Stainless welding rods have become indispensable in construction, automotive, and manufacturing sectors, driven by the growing demand for durable and corrosion-resistant materials. These rods are specifically engineered to enhance the durability and finish of welding projects, ensuring robust connections and long-lasting structures.
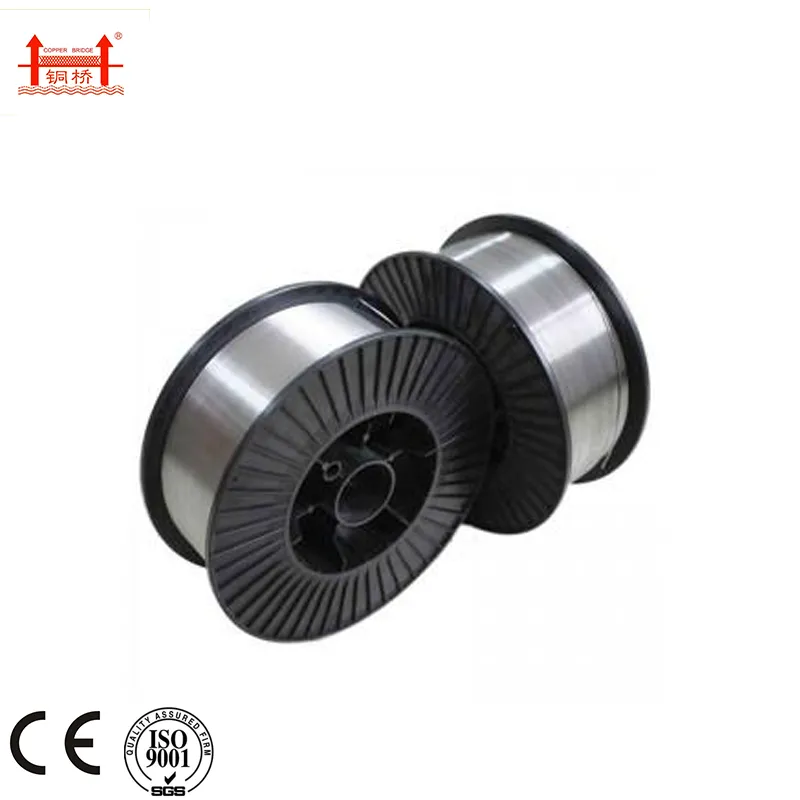
One key feature that sets stainless welding rods apart is their exceptional resistance to corrosion. Stainless steel, an alloy known for its robust resistance to rust and stains, is the primary component. This resistance makes stainless welding rods ideal for projects exposed to harsh environmental conditions, such as offshore structures, pipelines, and bridges. Their superior performance helps reduce the need for frequent maintenance and replacements, ultimately resulting in cost savings.
For professionals working with stainless welding rods, understanding the nuances of their operation is crucial. These rods require precise temperature control and technique adjustments to ensure optimal results. High-quality welds necessitate stable arc control and minimal spatter, as the presence of spatter can significantly affect the strength and appearance of the weld. Experts recommend using a consistent wire feed speed and employing a steady hand to maintain precision in weld seams.
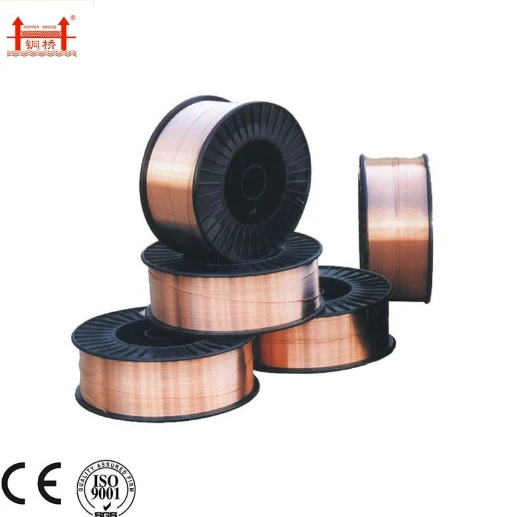
Navigating through the various types of stainless welding rods is essential to selecting the most appropriate one for a given application. Among the most common are 308 and 316 types, each tailored to specific environmental and structural demands. For instance, 308 stainless welding rods are typically used for welding similar base metals, offering excellent toughness and corrosion resistance. On the other hand, 316 rods are preferred in industries like pharmaceuticals and food processing due to their enhanced resistance to chlorides and acids.
Professionals also underscore the significance of pre-weld and post-weld treatment processes. Proper cleaning and preparation of the base materials before welding ensure a strong bond and prevent imperfections. Post-weld treatments, such as passivation, are recommended to restore the passive layer on stainless steel, enhancing its corrosion resistance. By adhering to these meticulous steps, welders can extend the life span and maintain the aesthetic appeal of their projects.
stainless welding rod
Investing in high-quality stainless welding rods is vital, as the choice of rod directly impacts the integrity of the weld. The adherence to international quality standards such as ASTM or AWS ensures that the rods are manufactured under stringent regulations, providing both welders and project managers with assurance about their performance. This adherence translates into a higher level of trust and reliability on construction sites and factory floors.
The use of stainless welding rods has a significant impact on operational efficiency. Their robust properties reduce downtime associated with repairs and maintenance. Structures completed using these rods demonstrate exceptional longevity, making them a preferred choice for large-scale infrastructure projects where safety and durability are paramount.
For organizations seeking sustainable solutions, stainless welding rods offer an environmentally friendly alternative. The longevity and durability of stainless steel reduce the need for resource-intensive replacement over time, contributing to sustainability goals. Additionally,
stainless steel is fully recyclable, minimizing waste and promoting a circular economy.
With an eye on continuous improvement, manufacturers of stainless welding rods are investing in research and development to enhance their properties further. Innovations aim to improve their usability, reduce costs, and enhance environmental benefits. For welders and engineers, staying abreast of these advancements is crucial in maintaining a competitive edge and delivering high-quality results.
In conclusion, the application of stainless welding rods in welding projects is not just a technical consideration but a strategic decision that influences the integrity and longevity of structures. Their corrosion resistance, strength, and adaptability to various environments make them the material of choice for professionals committed to quality and sustainability. By understanding the intricacies of their use, and ensuring adherence to best practices and quality standards, professionals can achieve superior outcomes that stand the test of time.