When it comes to achieving the perfect weld, particularly in vertical positions, professionals in the welding community often discuss the significance of choosing the correct amperage.
One of the most discussed electrodes for vertical welding is the 7018. This versatile and widely-used electrode is renowned for its strength, ductility, and ease of use, but mastering the appropriate amperage settings is crucial for optimal performance.
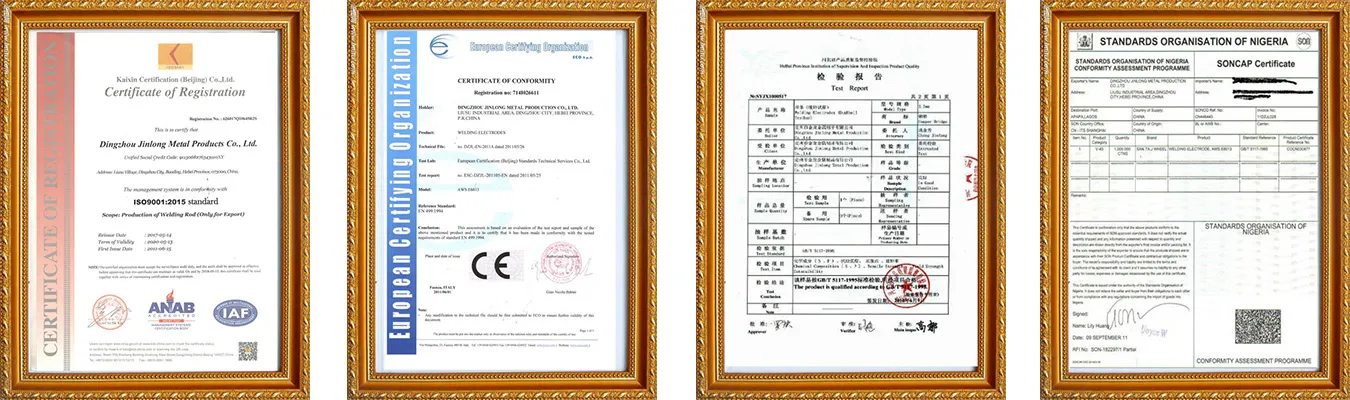
Navigating the nuances of welding, particularly with the 7018 electrode, involves a comprehensive understanding of variables that affect the outcome, including the material type, thickness, welding position, and, importantly, amperage settings. Experienced welders often suggest that for vertical welding, starting at a lower amperage and gradually increasing can lead to more controlled and visually appealing welds. When using the 7018 electrode, amperage settings can vary significantly; broad recommendations suggest starting between 90 to 150 amps, but achieving precision requires more than a basic guideline.
One of the foundational aspects of expert vertical welding is recognizing the role of polarity—7018 electrodes are typically used with a DC positive current. This polarity is crucial as it influences the penetration depth and arc stability—both vital for achieving high-quality welds in vertical positions. Amperage adjustments are contingent upon maintaining this effective polarity to ensure the electrode effectively melts the base metal and achieves sufficient fusion.
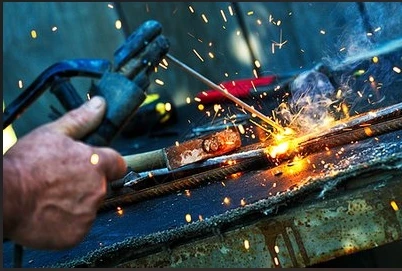
Professional welders often emphasize the trial-and-error nature of perfecting vertical welding. Each weld session can be influenced by factors such as the welding environment, metal cleanliness, and even the welder's technique. With the 7018 electrode, the vertical-up technique demands careful amperage control to avoid defects like slag inclusions. A controlled amperage setting allows the welder to deposit metal efficiently, reducing the risk of overheating and minimizing splatter, which can be more prevalent when welding vertically.
In practice, the starting amperage for vertical welding with the 7018 electrode may also depend on the welder's personal technique and the equipment used. For instance, newer welding machines equipped with advanced technology offer settings that automatically adjust the arc force, which can simplify the process for beginners but requires expert settings for veterans aiming for perfection. The utilization of these features can enable welders to fine-tune the amperage settings further, adapting to their specific needs and achieving a smoother, more consistent weld bead.
vertical welding 7018 amps
Understanding the subtleties of amperage adjustments involves analyzing the weld puddle's behavior—a critical aspect of vertical welding. The ideal amperage allows for a puddle that is cohesive and easy to manipulate, avoiding the unsightly sagging or dripping that can occur with excessive heat. Additionally, an informed approach to amperage adjustment can ensure a balanced deposition rate, crucial for maintaining a uniform weld bead along the vertical axis without compromising structural integrity.
Industry-specific knowledge further enhances the effectiveness of vertical welding with the 7018 electrode. Manufacturers often provide recommended amperage ranges and guidelines on electrode packaging. However, industry experience reveals that these are starting points rather than strict rules; welding professionals often adjust these parameters based on their unique requirements, accumulated expertise, and the specific welding scenario.
The prowess of an authoritative welder is demonstrated not only through precise amperage adjustments but also through the ability to adapt these settings seamlessly in response to environmental changes or project specifications. Trust in the weld's strength and reliability stems from a welder's capacity to maintain consistent quality control throughout the operation.
Ultimately, mastering vertical welding with 7018 electrodes involves an amalgamation of theoretical knowledge, hands-on experience, and a laser-focused approach to amperage adjustment. The consensus among experts is clear—while amperage settings form the backbone of a successful weld, the true mastery of the craft stems from a welder’s continued learning and adaptation, ensuring that each weld is executed with precise authority and expertise. In the rapidly evolving domain of welding technology, these foundational truths remain steadfast, underscoring the trusted skillset required to execute exceptional vertical welds with proficiency and confidence.