Navigating the world of welding requires a deep understanding of the various types of welding rods available, each serving distinct purposes and bringing unique advantages. A detailed guide on the types of welding rods is an invaluable resource for both novice and expert welders striving to enhance their craft. This exploration delves into the characteristics, applications, and benefits of these essential tools, ensuring welders choose the optimal rod for their specific projects.
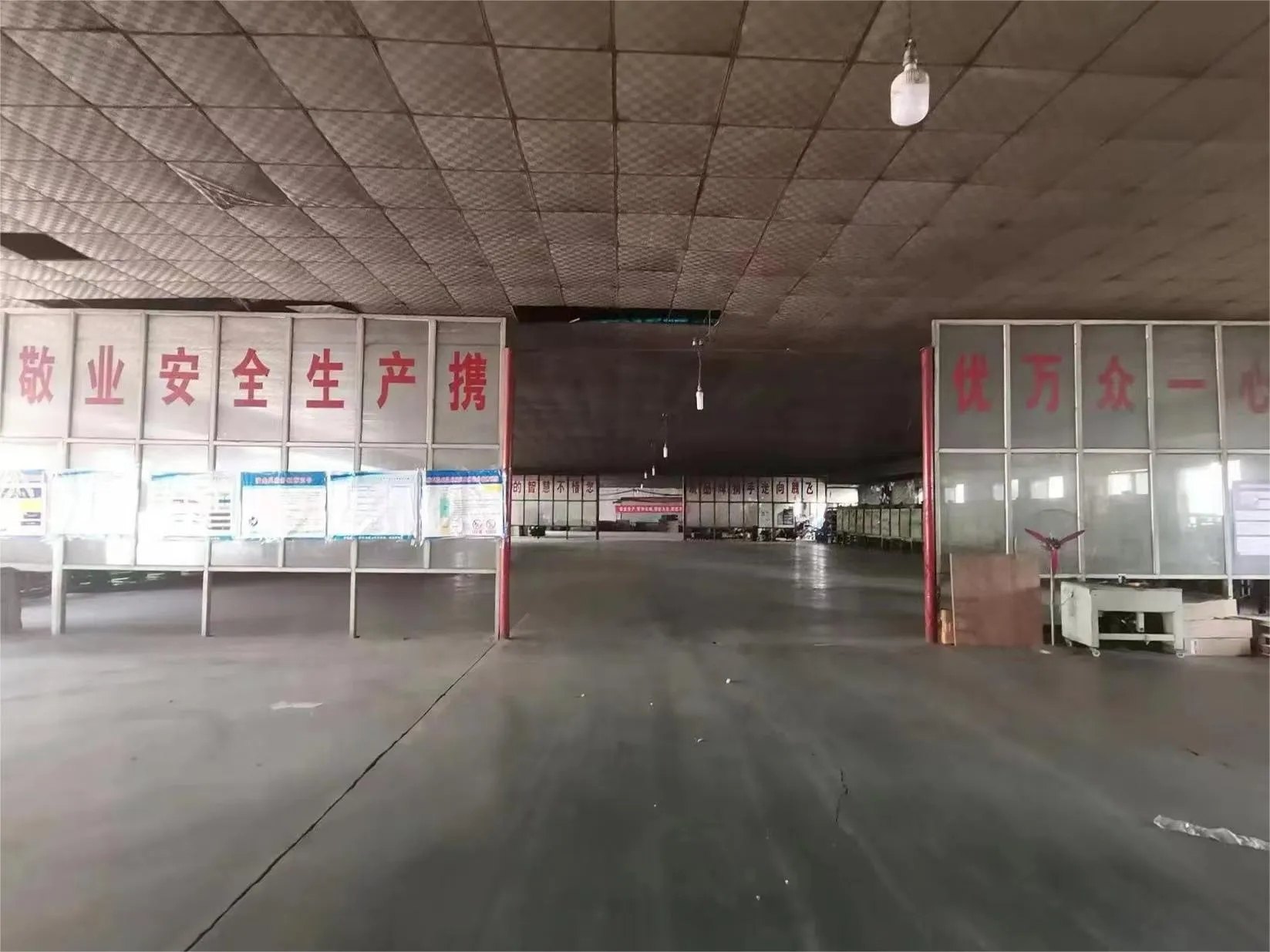
Welding rods, also known as filler metals or electrodes, are integral in the welding process, bridging the gap between two pieces of metal. They are classified mainly into consumable and non-consumable types, with each category offering distinct functionalities. Consumable electrodes, such as those used in shielded metal arc welding (SMAW) or stick welding, melt during the process and provide filler material. Non-consumable electrodes like tungsten, used in tungsten inert gas (TIG) welding, do not melt, and instead facilitate the arc needed to join metals while relying on a separate filler.
