Choosing the right welding rod is essential for ensuring the integrity and durability of welding projects, especially when it comes to stainless steel applications. The stainless steel welding rod 304 is one of the most versatile and widely used options available, known for its robust performance and compatibility with a range of stainless steel grades.
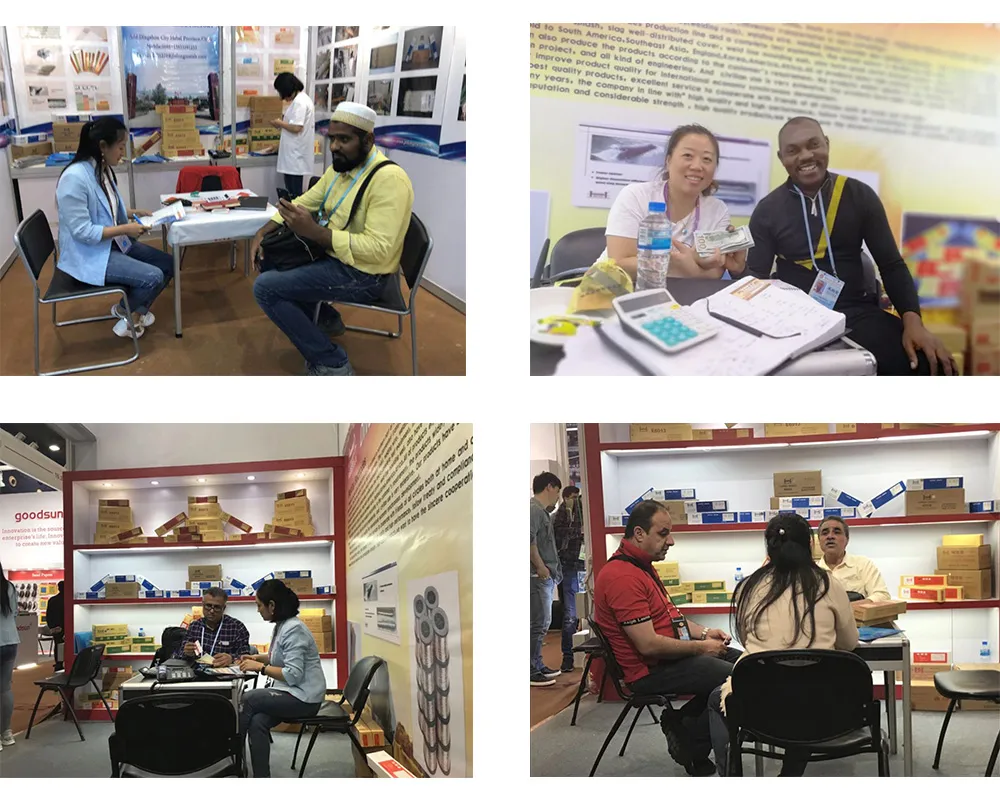
Firstly,
it's crucial to understand the composition and benefits of using the 304 stainless steel welding rod. This rod is primarily made of an alloy comprising 18-20% chromium and 8-10.5% nickel, which accounts for its excellent corrosion resistance and superior strength-to-weight ratio. The presence of nickel not only enhances its resistance to oxidation but also allows the material to withstand higher temperatures compared to other stainless steel types. These characteristics make the 304 welding rod particularly suitable for applications in environments that are prone to corrosion, such as marine and chemical processing industries.
From a professional welder’s perspective, the stainless steel welding rod 304 is appreciated for its ease of use. During welding, this rod provides a stable arc with minimal spatter, which enhances the overall quality of the weld and reduces the need for extensive post-weld clean-up. This is particularly beneficial in high-volume production settings where time efficiency is crucial. Furthermore, the 304 rod’s adaptability in both acidic and neutral environments allows welders to execute projects with consistent outcomes, regardless of the surrounding conditions.
