The 312 welding rod, often overshadowed by its more commonly known counterparts, is an exceptional tool in the world of welding. Known for its versatility and robustness, the 312 welding rod is pivotal for those looking to tackle challenging projects with dissimilar metals. Its unique features and applications make it indispensable in specialized welding processes, promising reliability and precision when handling complex welds.
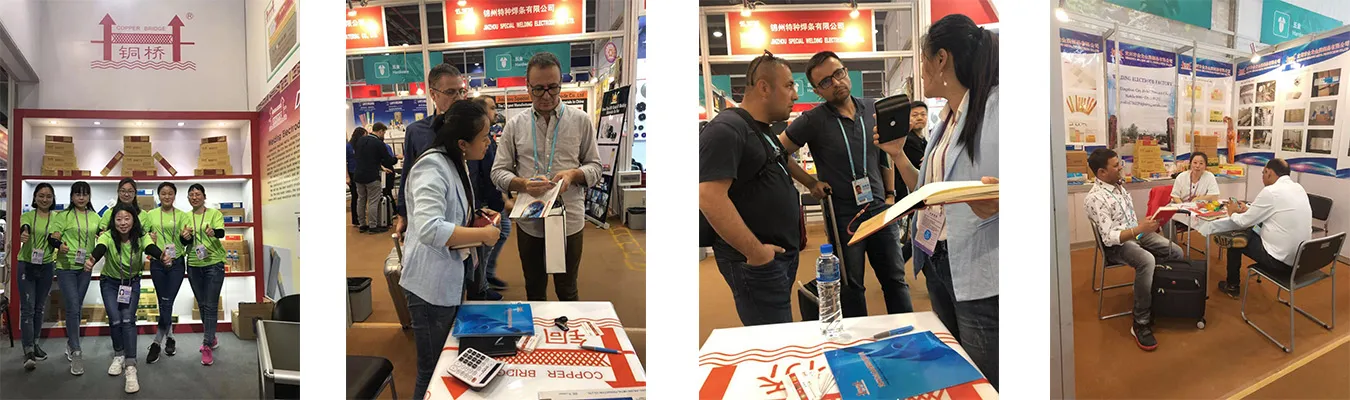
Steel fragments, broken crucial components, or hefty industrial equipment—each scenario demands a welding solution that guarantees durability.
The 312 welding rod comes into play particularly when welding alloy or stainless steel to carbon steel. These rods are an excellent choice for fabricating equipment that must endure harsh environments as they offer superior resistance to corrosion and wear. The utility of the 312 welding rod is magnified in industries such as petrochemicals, shipbuilding, and automotive sectors, where diverse metal joining is frequent.
Experts often recommend the 312 welding rod for its excellent tensile strength and ductility. With a tensile strength often reaching up to 120,000 psi, these rods provide high-quality welds that are less prone to cracking under stress—an essential factor when welding steel that might undergo distortion or when working with thicker materials. Their ability to absorb the stress posed by thermal expansion and contraction is pivotal during the heating and cooling cycles of welding, ensuring the structural integrity of the welded join.
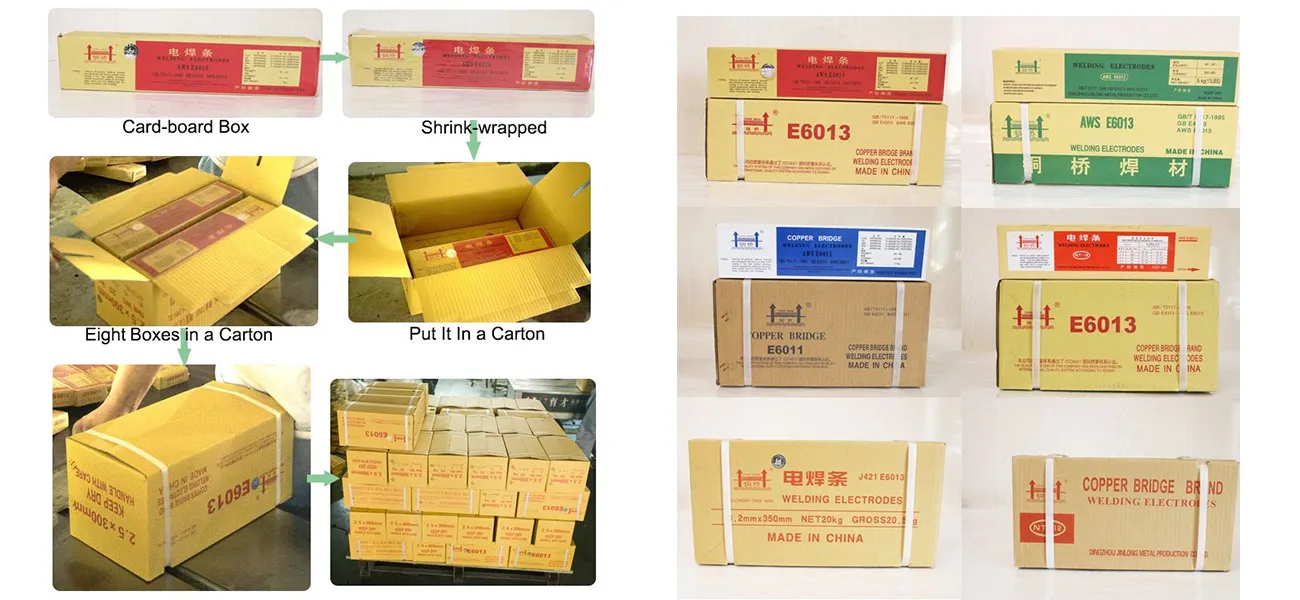
Professional welders value the 312 welding rod for its adaptability in high-pressure and high-temperature environments. Whether it's repairing tools, forging outdoor structures, or dealing with pressure vessels, the 312 welding rod’s capacity to create robust, reliable bonds is unmatched. Its high ferrite content in the austenitic matrix is instrumental in countering thermal fatigue, which makes it favorable for components undergoing repeated thermal cycles.
From a practical perspective, welders without extensive experience appreciate the 312 welding rod’s user-friendliness. This rod allows clean and smooth welding with minimal spatter, which makes it easier to control the welding pool and achieve a neat finish. This factor is critical for beginners trying to gain proficiency and for professionals aiming for efficiency in tight production schedules.
what is 312 welding rod used for
Safety, a paramount concern in welding, is well addressed with the 312 welding rod. When used correctly, it minimizes the emission of harmful fumes compared to other welding materials. This aspect assures welders of a healthier working environment, which is an important factor in maintaining long-term occupational health and well-being in industrial settings.
The 312 welding rod does not only benefit from practical handling and execution, but its economic advantage is notable, too. Its longevity and ability to produce superior quality welds decrease the need for frequent replacements or costly repairs, providing a cost-effective solution for businesses that prioritize both quality and budget-conscious practices.
In a constantly evolving industrial landscape, where the demand for specialized and efficient materials is ever-increasing, the 312 welding rod stands out as a significant resource. Its robust characteristics and wide range of applications make it a must-have in the toolkit of professional welders. It provides a reliable, expert-level solution to complex welding challenges, ensuring the safety and durability of crucial metallic infrastructures across various industries.
With its proven track record, the 312 welding rod exemplifies the peak of welding technology, marrying strength and versatility to meet modern demands efficiently. It's not only a testament to the advances in welding technology but also an assurance of delivering optimal performance when it matters the most.