Stick welding, known technically as Shielded Metal Arc Welding (SMAW), is one of the most versatile and widely used methods for welding a variety of metals. Among these metals, 316 stainless steel is a common material in industries such as food processing, chemical manufacturing, and marine applications due to its exceptional resistance to corrosion and pitting. However, welding 316 stainless steel requires a distinct blend of technique, precision, and understanding of the material properties. Here, we delve into the practical insights and authoritative advice to achieve optimal results in stick welding 316 stainless steel.
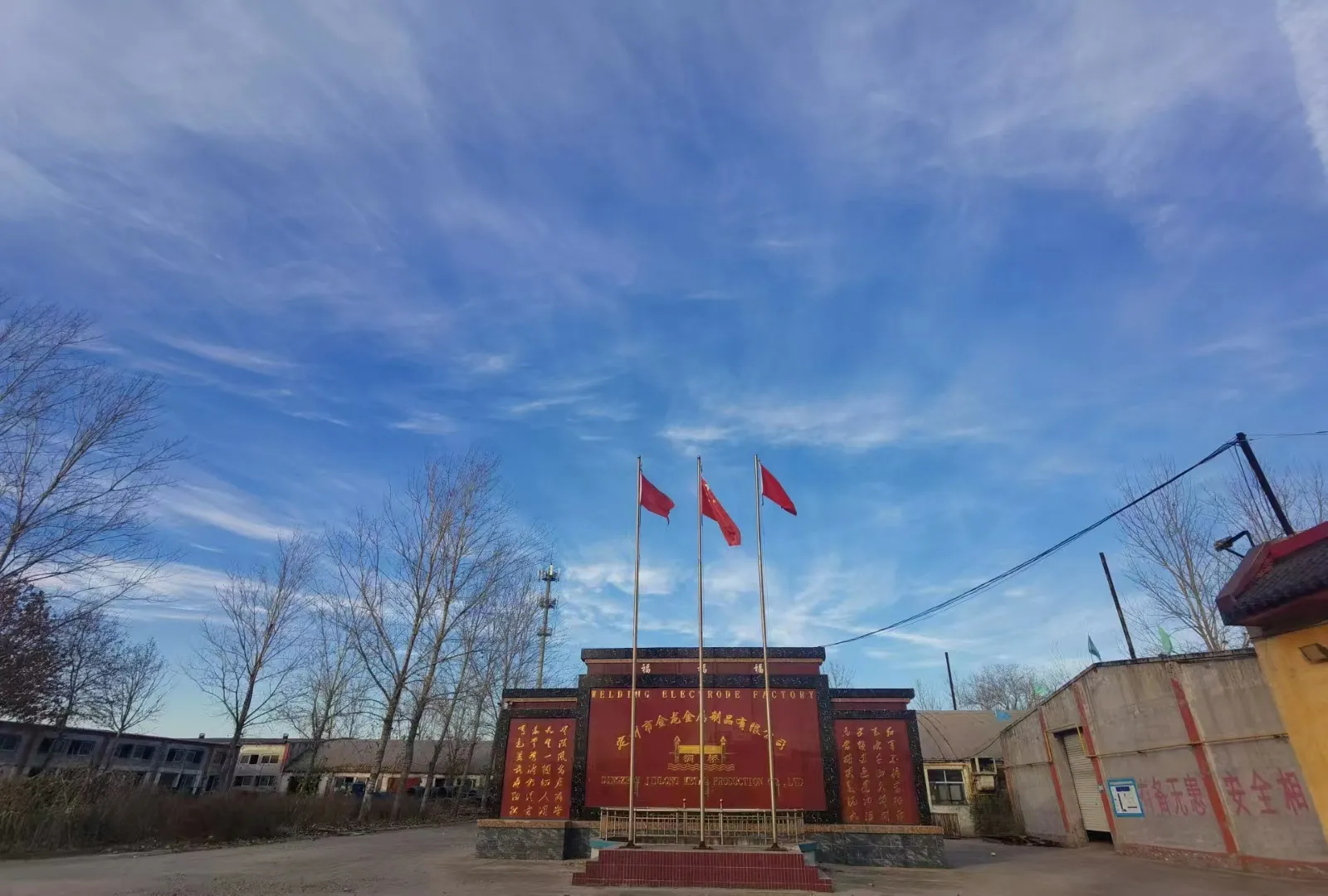
Achieving success in stick welding 316 stainless steel begins with understanding the material's unique characteristics. The presence of molybdenum in 316 stainless steel enhances its anti-corrosive properties but also requires specific considerations during welding to prevent defects such as distortion, sensitization, and hot cracking. For professionals looking to achieve a pristine weld, selecting the right electrode is crucial. An E316L electrode is often recommended due to its compatibility with the base metal and its low carbon content, which minimizes carbide precipitation and intergranular corrosion.
