The stainless steel welding electrode is an indispensable tool in industries where metal fabrication and construction are paramount. A critical element for joining stainless steel components, these electrodes ensure reliability, structural integrity, and longevity in various applications. From aerospace to construction, understanding the nuances of stainless steel welding electrodes paves the way for superior quality and performance in welding projects.
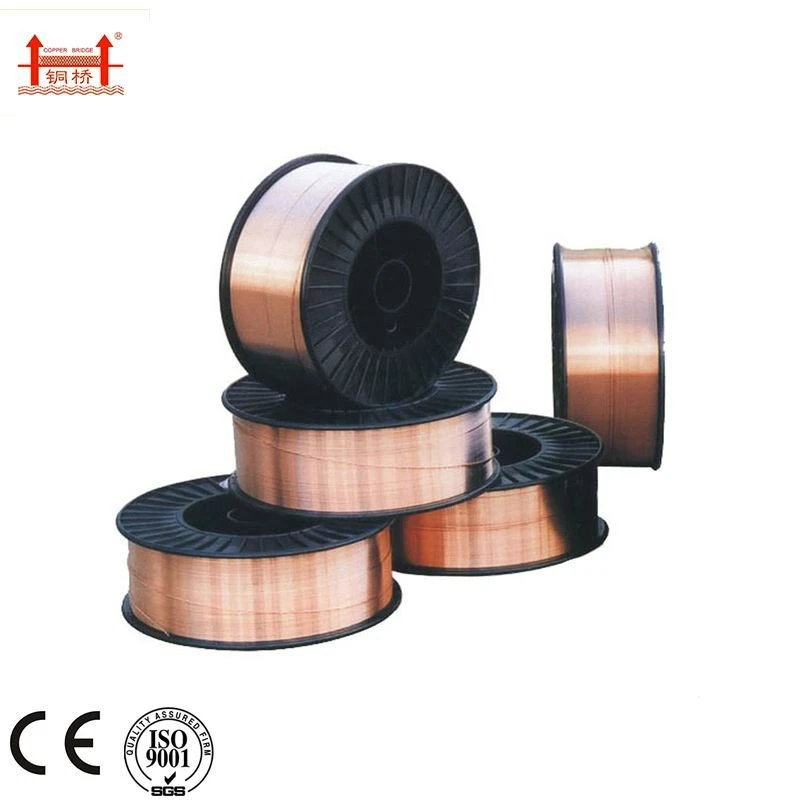
One of the key attributes of stainless steel welding electrodes is their composition. Stainless steel contains chromium, which forms a protective layer, rendering it resistant to corrosion and oxidation. When welding stainless steel, the electrode must match the material in order to maintain these properties. For instance, an electrode with a 304 designation typically complements a 304 stainless steel base. This alignment is crucial for preventing chemical dissimilarity that might compromise the welded joint's durability.
Deciphering the various types of stainless steel electrodes further illustrates their expertise in specialized applications. For instance, depending on the welding position and specific project requirements, professionals might select an electrode such as E308L-16, which is particularly advantageous for its low carbon content. This low carbon composition mitigates the risk of carbide precipitation at the grain boundaries, hence preventing intergranular corrosion, a common threat to welds in high-temperature environments.
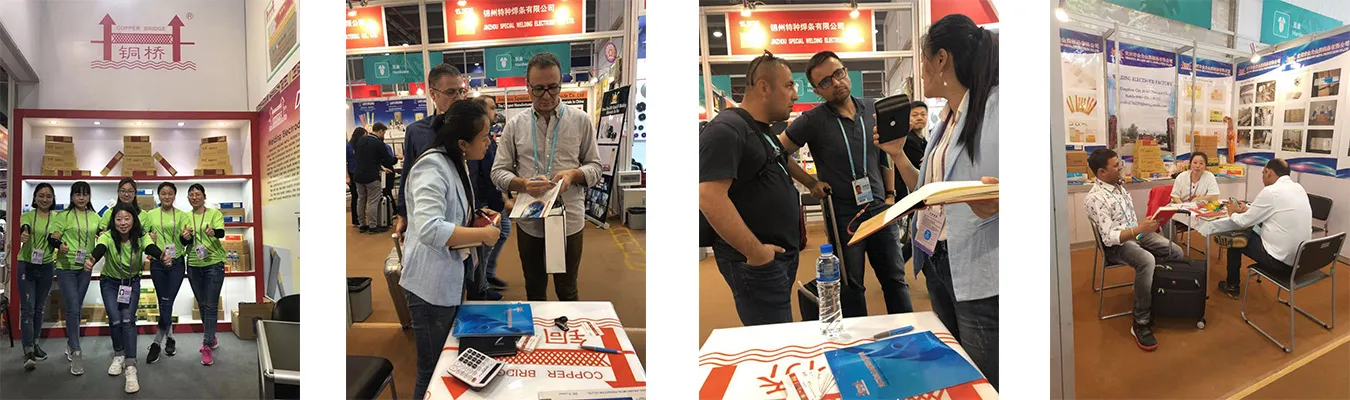
Stainless steel electrodes are not just about composition and compatibility; the electrode coating also plays a pivotal role. Coatings can be rutile, cellulosic, or basic, each influencing arc stability, slag removal, and bead appearance. Rutile-coated electrodes, for example, offer smooth arcs and an easy-to-remove slag, making them favorable for aesthetic welds and ease of use. This professional nuance is essential for welders seeking to balance operational efficiency with the highest standards of weld aesthetics.
ss welding electrode
The crafting of a quality weld also demands attention to technique and equipment. Welders must ensure that the welding machine settings align with the electrode specifications. Improper amperage, for instance, can lead to an unstable arc, excessive spatter, or even weld defects such as porosity or cracking. Professionals recommend undergoing rigorous testing and calibration of welding machines to align with the optimal settings prescribed by electrode manufacturers. This practice not only fosters the electrode’s authoritative performance but also enhances trustworthiness in the welding operations.
Ensuring safety and environmental considerations further highlights the trustworthiness of stainless steel welding electrodes. As these electrodes are often employed in environments where heat and fumes are prevalent, using them responsibly with appropriate ventilation systems reduces health risks. Welding professionals are encouraged to employ personal protective equipment (PPE) such as masks, gloves, and eye protection to safeguard against harmful particulates.
Beyond the physical use, the logistical aspects also underscore the systemized expertise of stainless steel welding electrodes. Proper storage is critical electrodes should be kept in a dry, humidity-controlled environment to prevent moisture absorption, which can compromise the coating and cause hydrogen-induced cracking in welds. Manufacturers often provide guidelines or storage solutions, reinforcing the authoritative stand by which these electrodes are maintained to ensure optimal performance during use.
Understanding these technical intricacies of stainless steel welding electrodes not only amplifies their functional efficacy but also enhances the credibility of welding operations across industries. With the continual advancements in electrode technology accompanied by rigorous adherence to metallurgical principles, these components uphold the standards of quality, durability, and reliability essential in today’s diverse industrial applications.