Stainless steel electrodes are pivotal components in various industrial applications, ranging from construction to automotive industries. Understanding their classification is crucial for selecting the right electrode for specific tasks, ensuring both safety and efficiency in operations. In this guide, we delve into the classification of stainless steel electrodes, drawing from first-hand experience and expert insights, to equip professionals with authoritative and reliable information.
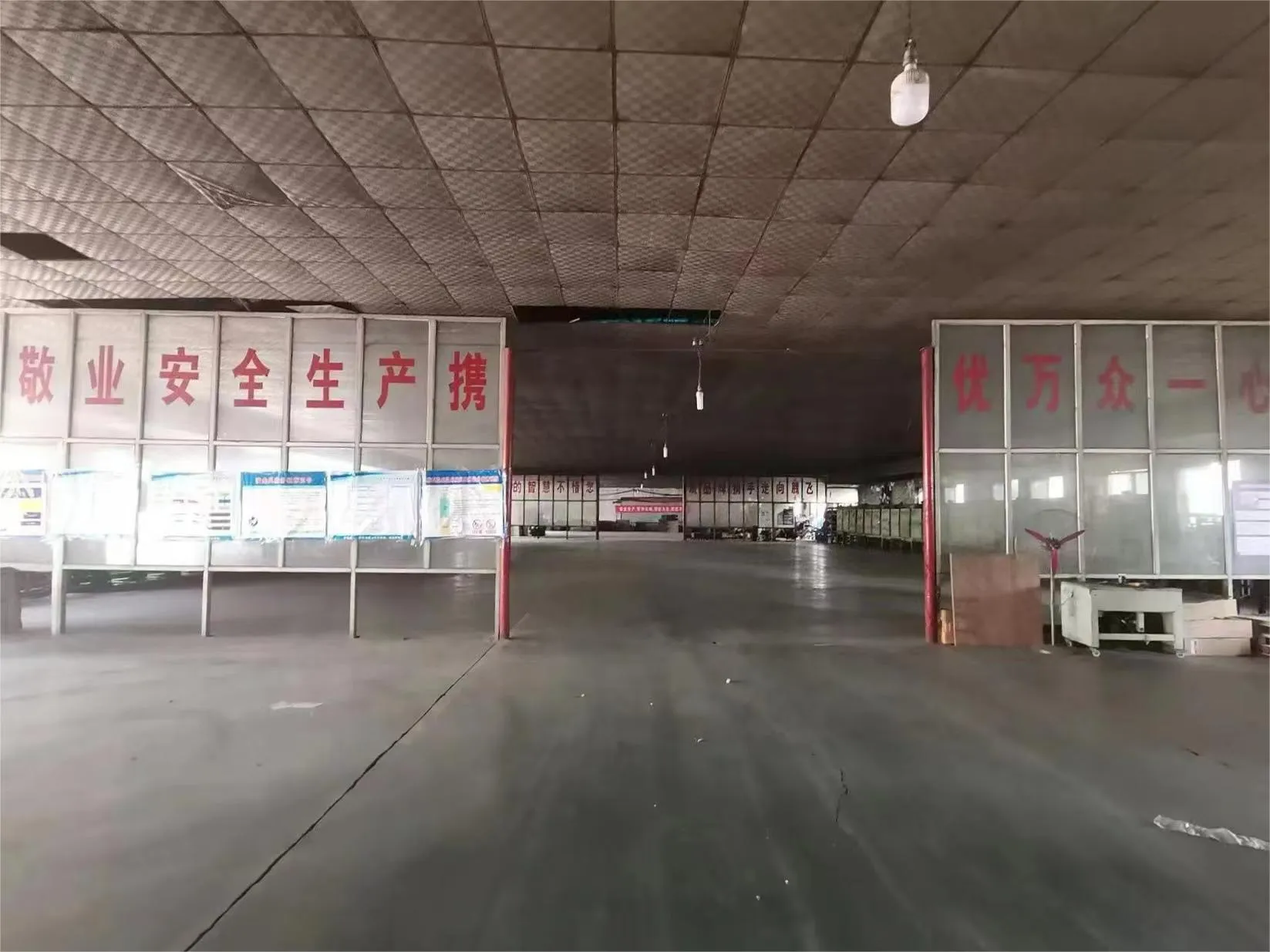
Stainless steel electrodes are categorized based on several parameters, including the type of stainless steel, the welding process, and the electrode coating. The classification system most commonly used is the AWS (American Welding Society) classification, which provides a standardized language for discussing electrode types.
