration of functionality and form in stainless steel welding projects.