Choosing the right welding rod is crucial for achieving high-quality welds in any project, whether you are a seasoned professional or a hobbyist welder. Two popular types of welding rods, the 6011 and 7018, are often at the center of a welder’s selection dilemma. However, understanding the distinct characteristics and ideal applications of these rods can enhance both the quality and efficiency of your work.
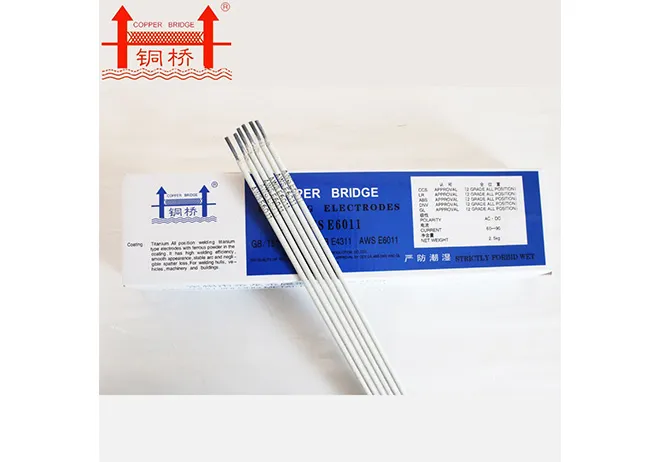
The 6011 welding rod is well-regarded for its versatility and deep penetration capabilities. This rod is a go-to choice for those working in environments with dirt, rust, or paint, as it can effectively burn through surface contaminants to deliver solid welds. This is particularly useful in agriculture and construction, where perfect surface cleanliness cannot always be assured. The 6011 rod utilizes an alternating and direct current (AC/DC) and is valued for its ability to produce strong joints even in less-than-perfect conditions. Its fast-freeze characteristics, which allow for solidifying the molten weld pool quickly, make it ideal for vertical and overhead welding—positions where managing weld pool gravity is challenging.
In contrast, the 7018 welding rod is highly celebrated for producing smooth, aesthetically pleasing welds that combine robustness with resilience. It’s revered for its low-hydrogen coating, which significantly reduces the risk of weld cracking—a crucial factor when working on critical projects like pipelines, bridges, and pressure vessels. The 7018 is best suited for materials that require clean and strong welds, like structural steel and heavy-duty manufacturing parts. However, it requires a particularly clean surface and is mainly used with direct current (DC), which may limit its versatility in certain scenarios. The rod must also be kept in a controlled, dry environment to maintain its low-hydrogen properties, necessitating careful storage and handling.
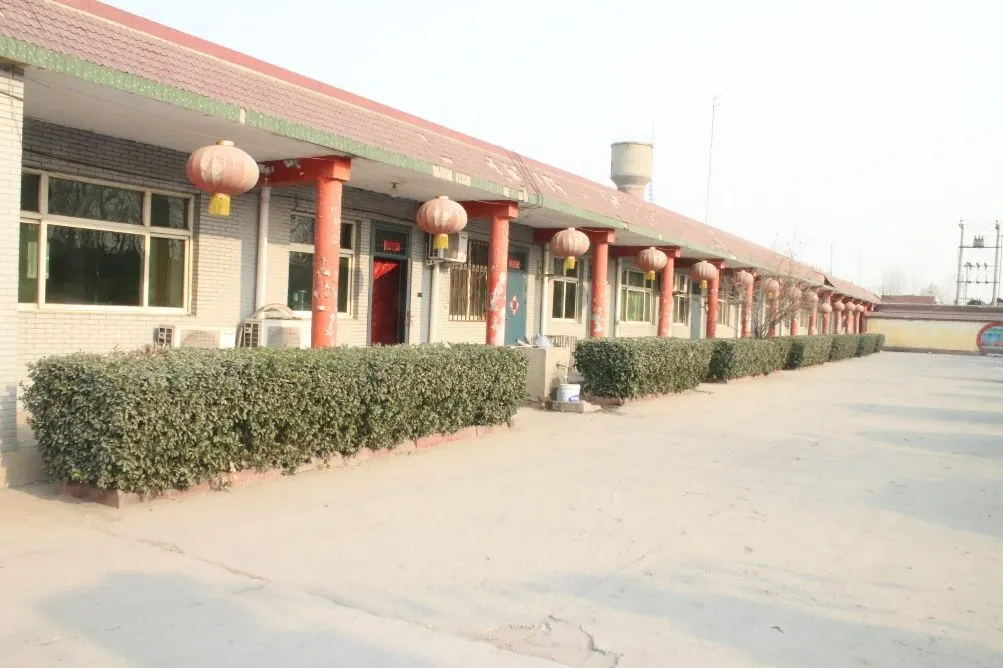
From an experience standpoint, beginners may find the 6011 easier to work with due to its forgiving nature regarding surface preparation and its compatibility with a more expansive array of welding machines. Meanwhile, experienced welders who demand precision and structural integrity often prefer the 7018 due to its superior strength and finish, provided they have the necessary equipment and controlled conditions.
what's the difference between 6011 and 7018 welding rod
For professionals, expertise in handling these rods comes with understanding the specific demands of your project. When weld accessibility is limited, or when tasks require out-of-position welding, the 6011 is often unparalleled. Conversely, if your work environment supports pre-heating and optimal surface preparation, and if weld appearance is a priority, the 7018 becomes a prime candidate.
In examining authoritativeness, one can refer to industry standards and certifications where both rods play a critical role. The American Welding Society (AWS) provides clear guidelines on the applications and uses of these rods within the A5.1/A5.1M specification,
underscoring their respected place in the welding community. Understanding these standards can enhance a welding professional’s knowledge and application of each type, reinforcing trust and competence in selecting the right rod.
Ultimately, trusting the choice between 6011 and 7018 rods stems from a comprehensive assessment of the welding environment, material type, required structural integrity, and the skill level of the welder. Consulting with experts, participating in hands-on practice, and ongoing learning are key to making informed, strategic decisions that best fit your welding needs. As welding technology continues to evolve, staying informed with the latest advancements and community insights will continue to expand your skill set and improve your craftsmanship.