Selecting the perfect TIG welding rod for 304 stainless steel is crucial for achieving strong, precise welds. This decision involves considering various factors including materials, technique, and environment to ensure optimal results.
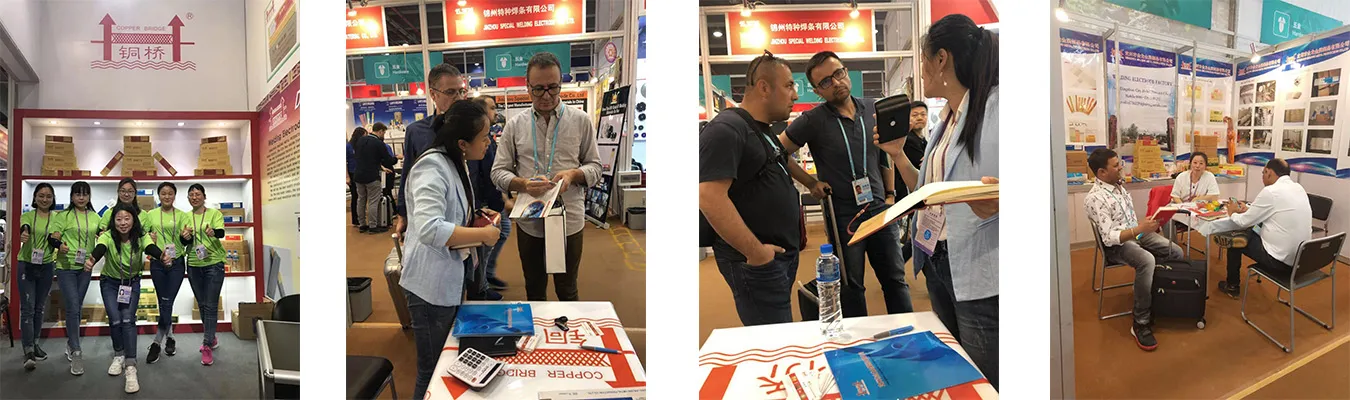
First, let’s delve into the material itself 304 stainless steel. This alloy is revered for its corrosion resistance, strength, and formability, making it a popular choice across industries such as food processing, architecture, and automotive manufacturing. Its chemical composition includes chromium and nickel, which enhance its durability and resistance to oxidation. Understanding these properties is imperative for choosing a compatible welding rod.
Enter the ER308L TIG welding rod,
the ideal candidate for welding 304 stainless steel. This rod, composed primarily of similar alloying elements, ensures excellent weld integrity with minimal risk of cracking or corrosion. The L in ER308L denotes a low carbon content, reducing carbide precipitation during welding, which is critical for preserving the corrosion-resistant properties of the stainless steel.
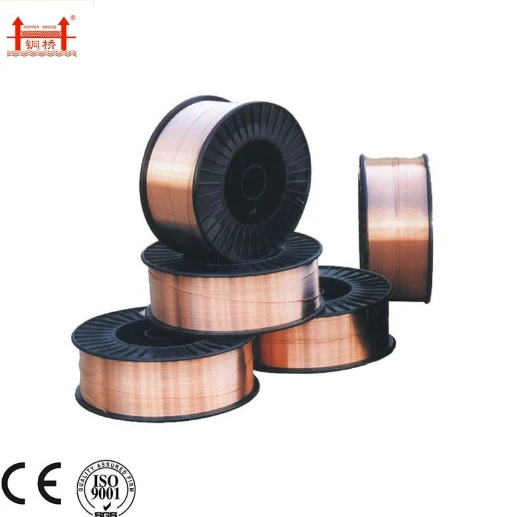
When choosing a TIG welding rod, one must consider the expertise required for executing high-quality welds. Precision and control are paramount in TIG welding, making it essential to have a skilled operator. This method allows for precise heat and filler material control, crucial for handling the thin edges and varying thicknesses commonly found in stainless steel applications. Thus, proficiency in maintaining a stable arc and managing the heat-affected zone is vital.
Furthermore, selecting the right tungsten electrode is key for effective TIG welding. The electrode should ideally be a 2% thoriated tungsten, known for its excellent arc-starting capabilities and resistance to contamination. This choice complements the characteristics of the ER308L rod and the stainless steel being welded, facilitating a cleaner, more durable weld.
tig welding rod for 304 stainless steel
Environmental factors also play an influential role. TIG welding of stainless steel should ideally occur in a controlled environment to prevent contamination and oxidation. Shielding gas, usually argon or an argon-helium mix, is utilized to maintain a pure atmosphere at the weld site, thereby preventing impurities. In environments where exposure is inevitable, back purging with gas can protect the underside of the weld.
Trustworthiness and authority in choosing TIG welding rods stem from understanding industry standards and certifications. For instance, ensuring that the ER308L rods are certified to meet standards such as AWS A5.9 is crucial. This certification guarantees that the rods are manufactured according to precise specifications, ensuring consistent performance across welding applications.
In acquiring TIG welding rods, rely on reputable suppliers who provide traceability and quality assurance. This ensures that the materials, regardless of batch, maintain consistent quality, which is pivotal for professional and industrial applications. A supplier's commitment to industry standards and continuous quality checks reinforces trust and reliability.
In conclusion, selecting the right TIG welding rod for 304 stainless steel involves expertly matching the base material properties with the appropriate filler rod, understanding the technical skill required, and acknowledging environmental factors to ensure the integrity of the weld. By adhering to stringent industry standards and relying on certified materials, welders can produce strong, durable joints, upholding the material’s integrity while meeting the highest quality expectations in industrial and consumer applications.