Stainless steel is a fundamental material used across various industries, notably in manufacturing, construction, and consumer goods.
Two common grades that often draw attention are 316 and 316L. Understanding their differences can be critical for selecting the appropriate material for specific applications, impacting durability, cost, and lifespan.
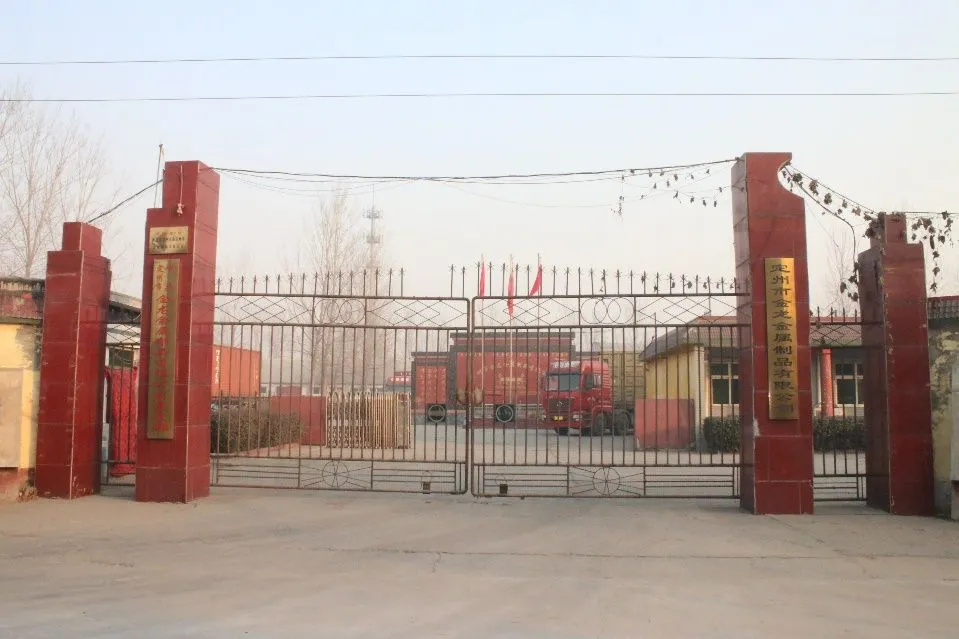
316 stainless steel, part of the austenitic family of stainless steels, is primarily composed of iron, chromium, nickel, and molybdenum. This composition is celebrated for its exceptional resistance to corrosion, especially against chlorides and industrial solvents. The addition of molybdenum provides 316 with enhanced resistance to pitting and crevice corrosion compared to 304 stainless steel, making it a preferred choice for marine environments or settings with exposure to aggressive chemicals.
In contrast, 316L stainless steel maintains a similar composition but with a slight variation a lower carbon content. This distinction, while minor in percentage, plays a significant role in the material's performance under certain conditions. The “L” in 316L stands for “low” carbon content, usually capped at 0.03% compared to the 0.08% in standard 316. This reduction minimizes the risk of carbide precipitation during welding processes, which can lead to intergranular corrosion.
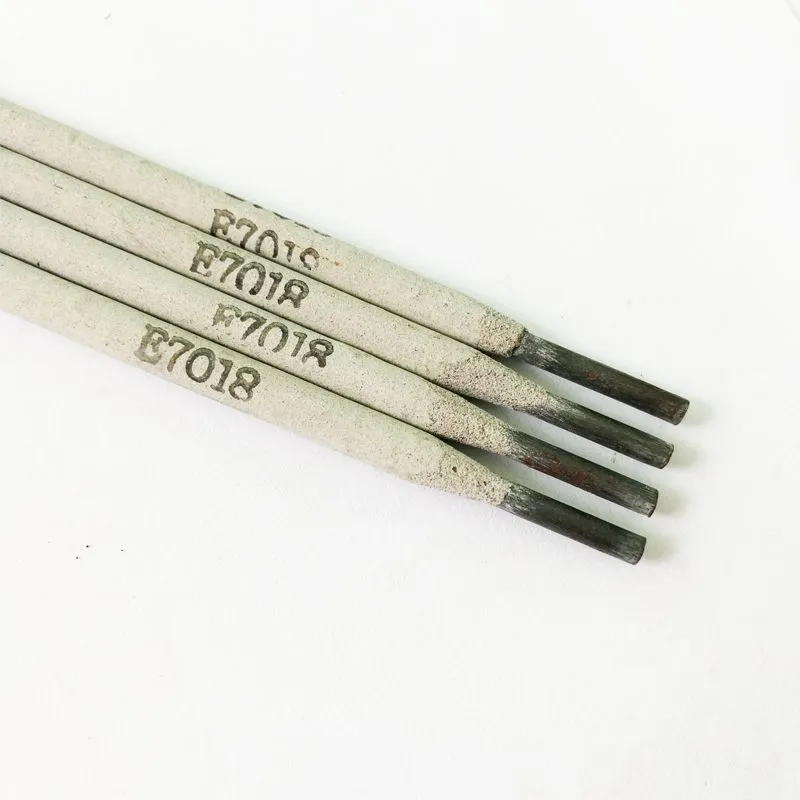
Why does this matter? During welding, the high temperatures can lead to carbide precipitation along the grain boundaries if the carbon content is too high, creating weak spots that can significantly undermine structural integrity. Thus, for applications requiring extensive welding, 316L is often the superior choice, ensuring long-term stability and integrity of the structure.
Another area these two stainless steel variants excel in involves differing tensile strengths. 316 typically boasts a higher tensile and yield strength compared to 316L due to its higher carbon content. This quality might make it a suitable choice for applications where formability is secondary to strength and load-bearing capacity.
what is the difference between ss 316 and 316l
However, in contexts prone to stress corrosion cracking or exposure to extreme temperature fluctuations, 316L’s lower carbon content actually improves its resilience, adding to its appeal in such environments. Industries such as pharmaceutical production, where purity and hygiene are paramount, often lean towards 316L. Its ability to withstand repeated sterilization and washing without compromising its surface finish or integrity gives it an edge.
Economic considerations also play a part. The cost of 316 and 316L stainless steel can vary. Because 316 contains slightly more carbon, it may occasionally be less expensive than its low-carbon counterpart. However, the price difference usually is marginal and should be weighed against the costs associated with potential material failure or end-of-life if the incorrect grade is used.
For designers and engineers, understanding the nuanced differences between 316 and 316L can lead to optimal material selection and enhanced end products. In choosing between the two, consider factors such as the environment (chemical exposure levels), the importance of weldability, and the mechanical property requirements of the application. Consulting with material engineers or suppliers with expertise in stainless steel can further help in making an informed decision.
In conclusion, both 316 and 316L stainless steels offer valuable properties that cater to different industrial needs. Their differences, while subtle, are significant enough to influence performance, durability, and cost-efficiency. A thorough evaluation guided by application requirements should dictate the most appropriate choice. Through informed decisions, businesses not only safeguard structural integrity but also optimize their investment in materials tailored for long-term efficacy and reliability.