Navigating the world of welding demands a comprehensive understanding of materials, especially when it comes to selecting the right stainless steel filler rod. This crucial component plays a significant role in ensuring the structural integrity and aesthetic finish of a project. Here's an in-depth exploration of how stainless filler rods enhance welding experiences, with a focus on practical applications, expert insights, and essential tips for both professionals and hobbyists.
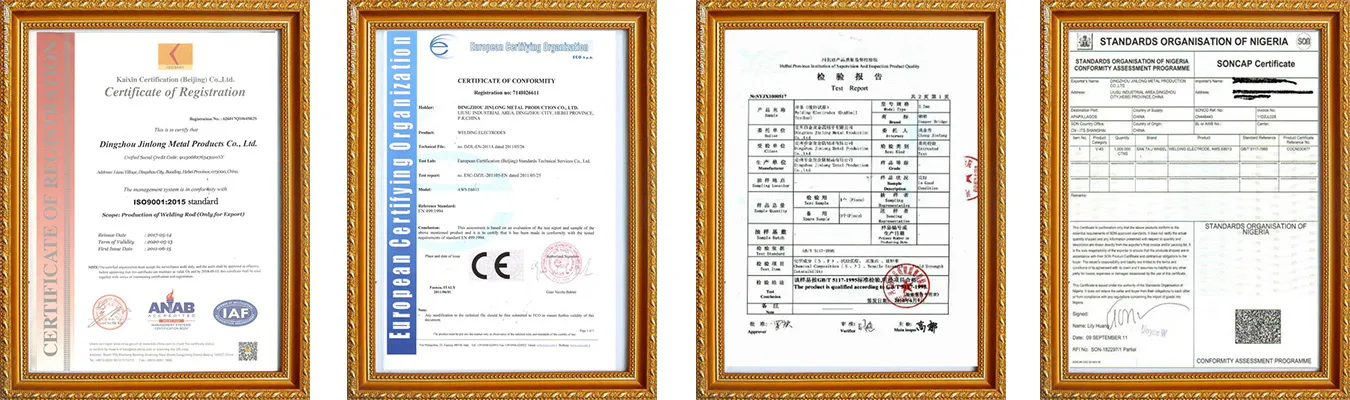
When tackling stainless steel welding projects, the choice of filler rod can significantly impact the weld quality.
Stainless filler rods come in various grades, each designed for specific types of stainless steel. This ensures compatibility with the base metal, minimizing the risk of corrosion and maximizing the strength of the weld. Commonly used grades such as ER308L, ER309L, and ER316L offer different properties. For example, ER308L is ideal for welding 304 stainless steel due to its low carbon content, which prevents carbide precipitation during the welding process, preserving corrosion resistance.
For welders, longevity and performance under stress are paramount. Stainless filler rods are preferred in environments where durability and exposure to the elements are concerns. This includes industries such as aerospace, food processing, and pharmaceuticals, where clean finishes and the ability to withstand harsh conditions are non-negotiable. Expert welders often recommend matching the filler rod to the specific application requirements, such as choosing ER316L for projects exposed to saline environments, given its superior resistance to chlorides.
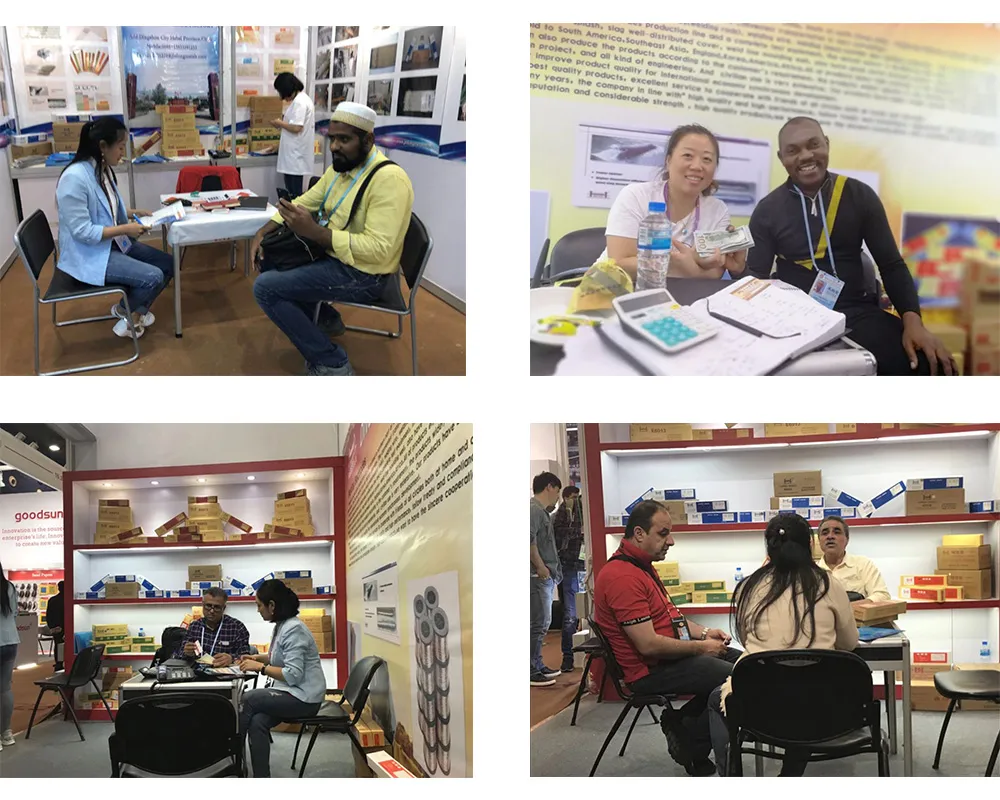
Drawing from authoritative sources and welding professionals' experiences, the preparation of the welding area is crucial. Proper cleaning of both the workpieces and the filler rod removes contaminants that could weaken the weld or introduce impurities. The use of appropriate shielding gases, like Argon or Helium, is also essential to protect the arc and optimize the weld pool. Skilled welders emphasize maintaining a consistent technique, with a steady hand and appropriate heat control, ensuring a precise and strong joint.
stainless filler rod
Trust in the quality of stainless filler rods is reinforced through certifications and compliance with industry standards, such as those set by the American Welding Society (AWS). When purchasing filler rods, ensuring they meet these rigorous standards is a testament to their reliability and effectiveness in various applications. Manufacturers providing detailed specifications and testing certifications enable users to make informed choices, thereby ensuring the credibility of their products.
Moreover, embracing a learning mindset and seeking continuous improvement aligns with the evolving field of welding. Engaging in forums, attending workshops, and consulting with veterans in the industry can offer practical insights into optimizing the use of stainless filler rods. The exchange of ideas and experiences strengthens the welding community's collective expertise and fosters a culture of trust and innovation.
In summation, the use of stainless filler rods is a nuanced decision that balances experience with technical knowledge. Whether it's ensuring the resistance of a structure against environmental stressors or achieving a flawless aesthetic in a food-grade setting, the suitable selection and application of these rods are central to success. By investing in high-quality materials and adhering to best practices, welders can achieve exceptional results, reinforcing the foundation of trust and professionalism inherent in the trade.