Stick welding, often known as Shielded Metal Arc Welding (SMAW), is a fundamental skill for many welders who appreciate its simplicity and effectiveness in various environments. When discussing stick welding, particularly with 7018 rods, we dive into a segment of welding that is renowned for its reliable performance and usability across a diverse range of applications.
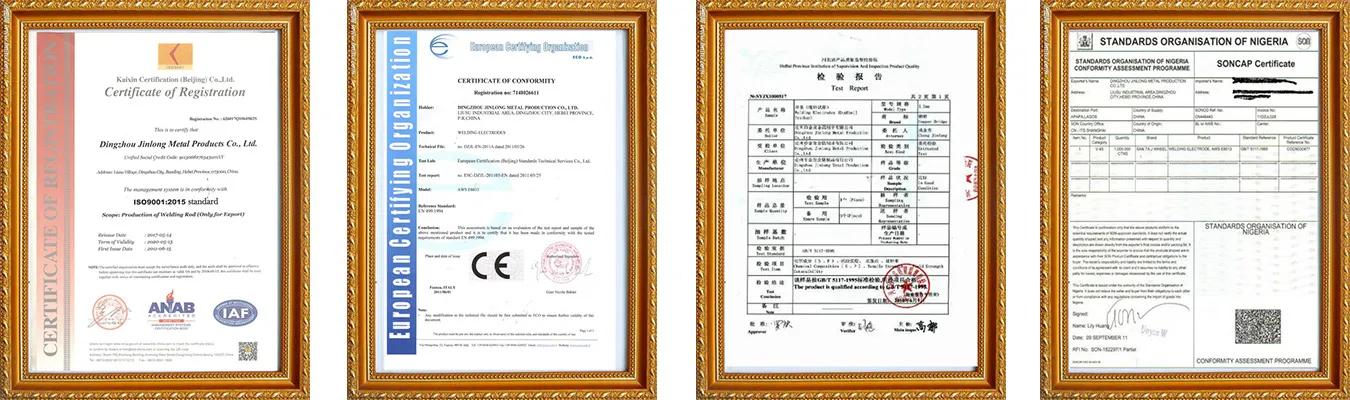
7018 welding rods are low-hydrogen electrodes, often coveted for their impressive tensile strength, which is vital for projects requiring high durability and structural integrity. This rod is composed primarily of iron powder and iron oxide, contributing to its smooth and strong welds. The 7018 designation itself speaks volumes, highlighting its tensile strength (approximately 70,000 psi) and the position of usability, which includes flat, horizontal, vertical, and overhead positions, making it incredibly versatile.
For those experienced in stick welding,
using 7018 rods offers a tactile advantage. The rod is known for its ease of control, reducing spatter and promoting a stable arc. This characteristic is crucial for projects demanding clean welds and minimal post-weld clean-up. The slag produced by 7018 rods is light and easily removable, allowing welders to save time and effort during the finishing process.
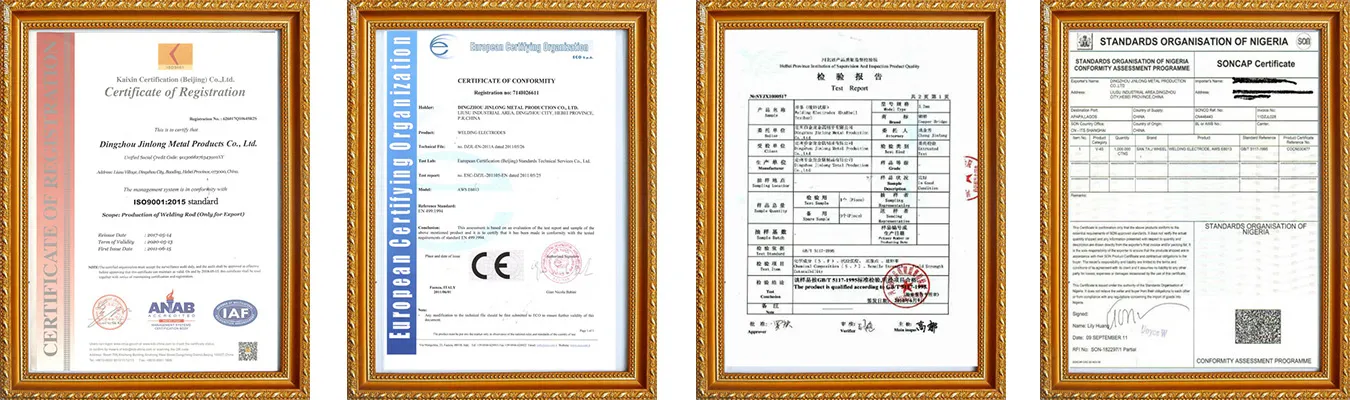
A key factor that adds to the expertise required in using 7018 rods is the need for precision in control and technique. The rod’s arc is relatively steady, which requires welders to maintain a consistent angle and pressure to ensure uniformity and penetration of the weld. This helps in fostering a neat bead appearance and prevents defects such as undercutting or porosity, which can compromise the strength of the weld.
One of the authoritative aspects of using 7018 rods is their compatibility with various metals. Whether working on carbon steel, low-alloy steel, or even high-strength steel, 7018 rods enhance the mechanical properties of the welded joint, making them a top choice in industries such as construction and shipbuilding. Their flexibility and universal application in welding procedures provide reliability that professionals trust for critical applications.
stick welding with 7018 rods
In environments prone to harsh weather conditions, 7018 rods have proven their trustworthiness. They can be applied in moist conditions thanks to their low-hydrogen composition, which minimizes the risk of hydrogen-related defects like cracking. However, it’s essential to store these rods correctly, preferably in a rod oven, to avoid moisture absorption that can compromise the weld quality.
Building on authentic experience, seasoned welders often advise that maintaining the right welding speed and rod angle, typically around 5 to 15 degrees off vertical, significantly impacts the quality of the weld. These techniques, garnered through practical application, also stress the importance of keeping the rod in close but not direct contact with the workpiece to stabilize the arc without sticking.
In enhancing your welding expertise with 7018 rods, continuous practice remains pivotal. Novices and experienced welders alike should occasionally revisit the foundational techniques while working with these rods, reinforcing the balance between speed and control. This reiteration not only polishes skill but also instills confidence in executing high-quality welds.
7018 welding rods offer an excellent pathway to achieving welds that meet both aesthetic and structural standards. Through diligent practice and an adherence to proper storage and handling techniques, welders can fully leverage the benefits of these reliable rods. Ultimately, the authority and trustworthiness of 7018 rods in stick welding lie in their consistent performance and the robust, durable welds they produce, fulfilling the most demanding industrial requirements.