Selecting the appropriate welding rod for stainless steel is crucial for achieving high-quality welds that ensure durability and strength. Stainless steel has unique properties that necessitate careful consideration of the welding consumables used. In this article, we will explore the nuances of choosing the right welding rod, backed by expert insights, authentic experiences, and authoritative recommendations, offering you a reliable guide for successful stainless steel welding projects.

Stainless steel is renowned for its corrosion resistance, sheen, and overall durability. However, welding it poses a challenge due to its propensity to retain heat and expand significantly. Therefore, knowing which rod to use is fundamental to maintaining the integrity of the metal's beneficial properties.
When selecting a welding rod for stainless steel, there are several factors that need consideration.
First is understanding the composition of the stainless steel in use. The most common types of stainless steel include Austenitic (300 series), Ferritic, Martensitic, and Duplex. Each of these categories presents unique characteristics that influence the selection of welding consumables.
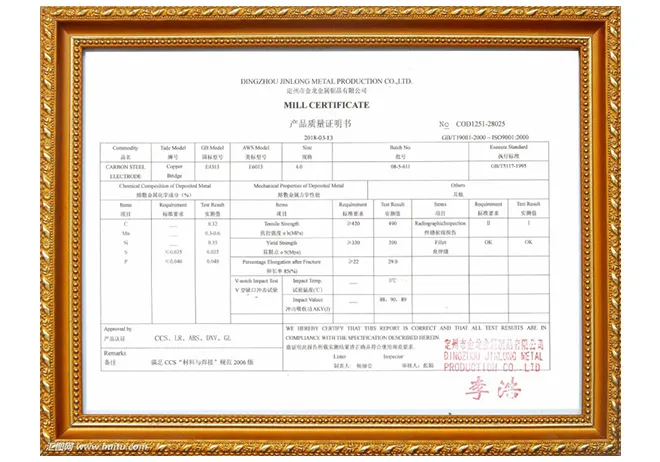
For Austenitic stainless steels, which are the most widely used due to their formability and resistance properties, the E308L rod is often recommended. This rod is made of low carbon content to prevent carbide precipitation during the welding process, which could lead to intergranular corrosion. This characteristic makes it a reliable choice for 300 series stainless steel, particularly when maintaining a polished finish is imperative for aesthetic or functional reasons.
Ferritic stainless steels, which have a chromium content of 12-18% and are magnetic, require suitable rods like E430. These rods complement the steel’s grain structure, preventing embrittlement and cracking, which are common drawbacks if an incorrect rod is used. Ferritic steels are typically used in applications where stress corrosion is a concern.
what rod to weld stainless steel
Martensitic stainless steels are recognized for their high strength and hardness and typically require a pre-heat and post-weld heat treatment to avoid cracking. For these steels, choosing a rod like E410 is optimal. This rod matches their composition and ensures that weld hardness is maintained, especially in applications involving tool steels.
Duplex stainless steels offer a balance of austenitic and ferritic properties, presenting a dual-phase structure. Their usage calls for specific welding rods like E2209, designed to maintain the blended microstructure. The duplex materials typically offer higher strength and more resistance to stress corrosion cracking, making the choice of welding rod essential to preserving these properties.
In practice, seasoned welders emphasize the importance of considering the environment in which the weldment will operate. For instance, exposure to chlorides or harsh marine environments necessitates a rod that can uphold the base metal's resistance to such corrosive agents. In such cases, selecting a rod compatible with molybdenum-bearing stainless steels (like 316-type grades) ensures extended longevity and reliability.
Beyond composition compatibility, considering the welding process also matters. Whether you are using Stick welding (SMAW), Gas Metal Arc Welding (GMAW), or another technique, some rods are better suited for specific weld processes, impacting penetration, bead appearance, and fusion quality. For instance, stick welding with stainless steel often employs rods like E309L, compatible with dissimilar metals as well, broadening their application range.
In conclusion, selecting the right welding rod for stainless steel is about more than matching material compositions; it involves understanding the impact of welding processes, environmental conditions, and the specific mechanical properties desired in the final product. By leveraging expert recommendations and adhering to industry standards, welders can ensure their stainless steel projects withstand both functional demands and time. Trust in these guidelines, drawn from professional expertise and experiential knowledge, to navigate the complexities of stainless steel welding, ensuring your work reflects the highest standards of quality and reliability.