Choosing the right welding rod size for thin metal is a critical decision that can greatly affect the quality and integrity of your welds. For anyone venturing into welding projects involving thin metal, such nuances can mean the difference between a perfect weld and a compromised structure.
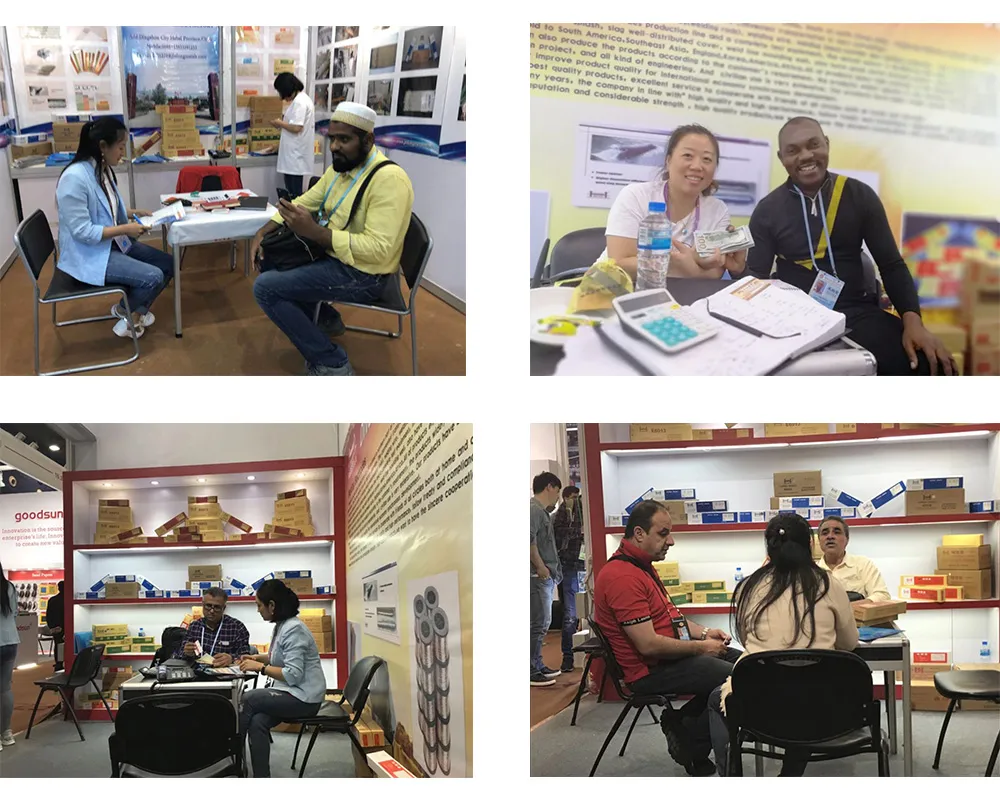
Understanding Thin Metal Welding Welding thin metal requires a delicate touch and an eye for detail. The metals in question, often ranging from 18 to 24 gauge, can be prone to warping, burning through, or improper fusion if incorrect welding parameters are used.
The welding rod size plays a pivotal role in ensuring a smooth, defect-free join. Typically, thin metals require smaller diameter welding rods that can deliver the precise level of heat and control needed.
Selecting the Right Rod Size For thin metal, welding professionals often opt for rods ranging from 0.025 inches to 0.035 inches in diameter. These sizes are small enough to manage the low heat input needed, and they offer excellent control over the weld pool. One common choice for many is the 0.030-inch rod, a size that offers a good balance of control and penetration, minimizing the risk of burning through the material. This size is particularly effective when used in conjunction with MIG (Metal Inert Gas) welding, which provides the gas shielding needed to protect the weld from atmospheric contamination.
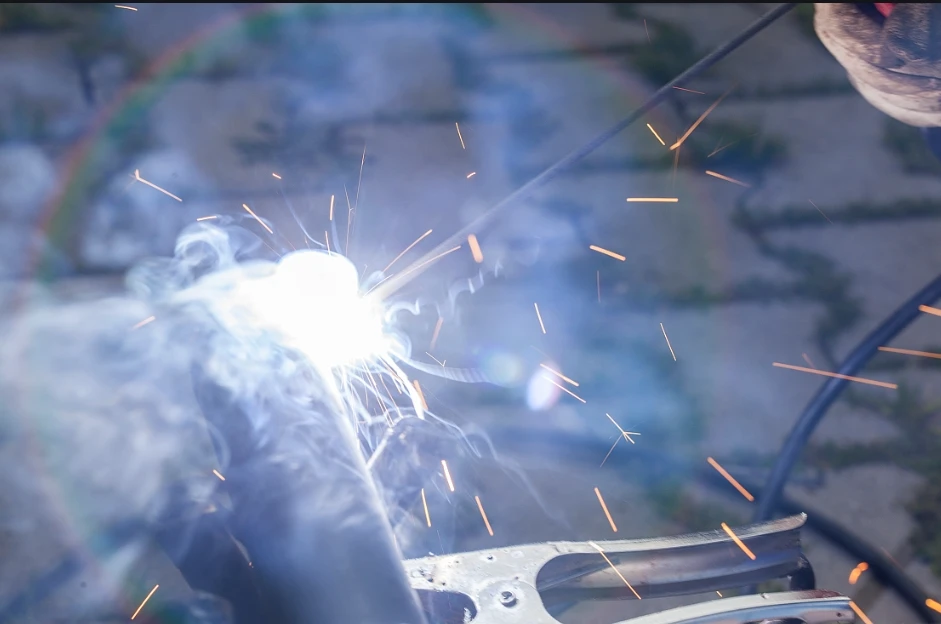
Real-World Experience and Insights Many expert welders recount the challenges associated with welding thin metals. The consensus is clear practice makes perfect. It's important to experiment with different rod sizes to see which provides the best results for your specific project and material type. For instance, welding professionals who have worked extensively with automotive panels often advise the use of a 0.035-inch ER70S-6 MIG wire, praised for its forgiving nature and adaptability to imperfections on thin surfaces. By sharing real-world applications and insights, newcomers can gain practical knowledge that enhances their welding skills.
Expert Recommendations on Techniques Aside from choosing the correct rod size, expert welders emphasize the importance of mastering technique. Use of a pulsing method can help control the heat input and minimize burn-through when working with thinner metals. Additionally, maintaining a clean surface is crucial—the presence of rust, paint, or oil can cause porosity and weaken the weld.
welding rod size for thin metal
Authoritative Advice Trust the guidance of certified welding professionals and organizations such as the American Welding Society (AWS). Resources on their platforms provide specifications and detailed tutorials on the appropriate settings and rod selections for various materials. Their certification processes ensure that industry best practices are followed, instilling trust and reliability in their recommendations.
Building Trust Through Quality Workmanship Trustworthiness in welding thin metal also stems from the results you achieve. Ensuring that welds are not only structurally sound but aesthetically pleasing can build a reputation for quality and reliability. Taking the time to inspect each weld, make necessary adjustments, and continually hone your skills will earn you a reputation as a trusted craftsperson.
Looking Forward As technology evolves, so do the tools and rods available for welding thin materials. Keeping abreast of industry trends and innovations can provide access to new products that further enhance the ease and efficiency of your welding projects. Utilizing forums, workshops, and continuous learning means you're not only using the best welding techniques today but are prepared for the innovations of tomorrow.
In the end, while the choice of a welding rod for thin metal might seem a small detail, it’s these precise decisions that lead to exemplary craftsmanship. Welder’s who consistently demonstrate expertise, present authentic advice, and uphold industry standards are best positioned to succeed in their endeavors.