Understanding welding rod codes is crucial for professionals engaged in welding and metalworking. The unique classification system provides essential information about the rods, such as their material, intended use, and performance characteristics. This article demystifies these codes and offers valuable insights enhanced by real-world expertise and authoritative knowledge.
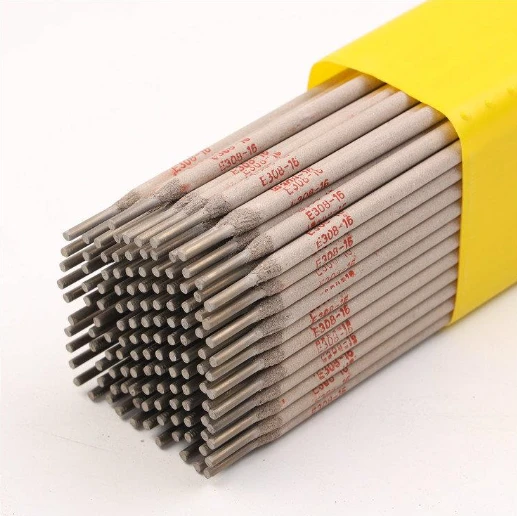
Welding rod codes are standardized by the American Welding Society (AWS) in the U.S. These codes serve as a universal language for welding professionals, ensuring consistent quality and performance expectations across different applications and geographical regions. A typical code is composed of letters and numbers, such as E6013, E7018, or E308L. Each component of the code carries specific meaning and implications for use.
The letter E in most rod codes denotes an electrode, indicating the rod's primary function in welding. Electrode rods conduct electrical current, generating the heat needed to melt metals and create a bond. This classification sets the stage for understanding the numerical part of the code. The first two digits typically indicate the tensile strength of the weld metal. For instance, in an E6013 rod, the '60' signifies a tensile strength of 60,000 psi. This measurement informs welders of the strength and resilience of the bond, an essential consideration when working with different metals and applications.
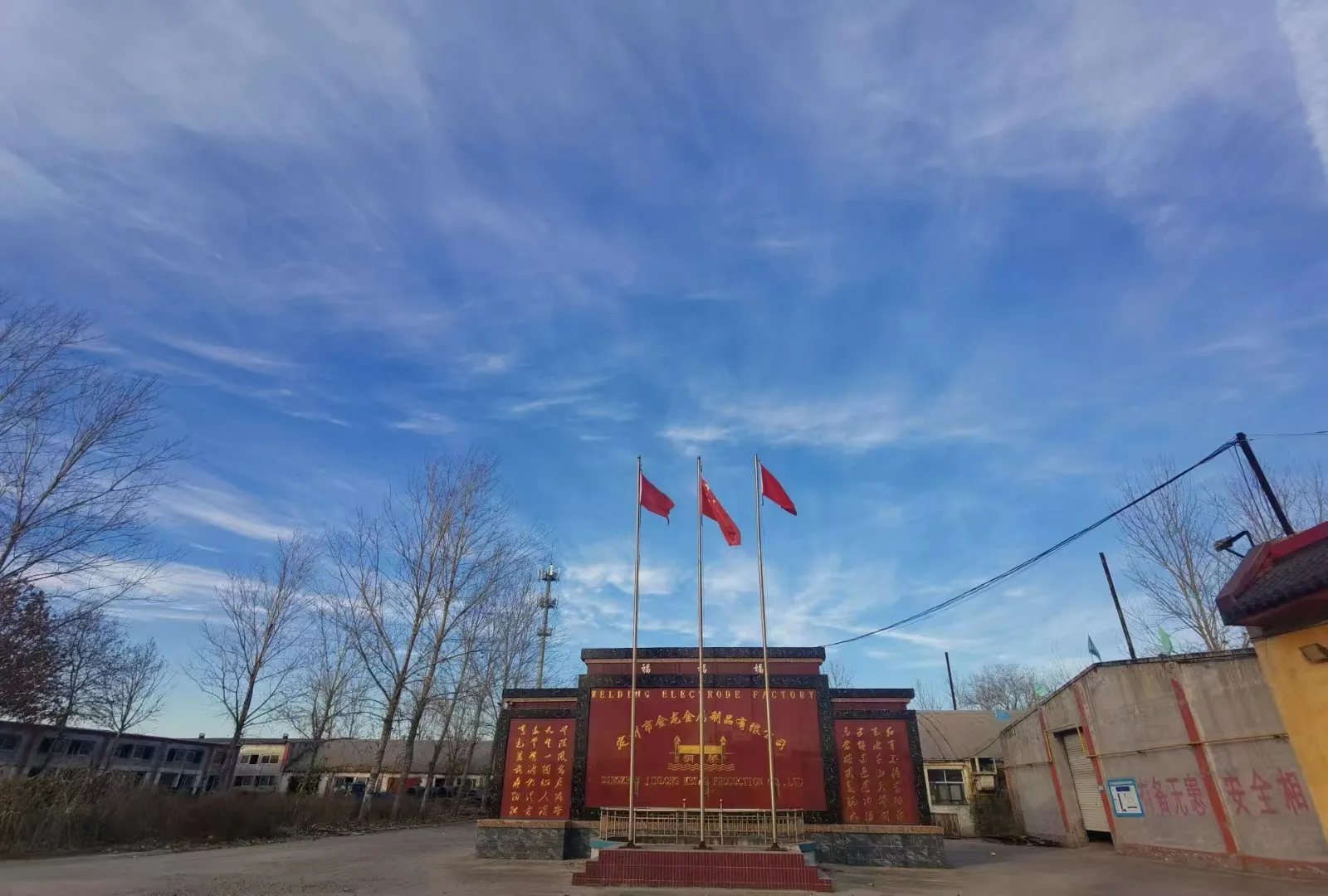
The third digit signifies the rod's position capabilities, showing whether it is suitable for flat, horizontal, vertical, or overhead welding. It denotes flexibility in application. For example, a '1' indicates that the rod is versatile across all positions, which is crucial in dynamic job sites where orientation cannot be controlled. Conversely, a '2' suggests the rod is suitable for flat or horizontal positions only.
welding rod codes
