Choosing the right welding electrode can significantly impact the quality and efficiency of a welding project. A well-selected electrode not only ensures strong and durable welds but also optimizes project time and cost. Below, we drawn from extensive industry experience to create a comprehensive welding electrode selection guide, providing expertise with detailed insights into selecting the perfect electrode for your specific application.
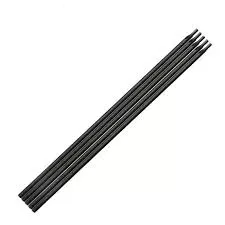
Welding electrodes serve as a crucial component in the welding process, acting as a current-carrying conductor and filler material. The type you choose can determine the mechanical properties of the weld, the type of welding current required, and ultimately, the success of your project. Matching the electrode's characteristics with the welding job is vital for achieving high-quality results.
Firstly, consider the base material. The compatibility between the electrode and the base material influences the weld's integrity. Soft metals like mild steel typically pair well with electrodes such as E6010 or E6011 due to their deep penetration capabilities, which ensure a strong bond. For high-carbon steel or low-alloy materials, choose electrodes like E7018, known for providing excellent mechanical properties and toughness.
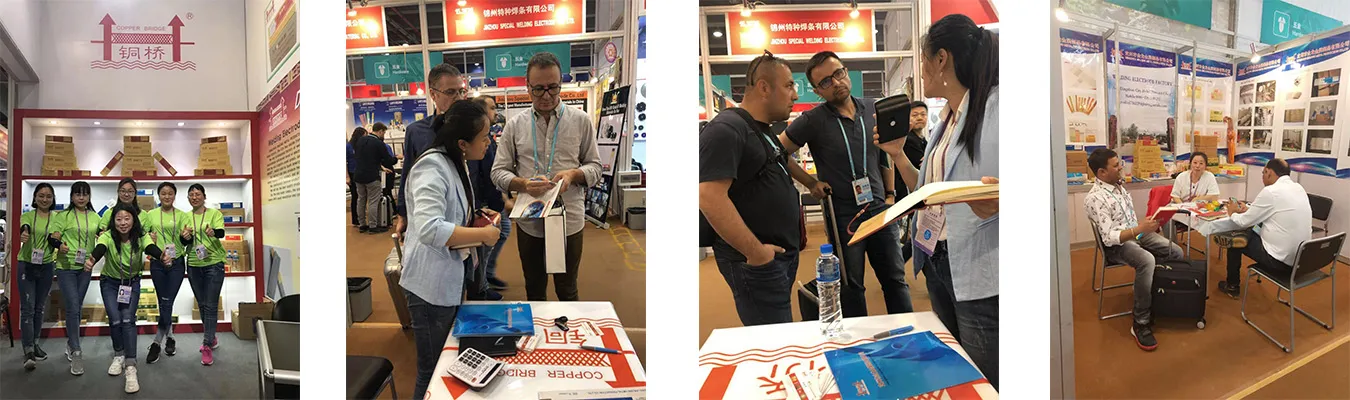
Next, analyze the joint design and position. If the work involves welding in awkward positions or on thin metals, opting for electrodes designed for all-position work, such as E6010 or E6013, is advisable. These electrodes offer ease of handling and control, which is essential in vertical or overhead welding.
Consider the welding environment. Factors such as temperature, humidity, and wind can affect weld quality. For outdoor or damp conditions, ensure to select electrodes that minimize moisture absorption like E7018 to prevent issues such as hydrogen-induced cracking. Electrodes with flux coatings that provide a protective gas shield are particularly beneficial in maintaining weld integrity in challenging environments.
welding electrode selection guide pdf
It's essential to account for the available welding equipment and power source. Different electrodes require specific types of current — AC, DC, or both. Verify that your welding machine is compatible with the electrode's requirements. For rural areas where access to three-phase power might be limited, choose electrodes that provide flexibility with power sources.
Economic factors can't be ignored. The cost of electrodes varies significantly. While high-quality electrodes may seem expensive, their efficiency and the superior quality of welds they produce can save money in the long term by reducing rework and downtime.
For beginners or those developing a new welding procedure, always refer to the manufacturer's specifications and guidelines. These documents often contain valuable information on the electrode’s ideal operating conditions, like amperage settings and travel speeds.
Finally, continuous learning and feedback integration form the backbone of optimizing electrode selection. Engage with industry forums, participate in welding expos, and consult technical sheets to stay updated on the latest technologies and electrode types.
Each welding project provides a unique opportunity to refine selection techniques and enhance welding expertise.
By employing this meticulous approach to welding electrode selection, the likelihood of achieving welds that are not only structurally sound but also efficient and economical increases substantially. With these tailored insights, one can navigate the complexities of electrode selection with confidence, ultimately leading to more successful welding endeavors.