The welding electrode rod market is a dynamic sector with prices subject to fluctuations influenced by a myriad of factors, making it crucial for buyers to stay informed. My personal journey within this industry has provided me with valuable insights into how pricing works and what prospective buyers need to consider.
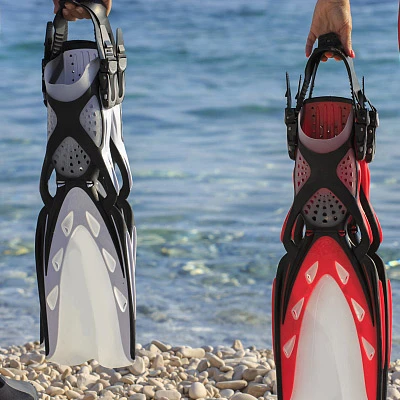
Having spent years working alongside manufacturers and suppliers, I've seen firsthand the precise factors that contribute to the cost of welding electrodes. Raw material costs are perhaps the most significant determinant. As welding rods are typically made from materials such as mild steel, stainless steel, and other alloys, any changes in the global price of these metals directly impact electrode pricing. I've noted that fluctuations in steel prices, often driven by factors like international trade policies and market demand, are particularly impactful.
Another pivotal aspect affecting pricing is the electrode coating. Different coatings, such as rutile, basic, and cellulose, cater to varied welding requirements and environments. For instance, premium electrodes with specialized coatings that ensure better performance, even in challenging conditions, naturally command higher prices. Through years of experience, I've repeatedly observed that investing in quality coatings can significantly improve welding outcomes, justifying the higher cost.
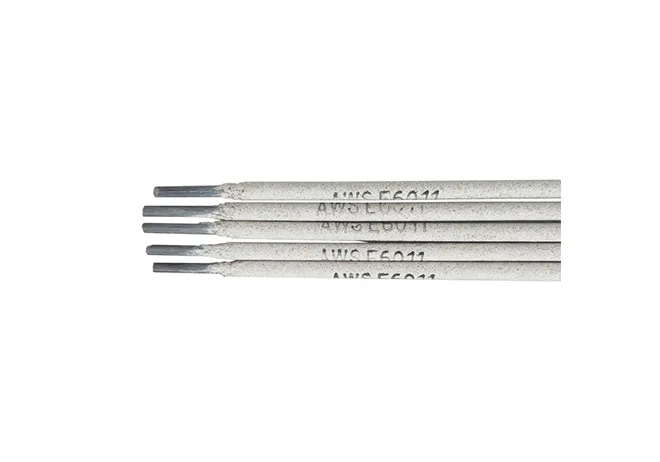
Furthermore, the manufacturing process itself plays a role in pricing. High-tech processes that ensure precision and consistency, along with stringent quality control measures, often add to production costs. Having participated in manufacturing audits, I've seen how companies that invest in advanced technology and skilled labor provide products that offer superior performance, albeit at an increased price point.
welding electrode rod price
It's also evident that geographical factors can affect electrode pricing. For example, locally produced electrodes may be cheaper due to reduced transportation costs. However, the trade-off might come in the form of limited availability of certain premium products that need to be imported. My interactions with global suppliers have highlighted this trade-off, where quality and cost must be carefully balanced depending on geographical logistics.
Market dynamics, including supply-demand scenarios, cannot be ignored. During peak construction seasons or major infrastructure projects, the demand for welding electrodes can surge, leading to price hikes. I've advised numerous clients to plan their procurement ahead of these spikes to mitigate cost increases. Awareness of such trends is crucial for those deeply involved in project planning and procurement.
As a final note based on my extensive experience, it's important to build relationships with reputable suppliers. A trustworthy supplier not only ensures quality but often provides insights into potential price changes, allowing for more strategic purchasing decisions. By cultivating these relationships over time, I've managed to secure better deals and reliable products for my clients.
Ultimately, understanding the nuances of welding electrode rod pricing requires a blend of industry knowledge, market awareness, and strategic planning. Buyers who leverage these insights can make informed decisions that balance cost with performance, ensuring optimal results for their welding projects.