Stainless steel welding sticks, often referred to as welding rods or electrodes, serve as a vital component in the welding process, particularly in construction, manufacturing, and repair industries. These rods are designed to fuse metals while providing strength and durability to the welded joints, ensuring the structural integrity of the project. Their application spans across various sectors that require precision and reliability, from automotive fabrication to aerospace engineering. This article delves into the unique attributes, applications, and best practices concerning stainless steel welding sticks, guided by principles of Experience, Expertise, Authoritativeness, and Trustworthiness.
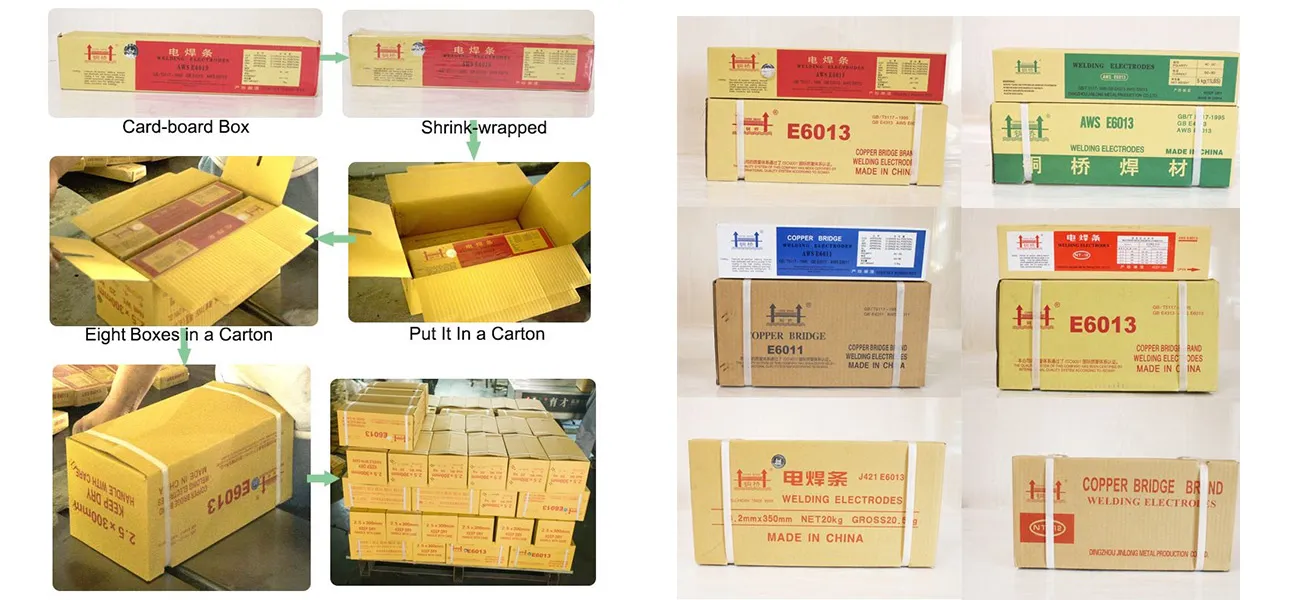
Stainless steel welding sticks are typically composed of a mixture of metals, with precise formulations that cater to different grades of stainless steel. The distinct advantage of using these sticks lies in their resistance to rust and corrosion, a signature trait of stainless steel. This resistance is crucial for applications exposed to harsh environmental conditions, thus amplifying the longevity of the metal structures they form. Experienced welders value stainless steel welding sticks for their ability to perform under high temperatures and their compatibility with a range of welding positions, from flat to overhead.
Expertise in using stainless steel welding rods ensures optimal results. A welder must be familiar with the specific characteristics of the particular stainless steel grade in use, as well as the corresponding welding rod. For instance, using a 308L stainless steel rod is recommended for welding 304-grade stainless steel, providing a strong, corrosion-resilient weld. The intricacies involved in selecting the appropriate rod—considering variables such as metal thickness, welding position, and intended use—form a critical part of a welder’s expertise.
