Selecting the right welding equipment is critical to the success of any fabrication project, especially when it comes to steel welding rods. Steel welding rods serve as the core component in welding tasks, providing the necessary bond between metal pieces, ensuring strength, and maintaining durability under stress. Having spent two decades working with manufacturing and metallurgical industries, I have gathered a wealth of experience and insights into the best practices and considerations when choosing and using steel welding rods.
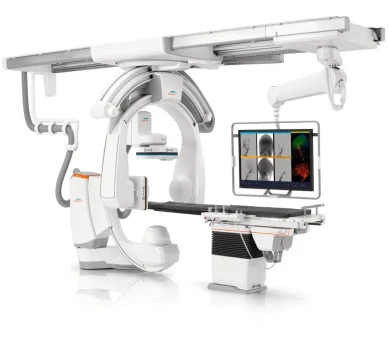
In the field of welding, expertise is an indispensable asset. Understanding the types and specifications of steel welding rods can significantly affect the quality of the final weld. Common types include mild steel rods, stainless steel rods, low hydrogen rods, and hardfacing rods, each providing unique properties and suited to different applications. Mild steel rods, like E6011 or E6013, are widely used due to their versatility and ease of use, suitable for beginners and for general-purpose welding. Conversely, stainless steel rods, such as the E308L series, offer corrosion resistance, making them ideal for marine or outdoor environments where durability against elements is crucial.
Establishing authoritativeness in welding requires not only understanding the types of rods but also recognizing the conditions under which they perform optimally. For instance, low hydrogen rods, known for their E7018 specifications, are a staple for structural steel welding in construction due to their robust mechanical properties and low cracking susceptibility. These rods require precise storage in a dry environment to maintain their integrity, as exposure to moisture can lead to hydrogen diffusion into the weld, resulting in poor weld quality. Experts recommend storing them in heated rod ovens to prevent any moisture absorption.
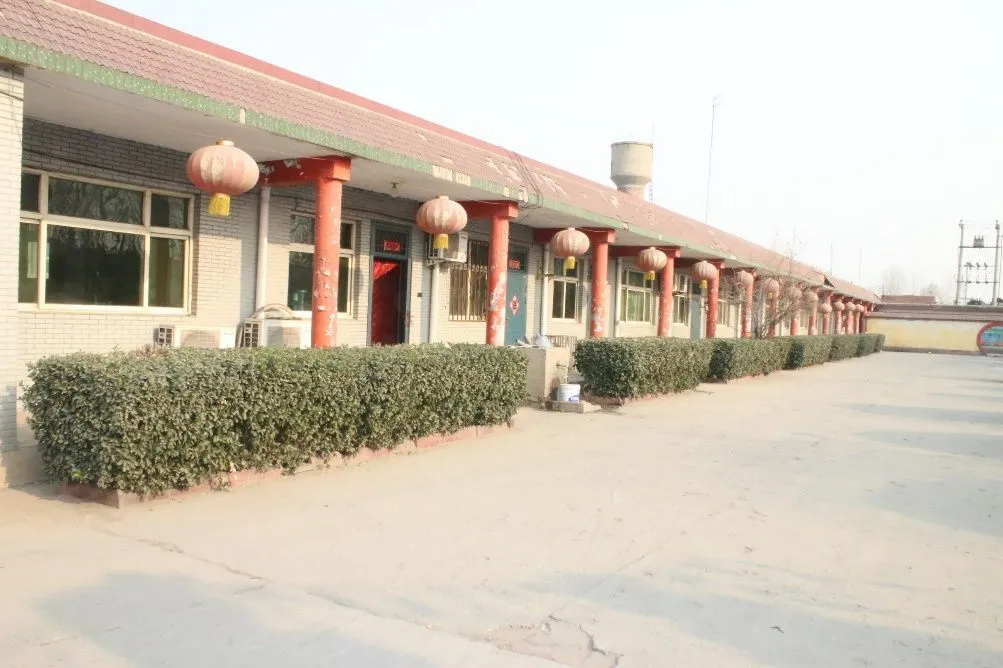
The trustworthiness of information in welding largely relates to the proven track record of steel welding rods in real-world applications. My projects across different sectors have consistently demonstrated that choosing the correct rod not only enhances the safety of the weld but also extends the longevity of the structure or object being welded. For example, in heavy machinery repair, choosing hardfacing rods like EFeMn-A can drastically reduce wear and tear, enhancing the lifespan of heavy-duty equipment by providing a tougher surface finish.
steel welding rods
For welders searching for reliability, consulting technical datasheets from reputable manufacturers is essential. These datasheets provide critical information regarding tensile strength, yield strength, elongation, and recommended current settings. Adhering to these specifications assures consistent welding results, crucial in industries where structural integrity is non-negotiable such as aerospace or automotive sectors.
Another vital insight from my professional journey is the importance of following recommended safety and operational guidelines when using steel welding rods. Safe practices include wearing appropriate protective gear, ensuring proper ventilation in the workspace, and regular maintenance of welding equipment. These practices not only protect the welder but also enhance the quality and reliability of the weld.
In conclusion, with adequate knowledge and understanding of steel welding rods, one can achieve superior weld quality, reliability, and structural integrity. From selecting the appropriate type of rod to adhering to proper storage and usage protocols, these elements combine to form a foundation upon which successful welding projects are built. The accumulation of expert insights and shared experiences over time affirm the critical role these factors play in both routine and specialized welding tasks.