Selecting the right welding rod for a project often determines the success and integrity of the weld.
In the realm of welding, precision is paramount. This holds especially true when navigating the transition between stainless steel (SS) and mild steel (MS). Choosing the correct welding rod number is a critical factor that not only influences the weld's strength but also its corrosion resistance and aesthetic appeal.
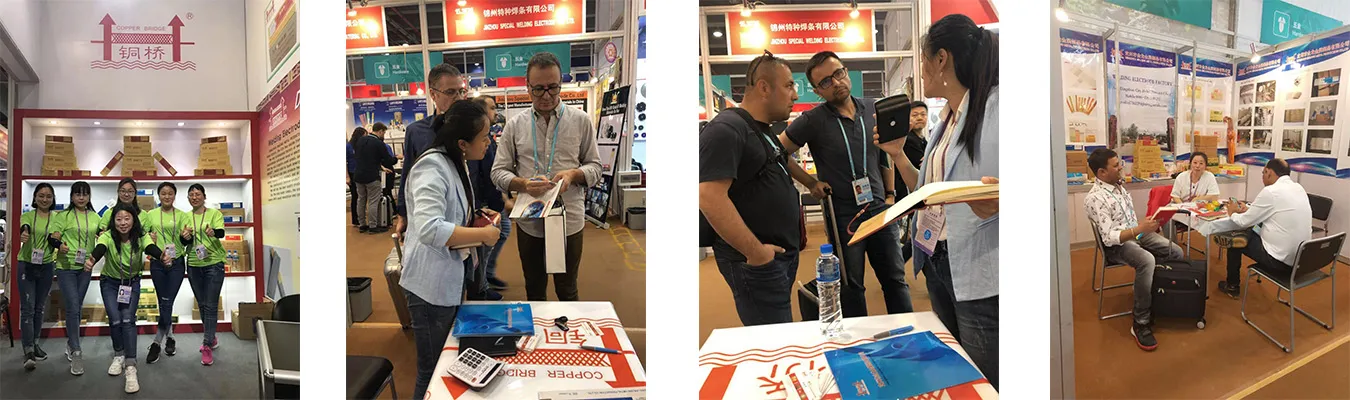
When welding SS to MS, the 309L-16 welding rod is often heralded as the industry standard, known for its exceptional versatility and reliability. This electrode is engineered to accommodate the differing thermal expansion rates and metallurgical properties inherent in SS and MS materials. The 309L-16 rod's low carbon content reduces carbide precipitation in the weld metal, ensuring a robust and corrosion-resistant joint.
Welders with years of hands-on experience testify to the seamless bead quality achieved when using the 309L-16. Its ability to maintain the integrity of the weld in varied temperature environments is notable. Moreover, its usability in both AC or DC+, and the user-friendly arc stability, make it a preferred choice among skilled professionals. The ease of slag removal further enhances its appeal, contributing to a cleaner weld finish and reducing the need for post-weld clean-up.
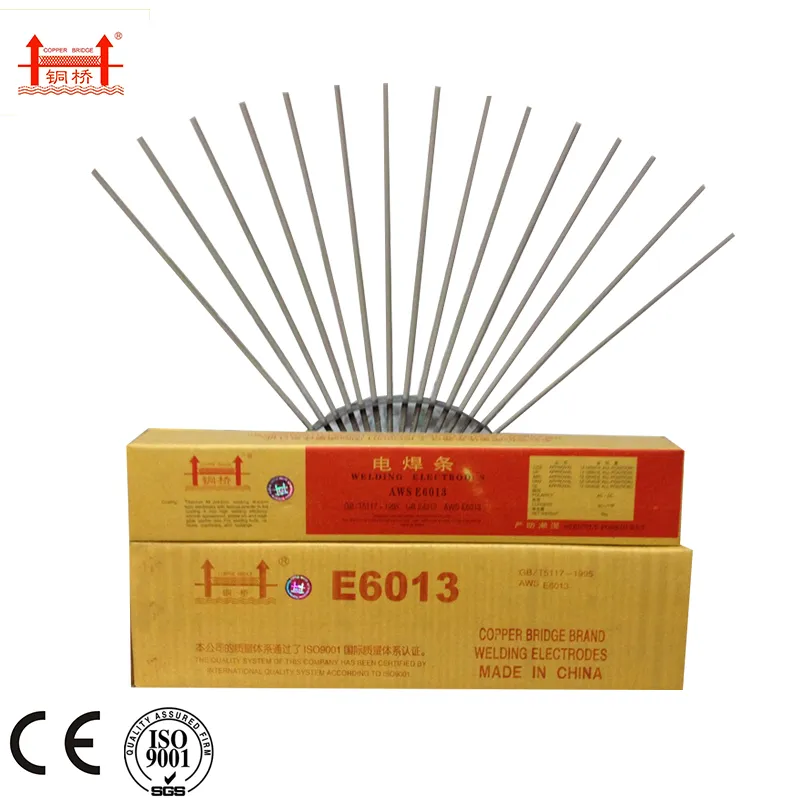
Yet, practical application often proves to be the best test of any welding rod's efficacy. Several expert welders emphasize conducting a trial with different rods to discern which one offers the best results in terms of tensile strength and ductility for their specific material combination. While the 309L-16 is typically recommended, certain projects with unique stress limits may require alternate solutions, like the 308L for smaller scale or less demanding applications.
Understanding the metallurgical science behind these rods fosters informed decisions. The filler metals in the 309L are specifically designed to create an austenitic stainless steel weld deposit that matches or surpasses the base metals' resilience. This is crucial when joining dissimilar metals which respond differently to thermal loads, often causing weld failures if improper filler materials are used.
ss to ms welding rod number
Authoritative insights into the broader spectrum of welding rods available for SS to MS applications underscore the importance of balancing cost and performance. Alternatives to 309L, such as E309MoL-16, offer added molybdenum for increased resistance to pitting and crevice corrosion. Such variants may come at a higher cost but provide an essential solution for specialized environments where chemical exposure is high.
In terms of reliability, the trustworthiness of the weld can be further maximized by adhering to stringent preparation practices. Thorough cleaning of the metal surfaces to eliminate contaminants, coupled with precise heat control, enhances the weld quality. Expert welders advocate for a consistent welding speed and bead pattern to minimize distortions across the different metal types. These meticulous practices underscore the commitment to weld integrity and longevity.
Finally, embracing advancements in welding technology and continuous skill development can greatly amplify the effectiveness of using the 309L-16 and similar rods. Training programs and certifications from recognized bodies ensure that welders remain abreast of industry standards and innovations, thus maintaining high levels of workmanship.
In conclusion, the selection of the appropriate welding rod number when welding SS to MS is pivotal, with the 309L-16 standing out as a premier choice for achieving balance between performance, cost, and adaptability. Through a combination of expert recommendations, practical experience, and ongoing education, welders can ensure exceptional results, reinforcing their reputation and delivering work that meets the most demanding requirements.