Choosing the right welding rod size is crucial for achieving strong, professional welds and ensuring project success. With years of industry experience, I’m here to provide you with insight into selecting the ideal welding rod size for your specific applications, taking into account material types, thickness, and desired welding positions.
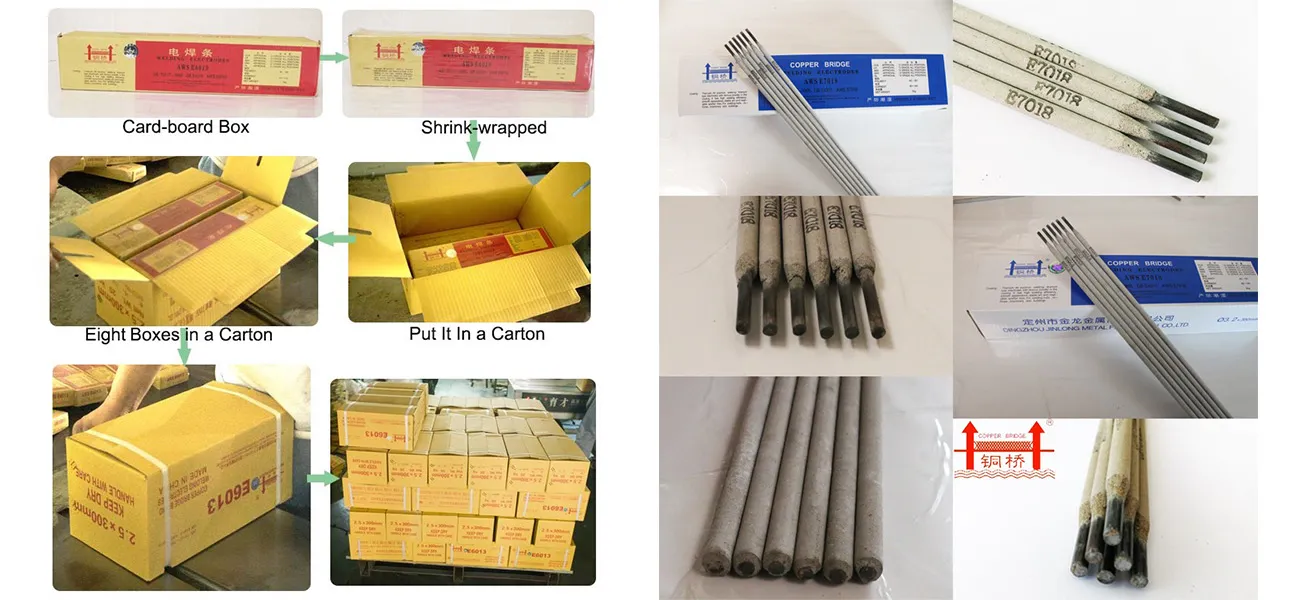
Welding rod size is significant as it directly affects the weld's appearance, strength, and overall integrity. As a rule of thumb, the welding rod size should match the thickness of the material. For instance, a 3/32 inch welding rod is typically used for thin materials up to 1/8 inch in thickness, while a 1/8 inch rod is more appropriate for material thickness up to 1/4 inch. However, it is essential to consult the specifications provided by the rod manufacturer because recommendations can differ based on the rod material and coating.
The material to be welded also plays a critical role in determining rod size. For mild steel, common choices include E6010 and E7018 rods. E6010 is often preferred for penetration, making it suitable for root passes, especially in pipes, whereas the E7018 provides a clean, smooth finish on mild steel. For aluminum projects, you might opt for rods like the E4043, which generally requires larger rod sizes to handle its distinctive properties effectively.
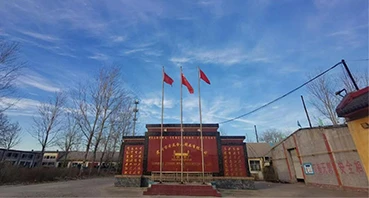
Welding position is another variable influencing rod size. For instance, overhead and vertical positions typically require a smaller diameter rod. A smaller rod provides better control, reducing the risk of weld spatter and dripping, which is common in these challenging positions. In contrast, flat and horizontal welds allow using larger rod sizes, which can help achieve a more substantial weld in less time.
welding rod size
Skill level and equipment are additional considerations. Novice welders should start with smaller rods because they are easier to manage and control. As you gain proficiency, you can experiment with larger sizes to optimize efficiency and performance. Moreover, ensure your welding machine can handle the amperage required for the chosen rod size. An incorrect match can lead to underwhelming results like weak welds or excessive spatter.
Ambient conditions such as humidity or cold weather can also impact your choice. High humidity might necessitate using rods with moisture-resistant coatings to prevent hydrogen-induced cracking. Cold weather can make thicker materials more challenging to weld, compelling a smaller rod choice to allow for better control and heat management.
Ultimately, rod selection is a balance of these factors tailored to your specific project needs. It’s advisable to keep a selection of rod sizes on hand, allowing versatility across different projects and conditions. Regularly updating your knowledge about new materials and technologies in welding rods contributes to maintaining a competitive edge.
In conclusion, by fully understanding the interplay of material thickness, rod composition, welding position, skill level, and environmental conditions, you can achieve optimal results in your welding endeavors. Making informed choices based on this criteria not only enhances weld quality but also increases productivity and project success.