Choosing the right welding rod is crucial for achieving optimal results when working with cast iron. Cast iron, due to its high carbon content and inherent brittleness, presents unique challenges during the welding process. Therefore, the selection of an appropriate welding rod becomes crucial for ensuring structural integrity and longevity in the repaired or fabricated piece.
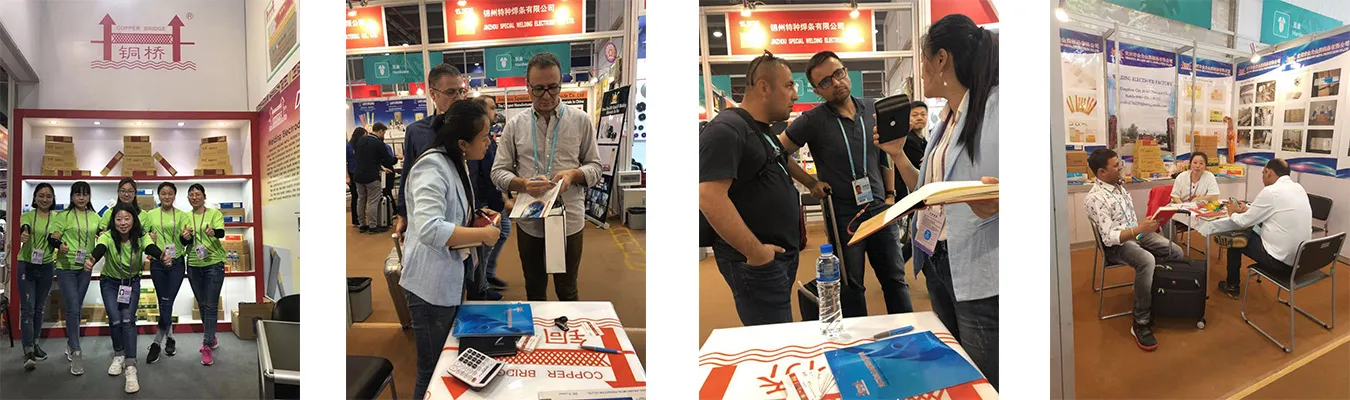
When working with cast iron, nickel-based rods are commonly recommended. Nickel rods, such as ENi-CI or ENiFe-CI, are popular due to their compatibility with cast iron. These rods offer excellent results because they provide a weld bead that adheres well to cast iron while reducing the risk of cracking, a common issue due to the material's tendency to expand and contract. The use of nickel rods also minimizes the risk of creating a hardened zone in the heat-affected area, which is a potential source for future cracks.
ENi-CI rods, primarily composed of nickel, are ideal for cold welding processes. They reduce thermal stresses that could lead to cracking by their low expansion properties. These rods are highly malleable, allowing the weld to absorb expansions and contractions, which is crucial in applications involving high temperatures.
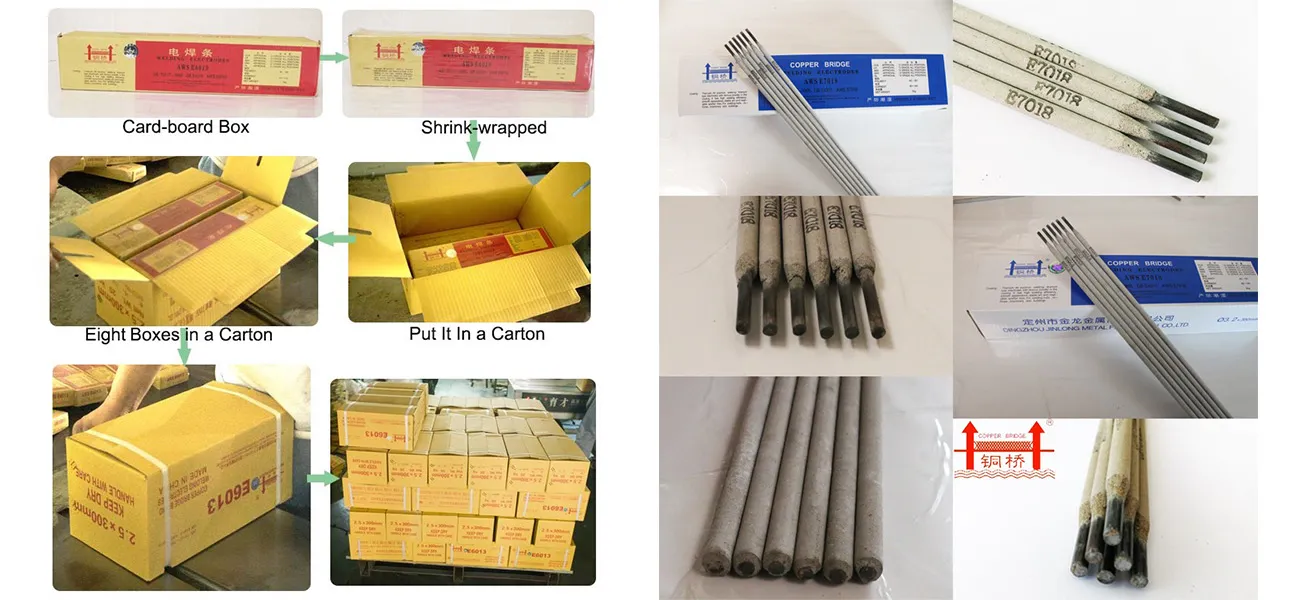
On the other hand, the ENiFe-CI rods are composed of nickel and iron, offering a balance between strength and ductility. These are more versatile than pure nickel rods and provide a slightly stronger weld. Due to the added iron content, these rods can accommodate different types of cast iron better, including those with a higher degree of impurities.
For optimal results, preheating the cast iron before welding is advised. Preheating reduces temperature gradients, helping to mitigate the induced stress within the iron that can lead to cracking. After welding, a slow cooling process is essential. It's advisable to wrap the workpiece in an insulating material to allow gradual cooling and reduce thermal shock.
welding rod used for cast iron
Furthermore, the technique used is just as important as the choice of rod. Employ a low-heat input method, such as using short, frequent passes instead of long, continuous welds. This approach allows each weld to cool slowly, reducing the cumulative heat-induced stress on the surrounding material.
For beginners and even experienced welders, practicing on a similar spare piece of cast iron is recommended. This practice helps in calibrating the technique and understanding the material response to the heat and rod combination. Additionally, consulting resources such as welding manuals and craft-specific forums can provide invaluable insight into the nuances of cast iron welding.
The significance of surface preparation can't be stressed enough. Properly cleaning the surface to remove any oils, rust, or contaminants ensures better weld penetration and adherence. Employ tools like grinders or wire brushes to prepare the surface adequately. In some cases, machining may be necessary to achieve proper fitting before the welding process begins.
Manufacturers and welders continue to innovate and adapt to the nuances of working with cast iron. Trust in products that rigorously test their rods and adhere to industry standards, ensuring they offer the highest quality and reliability for challenging welding applications. Choose suppliers that provide not only products but comprehensive support and guidance on best practices.
In conclusion, welding cast iron requires a multidimensional approach combining the right materials, meticulous preparation, and precise technique. By focusing on these areas, you ensure not only the success of the immediate project but also the durability and reliability of the weld over the lifetime of the repaired or fabricated piece. Whether you are an aspiring welder or seasoned professional, understanding these principles will enhance your craft and ensure your projects are completed to the highest standards of quality and safety.