The final number refers to the coating type and the type of current suitable for the rod. This last piece is critical, as it dictates how a rod will perform under various operational conditions, influencing factors like arc stability and slag detachability. In an E7018 rod, the '8' signifies that the rod is compatible with both AC and DC welding, has an iron powder low hydrogen coating, and provides good deposition and mechanical properties. Such characteristics make it preferable for structural welding jobs in bridges or buildings where high impact toughness is necessary.
The materials involved in these rods are another layer of complexity. Stainless steel rods, for instance, have their own set of standards and codes, often distinguishing not just the strength and position but also the alloy type. A rod like E308L suggests a low-carbon stainless steel electrode that provides corrosion-resistant welds. This is critical when working in environments exposed to moisture or chemicals, where corrosion can be a significant concern.
Possessing a deep understanding of welding rod codes not only empowers welders in selecting the right product for their specific job but also enhances the safety and strength of the welding application. Selecting the wrong rod can lead to weak welds, increased costs due to rework or part failure, and potentially hazardous failures during operation. Thus, this knowledge directly feeds into the Experience and Expertise pillars of SEO content, ensuring that those consulting such resources obtain the wisdom required to make informed decisions.
Moreover, welding codes are continually updated to reflect advances in technology and materials, underscoring the Authoritativeness of sources that maintain current information. Websites providing up-to-date, comprehensive insights offer unparalleled Trustworthiness, becoming invaluable resources for professionals seeking to remain at the cutting edge of their field. By harnessing this understanding, welders can achieve superior results, optimizing the integrity and functionality of their work.