Preparation is an indispensable step in the welding process. Thorough cleaning of the weld area ensures the absence of contaminants, which can compromise the weld's integrity. Abrasive cleaning tools such as wire brushes made of stainless steel should be employed to avoid cross-contamination with ferrous metals. Additionally, maintaining a bevel angle between 30 to 37.5 degrees on the workpieces facilitates better penetration and fusion, especially necessary given the thicker sections often associated with industrial applications of 316 stainless steel.
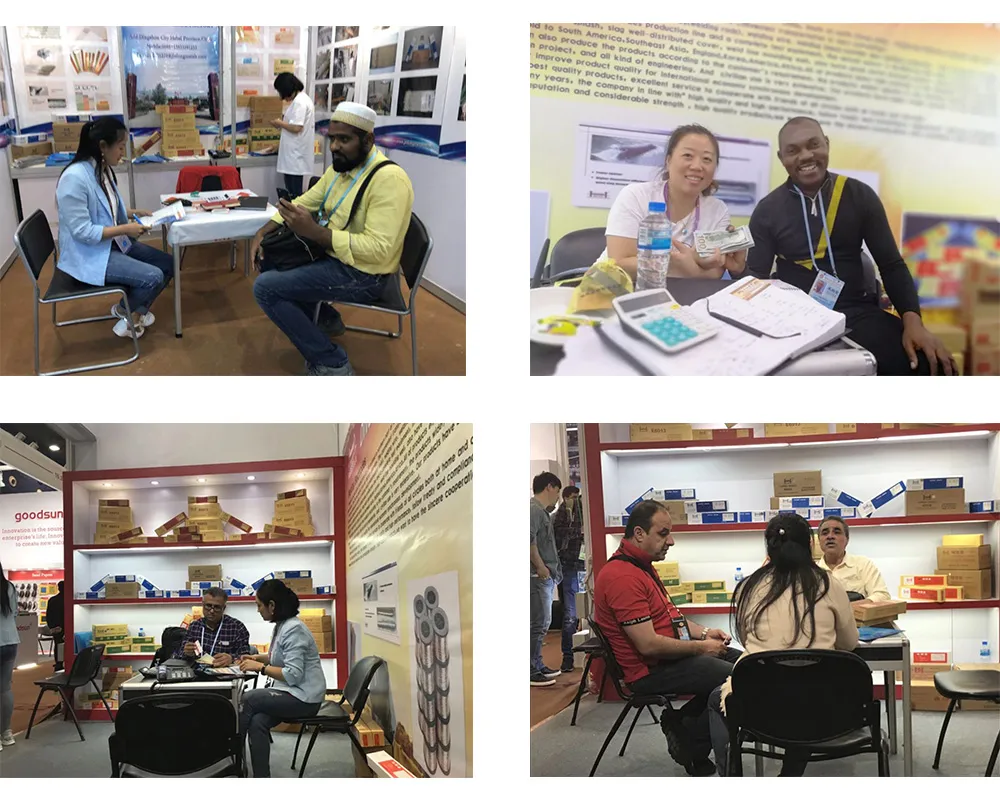
Controlling heat input is another fundamental aspect of working with this alloy. Excessive heat can lead to distortion and weaken the material's corrosion resistance. Welding experts suggest maintaining a short arc length and employing intermittent welding techniques, which allow more control over heat distribution. Utilizing a backstep welding technique also helps manage heat influence, reducing the risk of distortion and ensuring uniformity in the weld bead.
stick welding 316 stainless steel
Precision in setting the correct amperage cannot be overstressed. Welding practitioners should refer to the manufacturer's specifications for the electrode being used, typically a range between 80-120 amperes for average thickness. Fine-tuning is often required and must consider factors like electrode diameter, material thickness, and the weld position. Conducting trial runs on test pieces to calibrate the settings can save time and prevent material wastage.
Shielding gas is unnecessary for SMAW, but ensuring that the welding area is well-ventilated protects from harmful fumes. Safety should always parallel the technical aspects of welding. Welders should be equipped with the correct personal protective equipment, including helmets, gloves, and appropriate clothing, to safeguard against burns and exposure to ultraviolet radiation.
Finally,
post-weld treatments significantly impact the longevity and performance of 316 stainless steel welds. Stress-relieving and passivation treatments are widely encouraged. Stress relieving reduces residual stresses that can lead to cracking, while passivation restores the chromium oxide layer that gives stainless steel its corrosion-resistant properties.
In summary, stick welding 316 stainless steel demands meticulous preparation, precise technique, and a keen understanding of the material's properties. By adhering to the principles outlined here, welders can produce robust and reliable welds, enhancing both performance and longevity in demanding applications. This expert advice, backed by experience and industry standards, equips professionals with the knowledge necessary to master this complex yet rewarding welding process.