TIG welding with carbon steel presents unique opportunities and challenges that seasoned welders understand deeply. It's a process that demands precision and an understanding of the material properties, often reflecting the welder's skill and expertise.
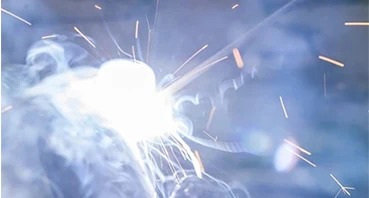
One of the critical elements of TIG, or Tungsten Inert Gas, welding with carbon steel is the material's inherent reactivity. Carbon steel, known for its strength and affordability, reacts readily with oxygen and can corrode quickly when not properly maintained. Thus, when undertaking TIG welding for such materials, the quality of the finished product largely depends on controlling the welding environment and protecting the steel from air exposure throughout the process.
Professionals in the field stress the importance of preparation. Before initiating the welding process on carbon steel, the surface must be meticulously cleaned. This involves removing any rust, oil, or paint that might interfere with the weld quality. Skipping this crucial step can lead to weak welds or contamination, which severely compromises the integrity of the joint. A clean surface ensures that the weld is strong and durable, which is essential for maintaining structural integrity in the final product.
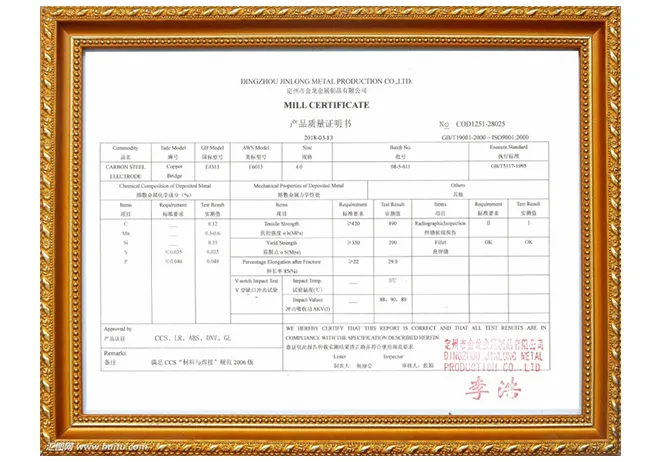
The choice of filler material also plays a critical role. Expert welders often opt for a filler metal that matches the base metal in properties. This decision enhances the overall mechanical properties of the weld joint. In many cases, ER70S-6 is a popular choice for welding carbon steel because of its ability to handle surface contaminants, thus optimizing the welding process.
tig carbon steel
Another significant factor is the control of the heat input. Carbon steel is sensitive to overheating, which can lead to warping or burn-through. Therefore, managing the amperage setting and travel speed meticulously is crucial. Experienced welders understand that maintaining a steady hand and consistent speed helps avoid overheating. The TIG process allows for precise control of heat, making it preferable for projects requiring high-quality welds without deforming the base material.
The shielding gas used in TIG welding also impacts the quality of the weld. Argon is typically the gas of choice due to its stable arc and excellent cleaning action.
For carbon steel, a pure argon shield is generally sufficient. However, when welding thicker sections, adding a small percentage of CO2 or helium can improve penetration and arc stability. These adjustments require a thorough understanding of the material and process, highlighting the importance of expert knowledge in achieving optimal results.
Post-welding treatment is an area that cannot be overlooked. Seasoned welders ensure their projects undergo appropriate cooling and finishing to enhance durability and appearance. Rapid cooling can lead to brittleness in carbon steel, so controlled cooling is recommended to maintain desirable properties. This attention to detail reflects not only the expertise of the welder but also their commitment to quality and reliability.
Ultimately, TIG welding carbon steel is a skill that marries artistry with science. Precision, technique, and an understanding of metallurgical principles come together to produce results that stand up to scrutiny. It is not merely about joining metal but creating a durable, aesthetically pleasing piece. Those experienced in this field know the satisfaction of a job well done, with every weld serving as a testament to their expertise and commitment to excellence. Through careful preparation, skillful execution, and detailed aftercare, TIG welding of carbon steel remains a respected and valuable craft within the industry.