Understanding the intricate world of welding can be a daunting task, particularly when it comes to choosing the right welding electrode. The welding electrode number chart serves as a critical tool in this decision-making process, guiding both seasoned professionals and new welders to the appropriate selection. The following article delves into the essential components and deciphering the seemingly complex data of a welding electrode chart while drawing from expert insights and years of technical experience.
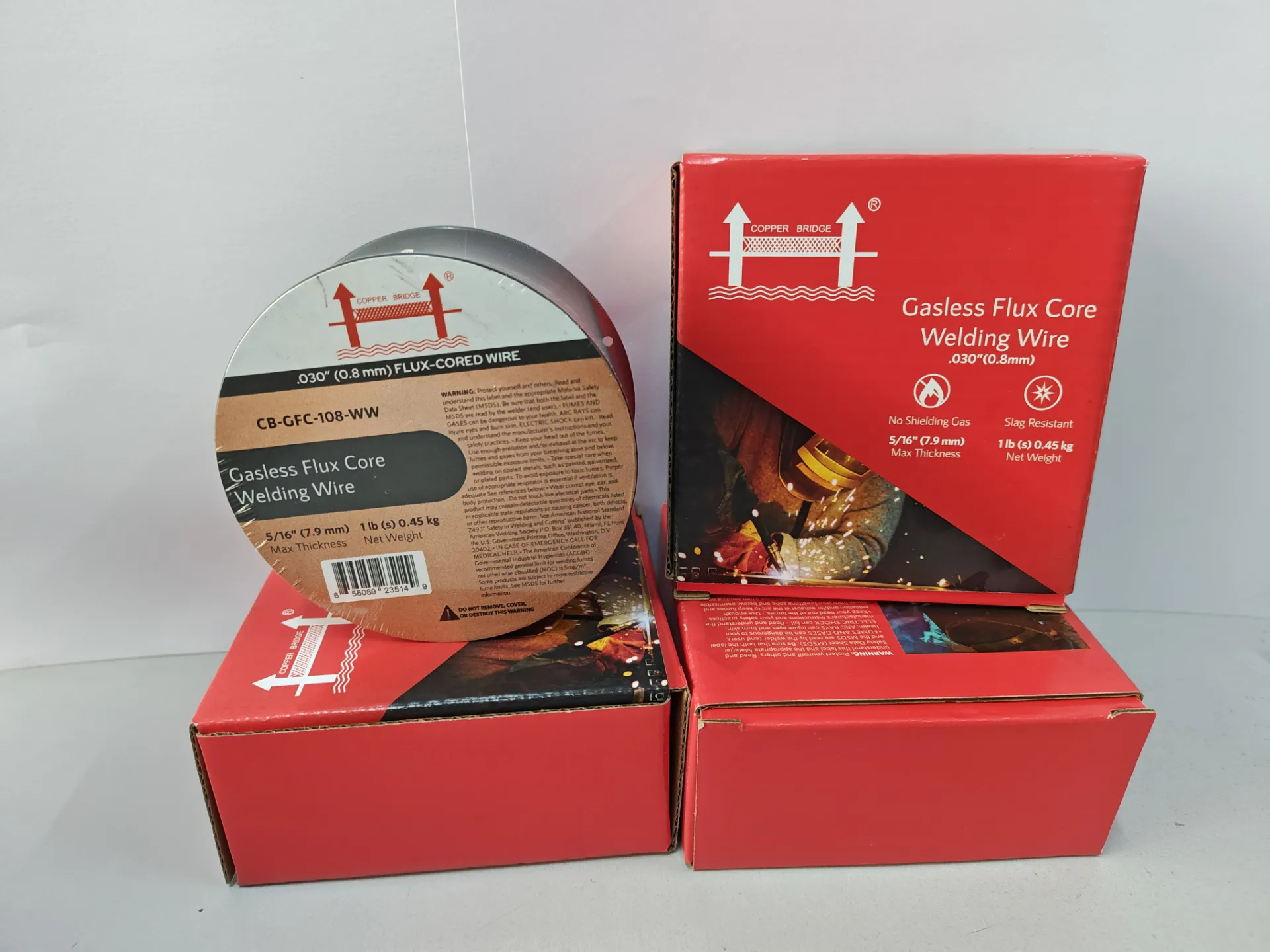
Welding electrodes are categorized by specific numbers, each representing unique properties and capabilities. This coding system, governed by organizations such as the American Welding Society (AWS), ensures clarity and uniformity in electrode specifications. For instance, an E6013 electrode reveals significant information at a glance. The E denotes a consumable electrode, while the following numbers provide insights into tensile strength, positions, and coating type.
The “60” in E6013 stands for the tensile strength of 60,000 pounds per square inch (psi), indicating the metal's ability to withstand stretching forces. Understanding this metric is important for ensuring that the welded joint can sustain the anticipated load without failure. The next digit, 1, specifies the positions in which the electrode can be used, with 1 signifying all positions. This versatility is crucial for projects that require welding in a variety of orientations.
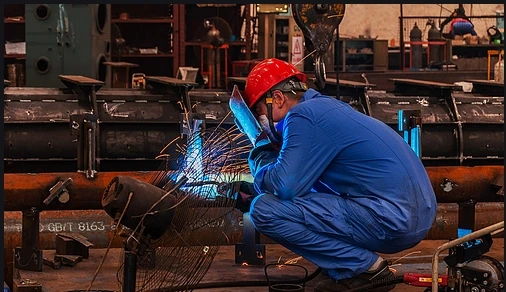
The final digit, “3,” indicates the specific coating and compatibility with the welding current type. The number 3 suggests that the electrode is primarily for use with AC or DC currents, making it versatile for alternating current applications.
Navigating an electrode number chart requires not only understanding these codes but also applying them to practical scenarios. For instance, constructing bridges or pipelines demands electrodes with higher tensile strength ratings like E7018, which offers 70,000 psi. Moreover, the selected electrode must accommodate the welding position and work environment, requiring expert assessment of project needs.
welding electrode number chart
Experience shows that selecting the correct electrode can significantly impact the quality and efficiency of a welding project. Professionals emphasize considering factors such as the base metal type, thickness, desired welding finish, and environmental conditions. For instance, moist or windy settings may influence the coating choice to ensure optimal performance.
Understanding welding electrode charts also extends beyond just selection. It involves rigorous adherence to safety and quality standards. Valid credentials from industry bodies affirming an electrode manufacturer’s quality control complement a welder's skillset, reinforcing the trustworthiness of the outcomes. This assurance in electrode reliability is crucial, as poor-quality electrodes can lead to dangerous structural weaknesses.
Industry experts continually stress the importance of staying updated with advancements in electrode technology and numerical specifications. As welding techniques evolve, manufactures frequently update and refine electrode specifications to accommodate new materials and techniques, underscoring the need for informed, continuous learning.
The welding electrode number chart serves as a cornerstone in welding tasks, allowing for precise selection that ensures strong, durable, and safe welds. This reliable system, combined with skilled craftsmanship and adherence to standardized codes, forms the foundation for successful welding endeavors across diverse industries. Through a deep understanding of these pivotal numbers, practitioners can execute their craft with the assurance of expertise and authority, tailoring their approach to meet the unique challenges of each project efficiently.