TIG welding, or Tungsten Inert Gas welding, is a process renowned for producing high-quality welds on a variety of metals, particularly carbon pipe. While this welding method requires skill and precision, it offers distinct advantages that set it apart from other welding techniques. Here, we delve into a comprehensive understanding of TIG welding carbon pipes, presenting insights based on experience and expertise, which exemplify the process's authority and trustworthiness.
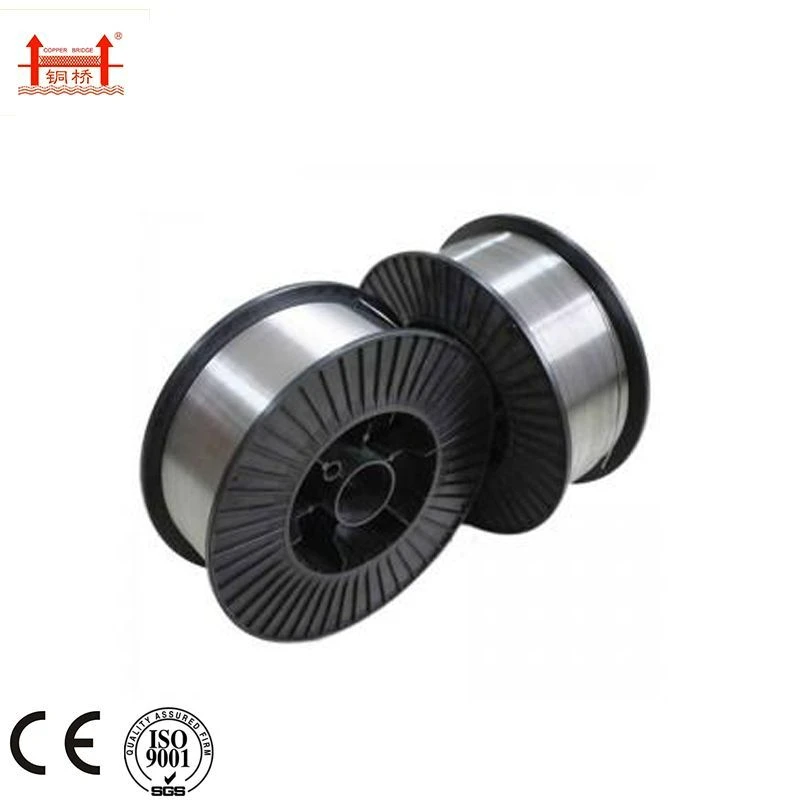
When addressing TIG welding, the most notable advantage lies in its ability to produce precise and clean welds. Carbon steel pipes, widely used in industries such as oil and gas, power generation, and chemical manufacturing, demand exacting standards in welding to ensure structural integrity and operational efficiency. TIG welding excels in this regard due to its precise control over heat input and its ability to weld with or without filler material. This control minimizes warping and provides welds that meet stringent inspection standards.
One critical expertise aspect in TIG welding carbon pipes is the preparation and cleanliness of the material. Unlike other welding methods, TIG welding is particularly sensitive to contaminants. Carbon pipes must be meticulously cleaned to remove oil, dirt, and rust—any of which could lead to defects. This meticulous preparation highlights the importance of experience in the field; skilled welders understand that even slight impurities can affect the quality of the weld.
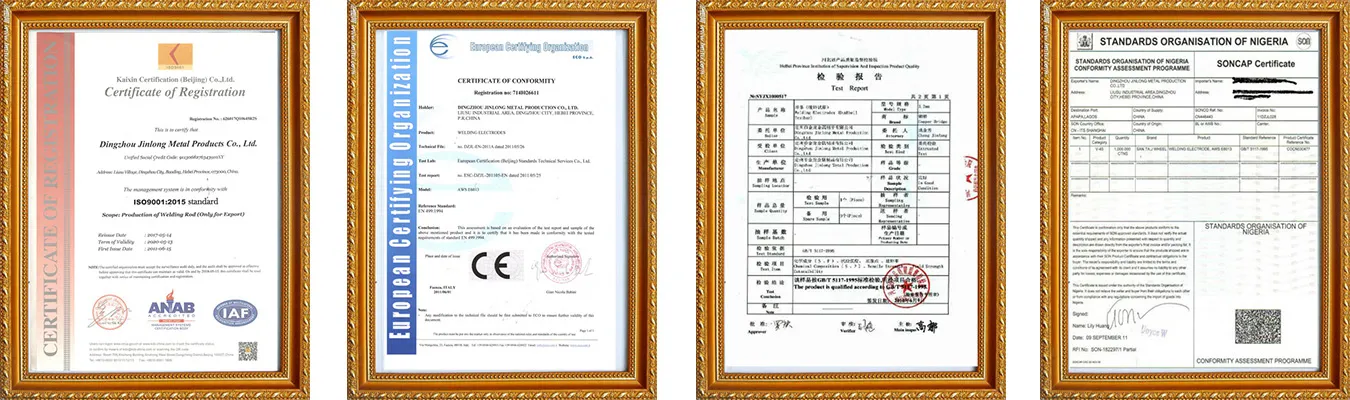
The process itself employs a non-consumable tungsten electrode to generate an arc and an inert shielding gas like argon to protect the weld pool from atmospheric contamination. The ability to control the welding parameters—such as current, voltage, and travel speed—affords welders the precision needed to handle complex projects. Mastery of these parameters is essential for achieving the desired weld quality, thus reinforcing the expert nature of TIG welding.
tig welding carbon pipe
As for the authority in TIG welding, certifications and accreditations play a pivotal role. Welders and projects that require carbon pipe welding must adhere to standards set by organizations like the American Welding Society (AWS) or the American Society of Mechanical Engineers (ASME). These standards ensure that welders are qualified and that the welding procedure specifications (WPS) align with industry requirements. Certified welders are often sought after, reflecting the credible standard expected within this domain.
The trustworthiness of TIG welding carbon pipes cannot be overstated. Its reliability in producing high-integrity weld joints is exceptional, making it a trusted method in industries where failure is not an option. Its capacity to produce welds that can withstand corrosion and pressure is invaluable for pipelines and structural applications. Moreover, consistent quality assurance through non-destructive testing (NDT) methods, such as radiographic and ultrasonic testing, further cements its reputation. These testing methods ascertain the weld’s soundness without damaging the pipe, ensuring that TIG welds meet operational demands.
Additionally, the innovation in TIG welding equipment has enhanced welders' capabilities. Modern TIG welders are equipped with advanced features like pulsing, which aids in controlling heat input and increasing penetration while maintaining a stable arc. These technological advancements support welders in managing challenging projects, confirming the method’s continual evolution and its adherence to modern standards of excellence.
In sum, TIG welding of carbon pipes stands out for its precision, cleanliness, adherence to industry standards, and innovative technology. The seamless blend of experience and expertise required to excel in this field underscores its authoritative and trustworthy nature. Professionals dedicated to mastering TIG welding contribute to the safety, durability, and efficiency of critical industrial applications, showcasing the indispensable role this method plays in today's manufacturing landscape.