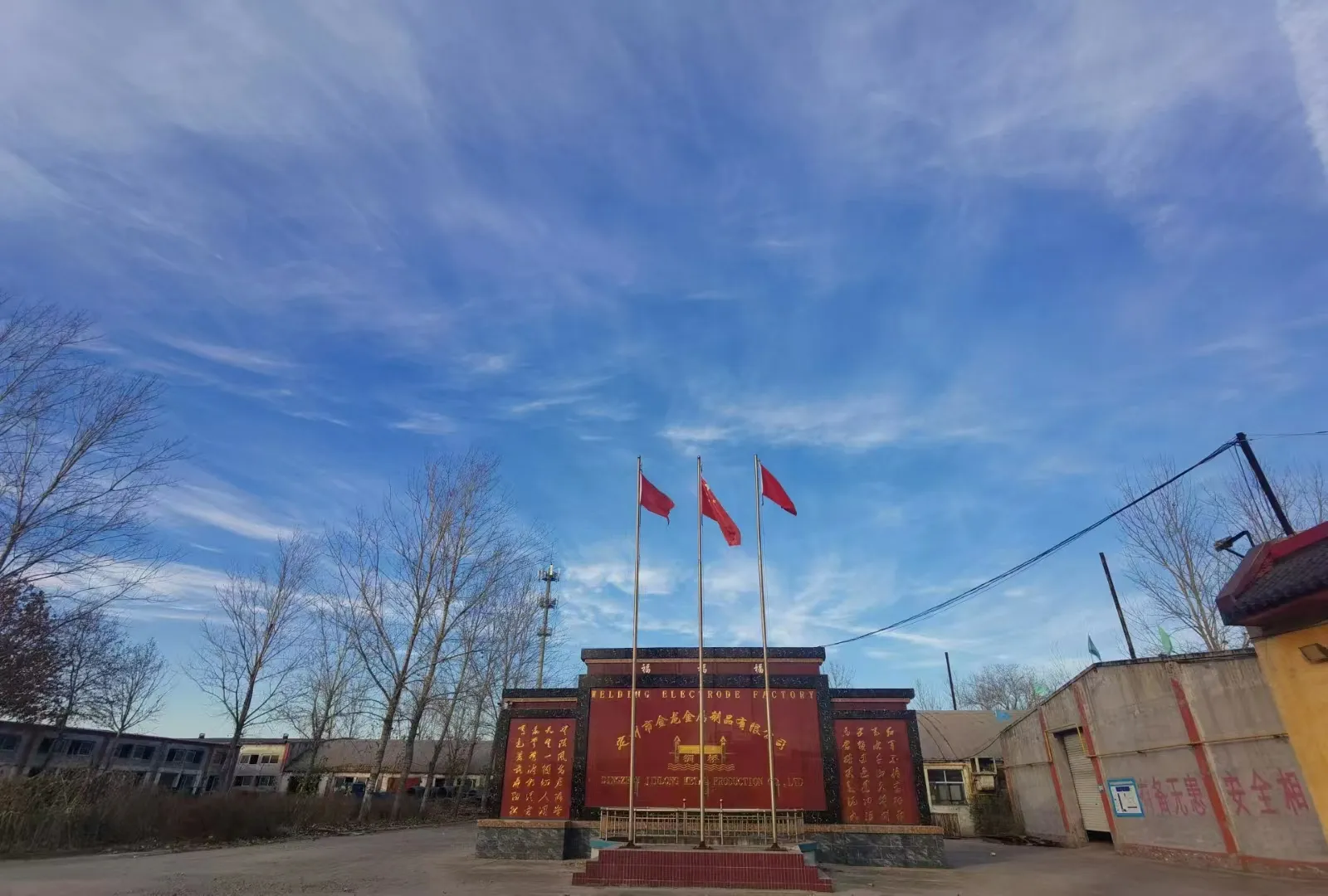
Authoritativeness in the use of stainless steel welding sticks can be accentuated through adherence to industry standards and safety regulations. Organizations such as the American Welding Society (AWS) and International Organization for Standardization (ISO) outline specific guidelines that ensure the safety, compatibility, and performance of these rods. Certified products that conform to these standards are preferred in professional environments, making them an authoritative choice for companies aiming to uphold safety and quality in their operations.
Trustworthiness is verified through the implementation of rigorous testing and quality control measures. Reputable manufacturers subject their stainless steel welding rods to a series of tests that simulate real-world conditions, assessing factors such as tensile strength, ductility, and impact resistance. These tests confirm the reliability of the welding rods in providing durable welds that withstand environmental stresses and wear over time.
stainless steel welding stick
In practice, a successful stainless steel welding process requires careful preparation and attention to detail. Cleaning the base metal thoroughly to remove contaminants such as oil, dust, and grease is crucial. Maintaining an appropriate arc length and angle during welding can prevent common defects such as porosity and cracking. Post-weld treatment like passivation or annealing may be necessary to enhance the corrosion resistance of the welds. Professional welders often rely on state-of-the-art welding machines with precise controls to fine-tune these elements, achieving a seamless and robust weld.
Stainless steel welding sticks also play a significant role in sustainability through their contribution to the prolonged life cycle of products, preventing premature replacement and reducing material waste. The recyclability of stainless steel further underscores its environmental benefits, aligning with global efforts to mitigate environmental impact through sustainable practices.
The demand for stainless steel welding rods is influenced by a variety of factors, including technological advancements in welding techniques and the growth of industries such as renewable energy and infrastructure. Understanding market trends and innovating with new alloy compositions and coating technologies can enhance the performance and versatility of these welding rods, meeting the evolving needs of modern industry.
In conclusion, stainless steel welding sticks are indispensable tools in welding applications that demand high performance and durability. Through expert knowledge, adherence to authoritative standards, and dedication to quality, these welding rods encapsulate the principles of Experience, Expertise, Authoritativeness, and Trustworthiness. For professionals seeking reliable welding solutions, stainless steel welding sticks are a testament to innovation and resilience in the face of diverse challenges, ensuring safety, quality, and sustainability in every weld.