Welding electrodes play a critical role in the productivity and quality of welding projects. Selecting the right electrode can influence the strength and durability of the weld, so understanding the different types and their uses is essential for any welding professional or enthusiast.
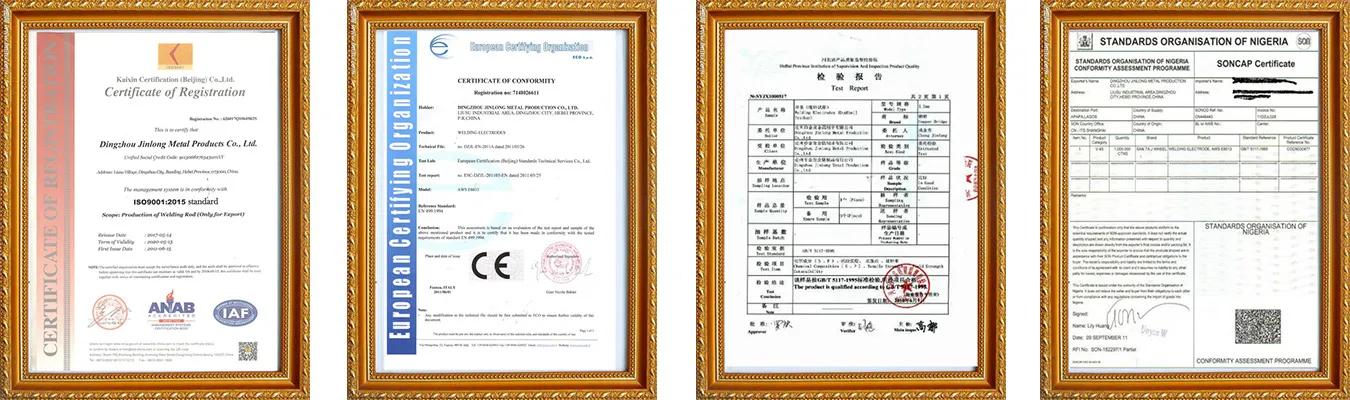
One of the most widely used electrodes is the E6010, known for its deep penetration ability, making it ideal for pipe welding and situations requiring root passes. E6010 is often employed in industries that demand high reliability, such as construction and shipbuilding, due to its versatility and ability to perform well on dirty or rusty surfaces. Professionals appreciate that while it requires a skilled hand due to its fast-freezing slag, the results are consistently reliable when executed properly.
E6011 electrodes share similarities with E6010 but come with additional flexibility, enabling use with AC power sources. This adaptability makes E6011 a good choice for repair and maintenance work, where power sources can be unpredictable. Its ability to weld through contaminants like paint and rust without compromising the integrity of the weld makes it a preferred choice for automotive repairs in numerous body shops.
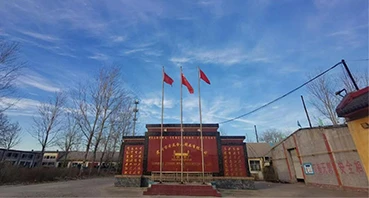
For projects that demand aesthetically pleasing welds with minimal spatter, E6013 electrodes are often recommended. Ideal for beginners due to their easy slag removal and smooth arc characteristics, E6013 is frequently utilized in household and light industrial applications. Their ease of use without specialized knowledge allows hobbyists to achieve professional-looking welds without extensive experience.
types of welding electrodes and their uses pdf
High tensile strength requirements in structural welding frequently necessitate the use of E7018 electrodes. These low-hydrogen electrodes produce strong and ductile welds, essential for constructions subjected to dynamic forces or impacts. Due to their performance on a variety of metals and compliance with stringent industry standards, E7018 electrodes are a staple in constructing bridges, buildings, and heavy equipment.
Stainless steel welding often calls for electrodes like E308L, which provide increased resistance to corrosion and oxidation. Suited for food processing equipment, medical devices, and other applications where metal integrity and sterility are paramount, these electrodes ensure a clean, long-lasting weld. Their ability to maintain structural properties at high temperatures makes them indispensable in high-demand environments.
In specialized applications requiring heat and electrical conductivity, such as in the electric and electronic industries, copper-coated electrodes like ER70S-6 are preferred. Designed for high-speed welding, these electrodes support precision work on thin metallic sheets, making them effective in the production of cabinets and metal furniture where neatness and efficiency are critical.
The choice of welding electrode not only impacts the quality of the weld but also affects efficiency, cost, and safety of the process. Therefore, understanding the strengths and recommended applications of each electrode type allows for informed decisions that contribute significantly to project success. Utilizing expert opinions and industry case studies can offer further insights into optimizing electrode use, enhancing both expertise and overall productivity.