Choosing the right welding rod for stainless steel is crucial for achieving optimal results in your welding projects. The selection of a suitable rod depends on various factors, such as the type and grade of stainless steel, the welding process, and the desired characteristics of the finished product.
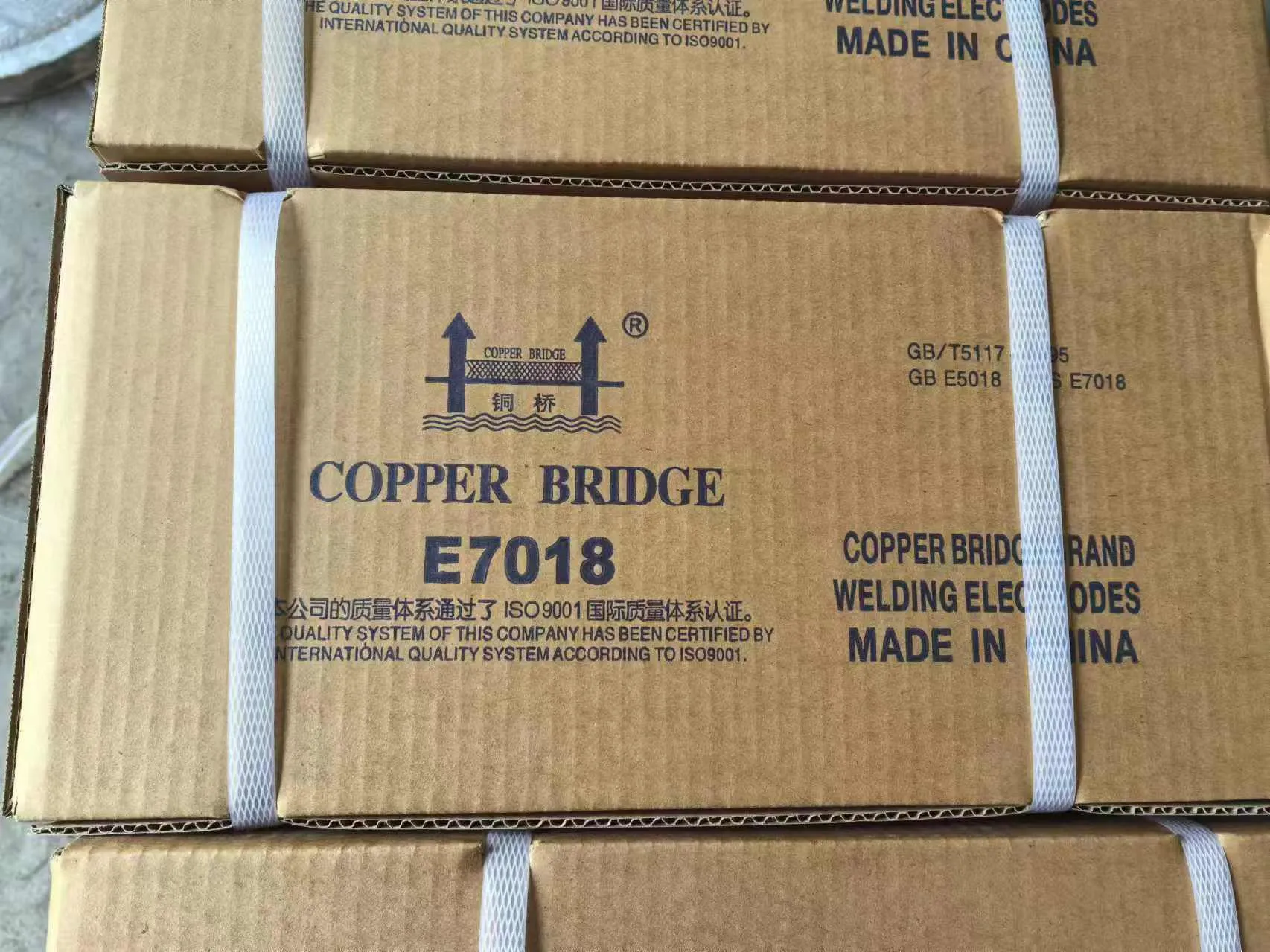
Understanding Rod Characteristics
When it comes to welding stainless steel, the most common rods used are the austenitic stainless steel electrodes. These rods, such as the E308L, E309L, and E316L, are favored for their excellent corrosion resistance, ease of use, and mechanical properties.
