Mastering Stainless Electrode Welding An Expert Guide to Precision and Performance
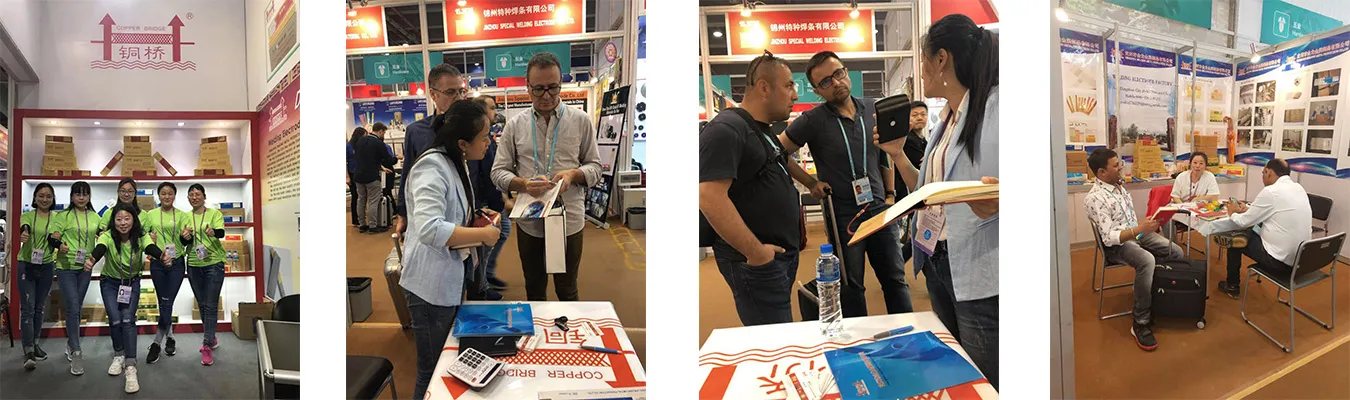
Stainless electrode welding is a critical process in various industries, from construction to automotive. The use of stainless steel electrodes is essential for projects that demand high durability and resistance to corrosion. As an experienced professional in this field, I've witnessed the transformation and improvements in welding techniques and technologies. Here’s an exploration into the intricacies of stainless electrode welding that not only underscores its importance but also provides insights from a seasoned perspective.
Understanding Stainless Electrode Welding
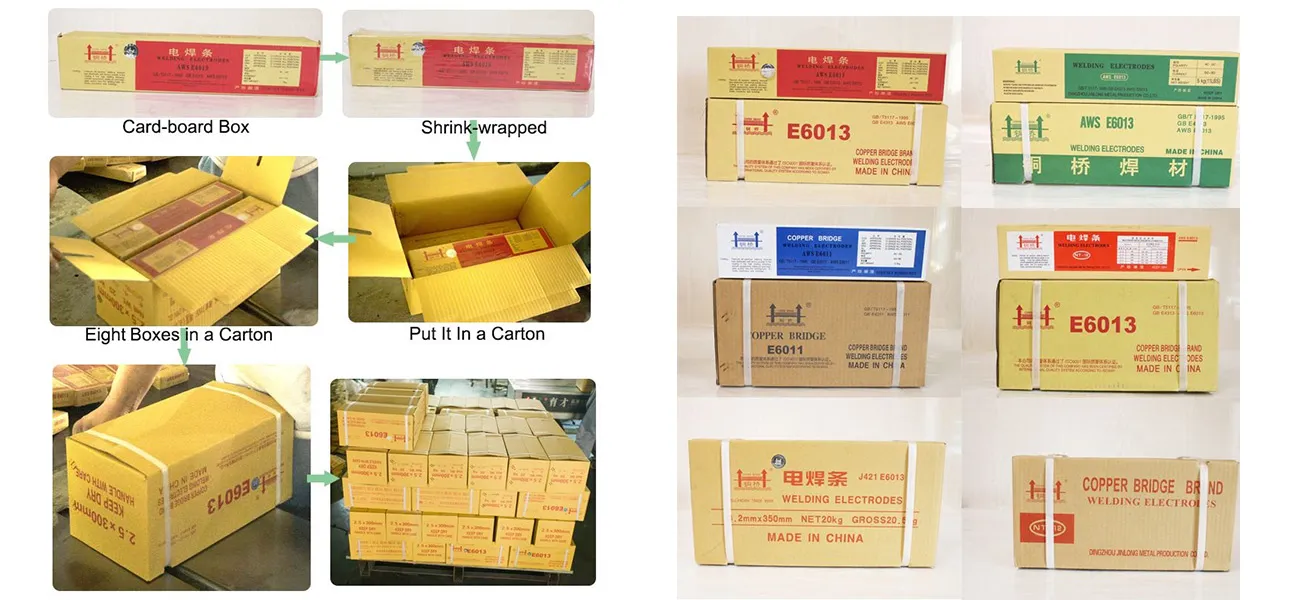
Stainless steel electrodes are integral for projects requiring a strong and rust-resistant finish. These electrodes come with unique challenges due to the composition of stainless steel, which includes chromium, nickel, and other elements. The primary objective of welding with these electrodes is to ensure a robust joint while maintaining the material’s inherent properties.