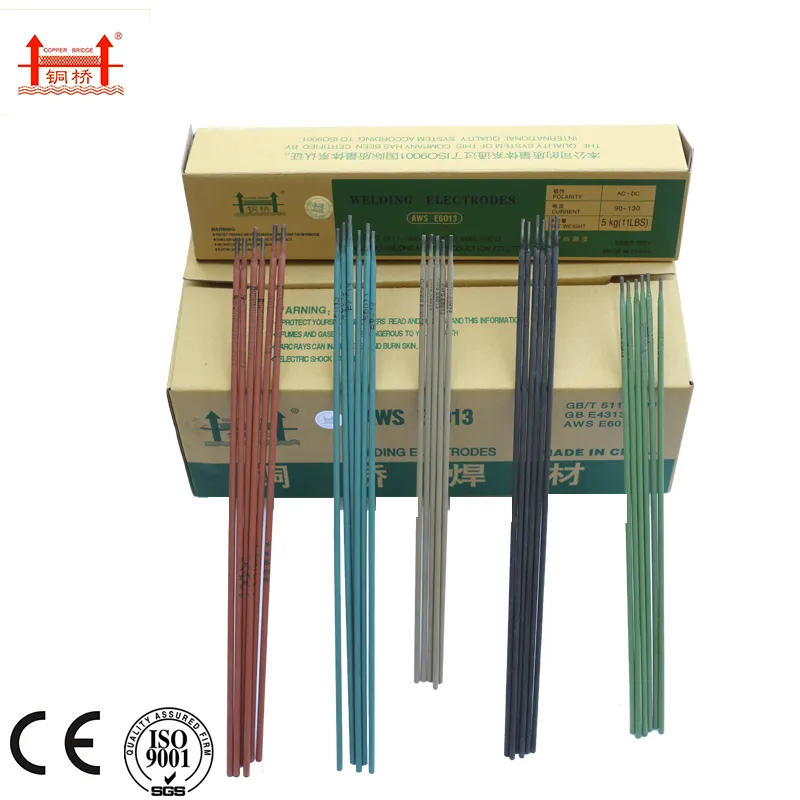
When discussing the welding techniques suitable for stainless steel welding rod 304, TIG (Tungsten Inert Gas) and MIG (Metal Inert Gas) welding are frequently recommended. TIG welding, in particular, is favored for its precision and ability to produce clean, high-quality welds. This technique is ideal when welding thinner materials as it offers greater control over heat input, thus minimizing the risk of warping or distorting the workpiece. In contrast, MIG welding is more suitable for thicker workpieces where speed and efficiency are priorities. MIG welding with a 304 rod can produce durable welds capable of handling significant stress and load without compromising structural integrity.
stainless steel welding rod 304
The application of a 304 welding rod is not solely limited to industrial purposes. It is also an excellent choice for artistic and architectural projects. With the increasing demand for aesthetic and durable construction materials, the 304 stainless steel rod finds its place in creating everything from large-scale sculptures to intricate design elements that require both an appealing look and resilience to environmental factors.
For those delving into DIY projects, the 304 stainless steel welding rod offers a user-friendly experience without requiring professional-grade expertise to achieve satisfactory results. Its forgiving nature, in terms of arc stability and puddle control, makes it a practical choice for hobbyists and aspiring welders who are keen on experimenting with stainless steel without the steep learning curve associated with other, more challenging materials.
Quality is a non-negotiable element when selecting a stainless steel welding rod, and the 304 grade stands out due to its consistent performance and reliability. It meets stringent industry standards, ensuring that each rod delivers the expected results, backed by proven metallurgical properties. This aspect reinforces the importance of choosing a reputable supplier that guarantees the authenticity and quality of the 304 rods, providing peace of mind and trust in every project undertaken.
In conclusion, the stainless steel welding rod 304 represents a balance of strength, versatility, and ease of use, making it a dependable choice across various applications. Whether in a professional context or for personal endeavors, its properties cater to a wide spectrum of needs, ensuring that regardless of the project's scale or scope, the outcomes are reliable, durable, and of a high standard. Embracing this welding rod not only contributes to the success of diverse projects but also establishes a foundational understanding of quality materials in the field of welding.