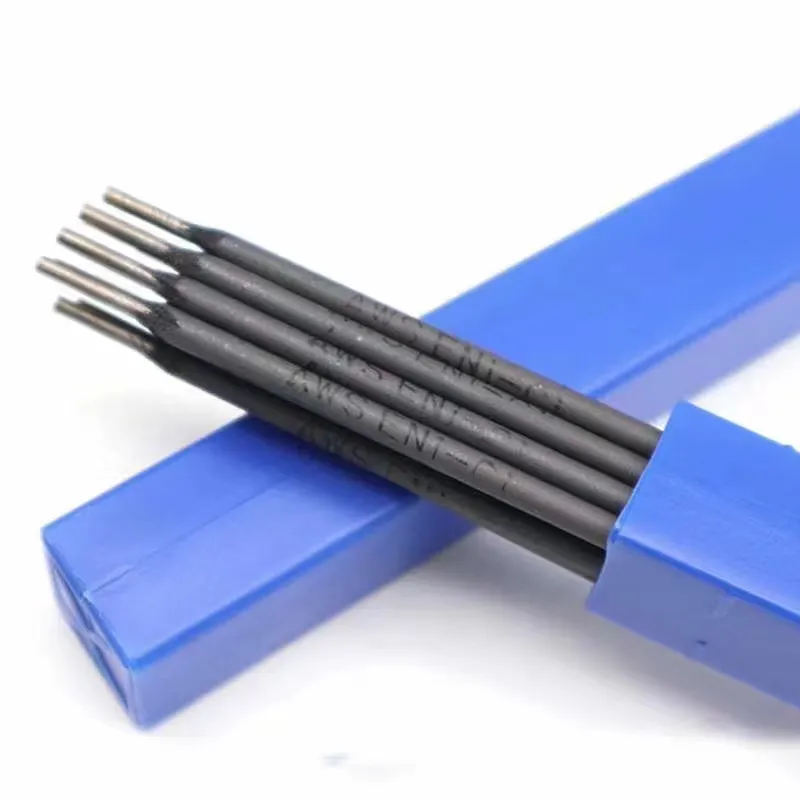
The E308L electrode is most commonly used for 304 and 304L stainless steels. It's a versatile option that offers good fusion properties and prevents chromium carbide precipitation, a common issue that can lead to intergranular corrosion.
For welding 309 stainless steel or joining dissimilar metals, the E309L electrode is preferred. It accommodates the differences in thermal expansion between metals, thereby reducing the risk of cracking or weakening of the weld at high temperatures.
E316L electrodes are used for 316 or 316L stainless steels, known for their superior resistance to corrosion, especially in chloride or saltwater environments. This makes them ideal for applications in marine, chemical, and pharmaceutical industries.
Welding Processes and Techniques
The choice of rod is also influenced by the welding process you choose. For Stick Welding (SMAW), the type of coating on the electrode affects the penetration, arc stability, and slag control. Here, a basic coating is typically preferred for its cleaner welds and reduced hydrogen content.
For TIG (GTAW) welding, filler rods such as ER308L, ER309L, and ER316L are typically used. These rods differ from the coated electrodes and are thin wires fed into the weld pool, allowing for precise control over the heat and weld deposition. TIG welding is ideal for thinner materials and projects where aesthetic finish is important.
MIG (GMAW) welding with stainless steel wires like ER308, ER309, and ER316 offers higher deposition rates and is often used for larger projects. The shielding gas mixture, often a combination of argon with a small percentage of oxygen or CO2, plays a critical role in the quality of the weld.
what rod do you use to weld stainless steel
Factors Influencing Rod Choice
When selecting a welding rod for stainless steel, consider the working environment. For instance, welding in a confined space or a location with limited ventilation necessitates a rod that minimizes toxic fumes. Similarly, outdoor projects may require rods resistant to moisture absorption to prevent weld porosity.
Furthermore, the operational service conditions of the welded joint should guide your choice. If the joint is expected to endure high temperatures, corrosive environments, or frequent mechanical stress, selecting a rod tailored to withstand these conditions is critical.
Expert Insights and Real Experience
Industry experts emphasize the importance of pre-weld preparation and post-weld treatments in addition to the correct rod selection. Cleaning the base material to remove contaminants such as oils, greases, and oxides can prevent defects and improve weld quality. Post-weld pickling and passivation processes help in restoring the corrosion resistance of stainless steel by removing any heat tint and oxide layers.
Trust and Manufacturer Recommendations
Trust in your materials is key, thus sourcing your welding rods from reputable manufacturers is crucial. These companies invest in research and development to produce high-quality, reliable welding consumables. Furthermore, manufacturers' recommendations often include valuable insights into the best applications and settings for their products.
Given the complexity and importance of selecting the right rod for stainless steel welding, consulting with welding professionals or engaging resources from industry associations can provide additional guidance.
By understanding the nuances of rod selection and applying a combination of expert advice and personal experience, welders can achieve strong, durable, and aesthetically pleasing results. This comprehensive knowledge ensures that projects are completed efficiently, safely, and with the highest quality standards.