Key Considerations in Selecting the Right Electrode
The choice of the electrode impacts the welding quality significantly. Important factors include
1. Composition The electrode’s composition should match the base metal. For instance, for 304 stainless steel, an AWS E308L electrode is typically recommended. Deviating from these can lead to joint failures.
2. Coating Type Various coatings like rutile and basic are available, which influence factors such as the ease of welding, penetration, and slag removal. Rutile-coated electrodes offer smooth arc performance, while basic-coated types assure deeper penetration and strength.
3. Size and Diameter The electrode size should align with material thickness. Thinner materials necessitate smaller electrodes to prevent burn-through.
Techniques for Optimal Welding
Achieving optimal welding performance requires mastering several techniques
1. Accurate Current Setting To prevent overheating and warping, the welder must set the current appropriate to the electrode’s diameter. A lower current might lead to lack of fusion, while excessive current can cause distortion.
2. Electrode Angle Holding the electrode at the correct angle is crucial. An angle of 70 to 80 degrees for fillet welds ensures proper penetration without defects.
3. Travel Speed Consistency in travel speed prevents excess deposit of the weld metal or undercut. Practice is key to maintaining a steady, moderate speed.
stainless electrode welding
Overcoming Challenges in Stainless Electrode Welding
Stainless steel welding presents challenges such as warping and sensitization. These can be overcome by
1. Preheating Preheating prevents thermal shock and reduces the risk of warping.
2. Intermittent Welding For large sections, welding in short sections allows the material to cool, minimizing deformation.
3. Post-Weld Treatment Processes like passivation or pickling can restore the material’s chromium oxide layer, crucial for corrosion resistance.
Innovations and Tools Enhancing Welding Efficiency
Advancements in technology have further refined welding practices. Use of inverter-based welding machines allows precise control over the welding parameters, reducing energy consumption. Additionally, developments in electrode formulation have led to enhanced stability and minimized spatter.
These tools, coupled with protective gear like auto-darkening helmets and ergonomically designed gloves, have elevated both safety and efficiency for welders.
Trust in Expertise and Proven Practices
The mastery of stainless steel electrode welding is a blend of understanding material science, technological adeptness, and continuous learning. Professionals in the industry sustain their expertise by engaging in regular training and staying updated with the latest standards and practices.
Documented case studies and shared professional experiences also fortify credibility, proving invaluable in resolving real-world welding issues. Ensuring adherence to industry certifications and standards like the American Welding Society (AWS) further solidifies trust and authority in services offered.
Conclusion
Stainless electrode welding is not merely a skill but a fusion of art and science. Precision, endurance, and expertise culminate to produce welds of impeccable quality and strength. The continuous evolution of techniques and equipment promises enhanced outcomes, underscoring the importance of experience and authoritative knowledge in this specialty. Whether you are a seasoned welder or a project manager, understanding these facets will transform the approach to stainless electrode welding, leading to superior performance and longevity in applications.