Stainless steel arc welding rods are a cornerstone of modern construction and manufacturing, and understanding their nuances is essential for anyone involved in welding or related industries. These rods, often referred to as stick electrodes, serve not only to fuse two metal components but also to enhance the structural integrity and durability of the joints. For industry professionals and hobbyists alike, selecting the right stainless steel welding rod can be the difference between a successful project and a costly failure.
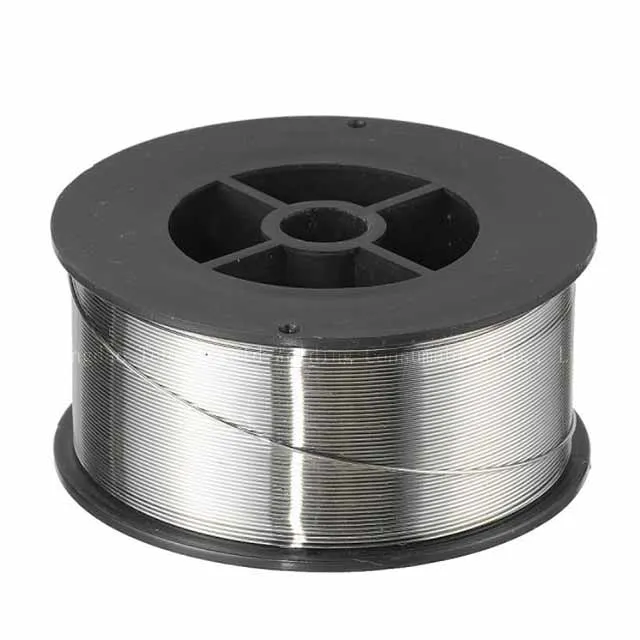
When discussing experience in using stainless steel arc welding rods, it’s crucial to acknowledge the various types available and their unique applications. The selection process begins with understanding the material composition. Stainless steel electrodes are typically composed of a combination of chromium, nickel, and sometimes molybdenum. This composition ensures that the welded joint maintains corrosion resistance and high tensile strength, attributes that are particularly important in industries such as automotive, aerospace, and construction.
The most commonly used types of stainless steel arc welding rods include 308, 309, and 316. Each of these rods serves different purposes based on their unique properties. For example, 308 rods are often used for general-purpose welding of stainless steel. They are optimal for joining similar or dissimilar materials and are noted for their smooth arc and ease of use. In contrast, 309 rods are better suited for welding stainless steel to mild steel, as their composition includes a higher chromium and nickel content, which accommodates the differing expansion rates of these metals during heating and cooling cycles.
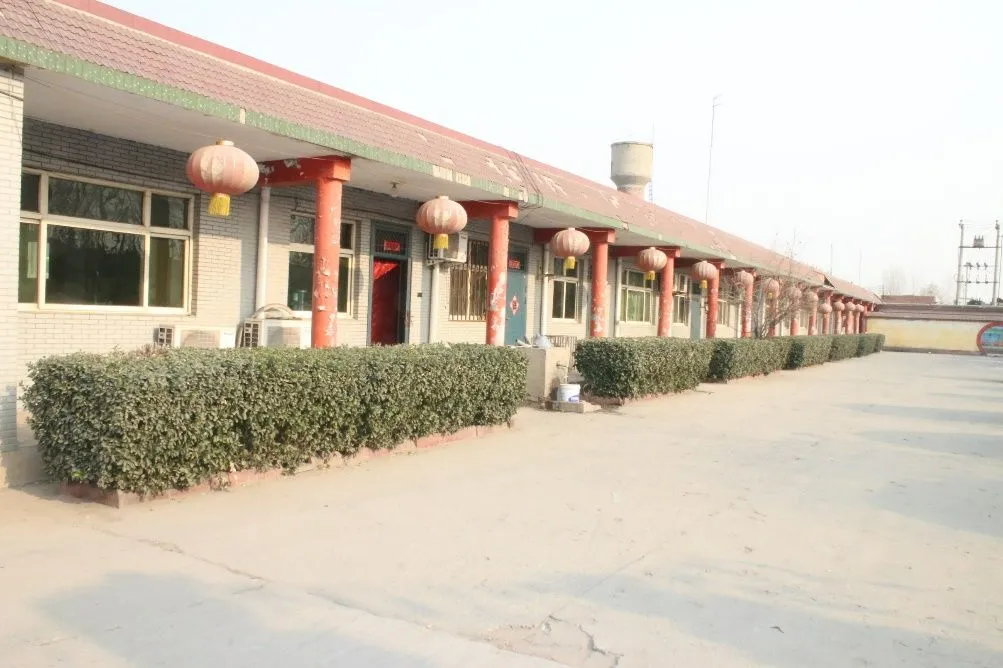
Professional expertise in the field of stainless steel welding involves understanding the welding techniques that are tied to specific types of rods. For instance, maintaining the proper arc length and angle is critical for achieving high-quality welds. An experienced welder will also be mindful of the amperage settings; using too much or too little can result in excessive spatter or weak welds. Ensuring the correct polarity is another technical aspect that seasoned experts emphasize to mitigate common problems such as arc blow—a condition where the arc becomes erratic due to magnetic interference.
stainless steel arc welding rods
Authoritativeness in stainless steel arc welding comes from a firm grasp of industry standards and certifications. Compliance with the American Welding Society (AWS) standards, such as AWS A5.4,
which classifies stainless steel electrodes, is paramount. These standards guide professionals in selecting the appropriate rods for their projects, ensuring consistency, safety, and quality across all applications. Furthermore, adherence to these standards indicates a commitment to excellence and reliability—an essential characteristic in the eyes of stakeholders.
Trustworthiness is built through consistency, transparency, and quality assurance. Suppliers and manufacturers of stainless steel welding rods often provide detailed documentation and material certificates that prove their products have undergone rigorous testing and meet industry standards. Engaging with suppliers who offer such documentation bolsters trust and ensures the credibility of the welding materials used. In addition, first-hand testimonials and case studies showcasing the successful use of these rods in various projects and environments also elevate trust. Sharing experiences and outcomes, both positive and negative, fosters an environment where practitioners learn from each other's pursuits and challenges, enhancing the collective knowledge base.
In conclusion, the world of stainless steel arc welding rods is rich with variables and complexities that necessitate a comprehensive understanding of their properties, uses, and standards. Whether you're a seasoned professional or a novice welder entering the field, recognizing these factors is crucial to improving your welding technique and ensuring that your projects stand the test of time. The commitment to staying informed and continually refining your skills will not only lead to superior craftsmanship but also secure your reputation as a trusted expert in the art of welding.