Stainless steel welding electrodes play a crucial role in today’s manufacturing and construction industries. These essential components ensure high-quality, durable welds that are capable of withstanding the rigors of various environmental factors. Understanding the intricacies of stainless steel welding electrodes is paramount for professionals seeking to achieve optimal results.
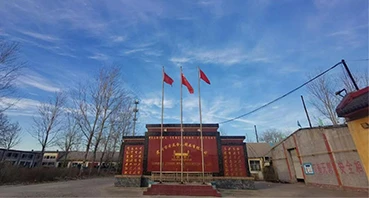
In the manufacturing world, stainless steel is highly valued for its exceptional resistance to corrosion, making it ideal for demanding applications in sectors such as food processing, chemical shipping, and architectural structures. The welding electrodes used for this metal must meet stringent quality and performance standards to maintain stainless steel's integrity.
When selecting stainless steel welding electrodes, the first consideration is the electrode's compatibility with the specific type of stainless steel being welded. Stainless steels are categorized into various grades, such as austenitic, ferritic, martensitic, and duplex, each with unique chemical compositions and mechanical properties. For instance, austenitic stainless steels, like the popular 304 and 316 grades, require electrodes that accommodate their high chromium and nickel content to prevent intergranular corrosion and to maintain their non-magnetic nature.
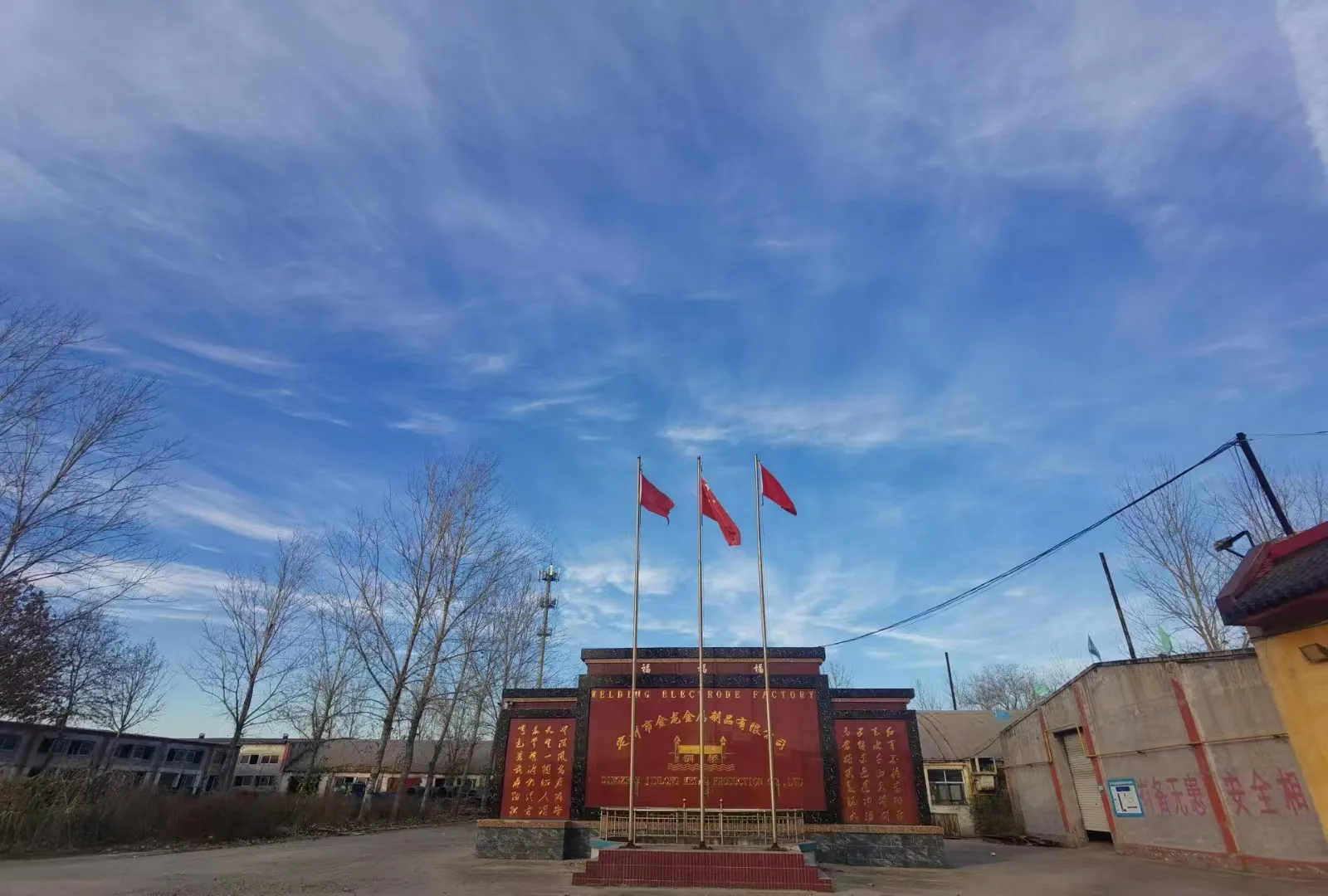
For professionals, expertise in the nuances of electrode coating cannot be overstated. Coatings significantly impact arc stability, slag formation, and penetration depth, all of which affect the welding process's outcome. For stainless steel, rutile and basic coatings are often preferred because they offer a smoother arc, easier slag removal, and superior mechanical properties in the weld metal. Experts recommend basic-coated electrodes for critical applications where reliability and mechanical toughness are non-negotiable.
Authoritative knowledge about the welding environment is crucial. Welders must be aware that the ambient conditions, such as temperature and moisture, can severely affect the quality of the weld. Stainless steel's expansion coefficient necessitates precise control over pre-heating and cooling rates to minimize the risk of thermal-induced stresses and distortion. To ensure trustworthiness in weld integrity, welders should routinely test and evaluate the welds against industry standards such as those outlined by the American Welding Society (AWS).
stainless steel welding electrodes
Real-world experience highlights the importance of electrode storage and handling. Stainless steel welding electrodes are susceptible to moisture uptake, which can lead to hydrogen-induced cracking. Only by maintaining electrodes in a dry and temperate storage environment can one prevent moisture absorption, ensuring the electrodes' readiness and performance remain uncompromised. For best results, professionals often utilize portable rod ovens on-site to keep electrodes dry during projects.
Furthermore, the safety and health implications associated with stainless steel welding cannot be ignored. Welding stainless steel releases fumes that may contain hexavalent chromium, a known carcinogen. Experts emphasize the implementation of adequate ventilation systems and personal protective equipment (PPE) to safeguard welders against occupational hazards.
Trust, built over years of consistent delivery of high-quality work, is at the core of a welder’s reputation. Keeping abreast of technological advances and evolving industry standards ensures that professionals not only adhere to established norms but also lead in implementing innovative welding practices. Electrode manufacturers constantly improve formulations for enhanced performance, and staying informed about these developments is crucial for maintaining a competitive edge.
In conclusion, the mastery of stainless steel welding electrodes encompasses a blend of in-depth product knowledge, hands-on experience, and a commitment to safety and excellence. This expertise supports welders and engineers in achieving welds that are not only structurally sound but also meet the aesthetic and functional demands of modern applications. Building trust through expertise and sustained performance, stainless steel welding experts uphold the highest standards in their craft.