TIG welding cast iron with 309 stainless steel filler presents a unique set of challenges and opportunities for welders and industries relying on cast iron components. The critical insight when using 309 filler is understanding the metallurgical and mechanical dynamics involved in joining these materials to ensure strong, durable welds that can extend the life of the components.
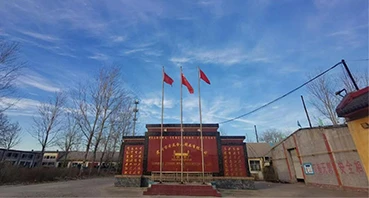
One of the foremost considerations is the nature of cast iron itself, which comes in many forms such as grey, ductile, and white iron, each with varying carbon content and properties. Cast iron is notorious for its propensity to crack due to its high carbon content, which leads to brittleness. When welding, the heat introduces thermal stresses that can result in stress fractures and a weak weld if not managed correctly.
Using 309 stainless steel as a filler material offers considerable benefits. 309 filler is an austenitic stainless steel, known for its ability to accommodate expansion and contraction during the cooling process, thanks to its high chromium and nickel content. This makes it an ideal choice for welding cast iron as it reduces the risk of cracking by offering better thermal expansion properties than many other fillers.
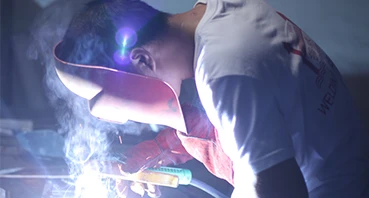
Experience has shown that preheating cast iron before welding is a crucial step. The temperature should be elevated gradually, typically to a range of 500°F to 1200°F (260°C to 650°C), depending on the thickness and type of cast iron. This reduces temperature differentials during welding and allows the material to cool more evenly, minimizing thermal shock.
During the welding process, the expertise lies in maintaining a low heat input. TIG welding provides precise control over the heat, allowing welders to use a slow, steady technique to deposit the 309 filler material. This control helps avoid overheating, which could lead to excessive stress and potentially compromise the integrity of the final weld.
In terms of authoritativeness and trustworthiness, industry professionals recommend utilizing best practices and understanding the specific requirements of the cast iron alloy being welded. Consulting manufacturer specifications and adhering to safety standards such as those outlined by the American Welding Society (AWS) ensures adherence to the highest safety and quality standards.
tig welding cast iron with 309
After welding, post-weld heat treatment (PWHT) is advisable to relieve residual stresses. This involves reheating the welded component and then allowing it to cool slowly. The exact parameters depend on the composition of the cast iron and the size of the welded section but typically involve heating to around 1100°F (593°C) and cooling in a controlled environment.
Past successful projects, documented by industry veterans and welding professionals, highlight the importance of a methodical approach when using 309 for TIG welding cast iron. Case studies often reveal that skipping steps like preheating or post-weld heat treatment frequently results in suboptimal welds that fail under stress.
Moreover, using appropriate personal protective equipment (PPE) and following strict handling guidelines for both the filler material and the base metals is crucial in maintaining safety, further adding to the trustworthiness of the procedure.
Many welding shops and industries are progressively adopting innovative welding technologies and pursuing continuous improvement in techniques to ensure precision and quality, further emphasizing the importance of expertise and experience in achieving successful results.
In conclusion, TIG welding cast iron with 309 filler is a viable and effective method that, when executed with precision and care, offers a strong weld with minimized risk of cracking. This blend of theoretical knowledge, practical experience, and commitment to safety and quality standards can lead to optimal welding performance, longer component life, and greater satisfaction for clients relying on top-tier welding solutions.