One of the most commonly utilized welding rods is the E6010. Known for its deep penetration and fast freeze, this rod is ideal for pipe welding and maintenance work, particularly useful when dealing with unclean surfaces. Its ability to weld in all positions makes it versatile, though it requires a skilled hand due to its demanding nature.
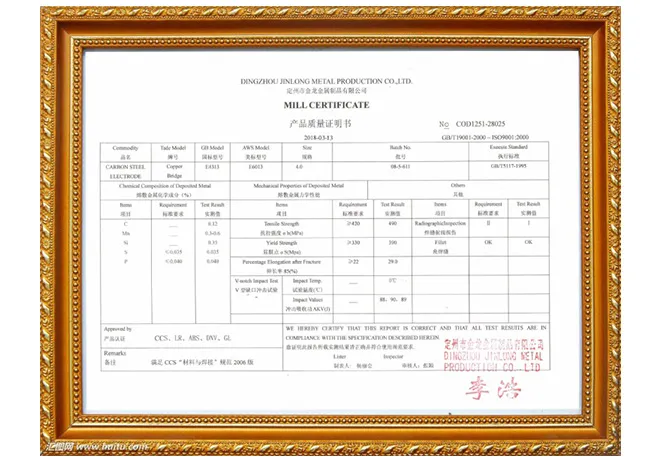
The E6011 rod carries similar penetration capabilities to the E6010 but operates with both AC and DC currents, offering greater flexibility. This electrode is favored for its performance on vertical and overhead welding projects and its tolerance to rust, paint, and grease. This adaptability makes it a prime choice for fieldwork requiring less surface preparation.
For projects requiring a smoother finish, the E6013 is the go-to electrode. Its versatility in terms of application and ease of use, even for novice welders, makes it widely popular. Producing a soft arc, the E6013 is suitable for sheet metal and ornamental iron work, providing aesthetically pleasing weld beads.
types of welding rods pdf
E7018 rods are paramount for structural projects demanding robust, high-strength bonds. They produce low hydrogen welds, reducing the risk of cracking in the weld metal. The E7018 is particularly favored in the fabrication of bridges and buildings, where strength and reliability are non-negotiable.
In specialty applications, stainless steel projects call for rods like the E308L, designed for welding similar chrome-nickel alloys. This rod ensures corrosion resistance, crucial in environments exposed to high temperatures or harsh chemicals, making it ideal for food industry equipment and chemical storage tanks.
Aluminum welding is another area requiring specialized electrodes. The E4043 is a standard choice for various aluminum alloys, offering excellent corrosion resistance and good mechanical properties, suitable for automotive parts and equipment repair.
Choosing the correct welding rod is not a matter of trial and error but an exercise in precision and knowledge. Factors such as the material composition, welding position, and environmental conditions heavily influence the decision. Proper selection not only ensures a seamless and strong weld but also enhances the overall quality and durability of the finished product. As technology advances, welders must stay informed of emerging trends and materials to maintain competency and efficiency in their field.
In conclusion, understanding the diverse types of welding rods is crucial for anyone involved in welding, whether in industrial settings, artistic endeavors, or routine repairs. By appreciating the unique characteristics and advantages each rod offers, welders can optimize their results, ensuring the longevity and integrity of their work while fostering trust and authority in their craftsmanship. This knowledge not only underscores the welder's expertise but also builds confidence in the quality of their projects, demonstrating a steadfast commitment to excellence.