When it comes to selecting stainless steel for industrial applications, understanding the subtle differences between SS316 and SS316L is crucial. Both these grades belong to the austenitic family of stainless steels but have distinct characteristics making them suitable for specific environments and uses. This article explores the key differences, guiding you on which grade may be more suitable for your needs.
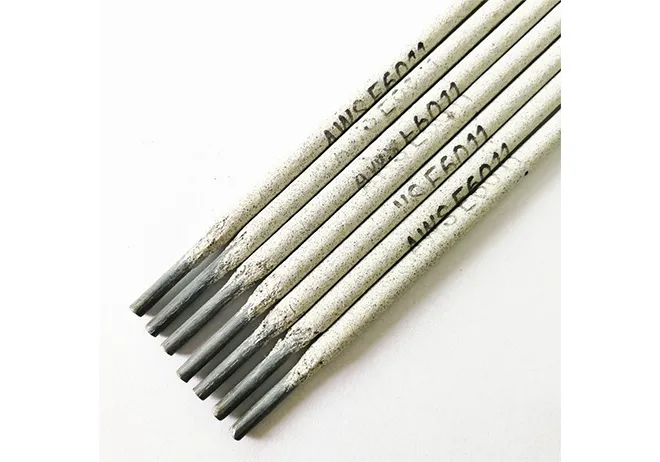
SS316 is well-recognized for its mechanical properties and resistance to harsh environments. With a composition including chromium, nickel, and molybdenum, SS316 excels in resisting pitting and crevice corrosion, especially in chloride environments. This makes it an ideal candidate for applications in marine environments, chemical processing, and pulp and paper production.
On the other side, SS316L serves as a low-carbon version of SS316. The 'L' signifies 'low carbon' and represents an important differentiation point. By having a lower carbon content, SS316L minimizes the danger of carbide precipitation during welding, thus enhancing its ability to maintain corrosion resistance even after exposure to high temperatures. This particular trait makes SS316L highly suitable for welded constructions where heat treatment post-welding is impractical or impossible.
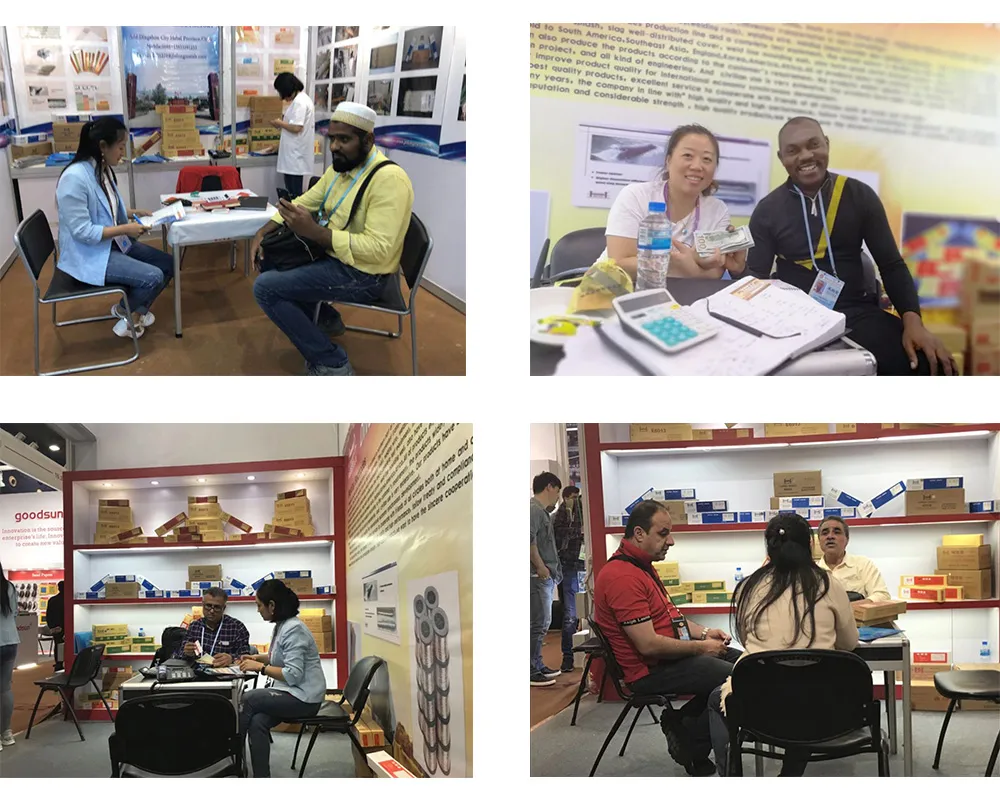
The lower carbon content in SS316L does slightly compromise its tensile strength compared to SS316. However, in applications where high strength is not the primary requirement, but welding plays a pivotal role, SS316L becomes the preferred choice.
what is the difference between ss316 and ss316l
Professionals dealing with fabrication often opt for SS316L because it reduces the likelihood of intergranular corrosion without extra processing. This property is especially vital in maintaining the structural integrity of the components over extended periods and in environments experiencing high variations in temperature.
In practical scenarios, if an application involves environments with extremely high levels of chlorides such as saltwater or de-icing salts, the molybdenum content in both SS316 and SS316L assists in offering superior protection against corrosion. Nevertheless, delicate industries like pharmaceuticals and food processing may prefer SS316L for its reliability post-welding and its ability to withstand the sanitization processes involving chemicals and cleaning agents more effectively.
Cost implications also influence the decision between SS316 and SS316L. Generally, SS316 is slightly less expensive than SS316L due to the lower levels of processing required in its manufacture. For large-scale projects where budget constraints are critical, opting for SS316 might offer satisfactory performance provided the welding requirements are minimal.
In conclusion, the choice between SS316 and SS316L should be guided by the specific demands of the application. Considerations such as the nature of the environment, the necessity of welding, and cost constraints play vital roles in determining the most suitable grade. For optimal results, consulting with materials engineers or corrosion specialists who can assess the detailed requirements of your project and suggest the most appropriate material is always advisable. With a deeper understanding of the differences between SS316 and SS316L, you can make informed decisions that enhance the longevity and performance of your design projects.