One primary classification aspect is the type of stainless steel. Stainless steels are divided into several families austenitic, ferritic, martensitic, duplex, and precipitation-hardening. Each category possesses unique properties, such as corrosion resistance, strength, and ease of fabrication, which influence electrode selection.
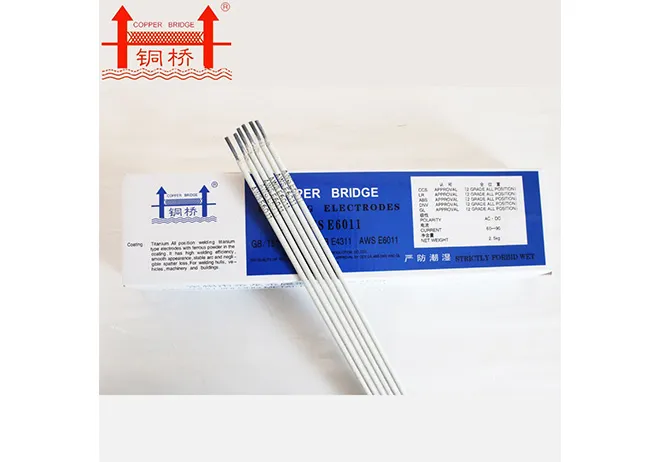
Austenitic stainless steels, represented by the 300 series, are renowned for their excellent corrosion resistance and formability. Electrodes like the E308L, E316L, and E309L are often used in welding austenitic steels. The 'L' denotes low carbon content, which minimizes carbide precipitation, enhancing corrosion resistance in welding seams.
Ferritic stainless steels, categorized under the 400 series, are known for their magnetic properties and resistance to stress-corrosion cracking. Electrodes such as E430 and E439 are matched with ferritic materials to capitalize on these characteristics.
Martensitic stainless steels require electrodes that can withstand high tensile strength and moderate corrosion resistance. Electrodes like E410 are suitable for applications demanding hardness and wear resistance.
Duplex stainless steels, characterized by a mixed microstructure of austenite and ferrite, offer superior strength and stress corrosion cracking resistance. Electrodes like E2209 and E2594 are crafted to maintain these properties even in challenging environments.
stainless steel electrode classification
The electrode coating is another critical classification criterion. Coatings serve multiple purposes they stabilize the arc, improve weld metal properties, and protect the molten metal from atmospheric contamination. There are three main types of electrode coatings rutile, basic (low hydrogen), and cellulosic.
Rutile electrodes contain titanium oxide, enhancing ease of use with a stable arc and smooth weld beads. They are preferable in situations where aesthetic weld appearance and ease of welding are prioritized.
Basic electrodes, also known as low hydrogen electrodes, are chosen for their superior mechanical properties and resistance to cracking. They are essential in demanding applications like pressure vessel fabrication and structural steelwork where weld integrity is non-negotiable.
Cellulosic electrodes, with a coating composed mainly of cellulose, provide deep penetration and fast freezing slag, making them ideal for vertical and overhead welding.
The welding process itself influences electrode selection. Shielded Metal Arc Welding (SMAW), Gas Tungsten Arc Welding (GTAW), and Gas Metal Arc Welding (GMAW) each have different requirements. SMAW, for example, utilizes consumable electrodes and requires precise electrode characteristics, while GTAW uses non-consumable tungsten electrodes demanding different considerations altogether.
In summary, selecting the appropriate stainless steel electrode involves understanding the material's application requirements, the intended welding process, and the specific characteristics of each electrode type. Working with the right electrode enhances weld quality, ensures safety, and maximizes efficiency. Through careful analysis and expertise-based selections, professionals can leverage stainless steel electrodes to their fullest potential, ensuring reliable and high-quality weld results. By using this detailed guide as a roadmap, professionals in the field can make informed decisions backed by experience and expert knowledge, laying the groundwork for successful, authoritative operations.