Selecting the right welding rod for stainless steel pipes is crucial for any construction or repair project. As an experienced welding professional, I've had the opportunity to explore different techniques and tools that enhance both efficacy and durability in welding processes. Below, I provide insights into the realm of stainless steel pipe welding rods, based on years of expertise, and how they contribute to achieving high-quality results.
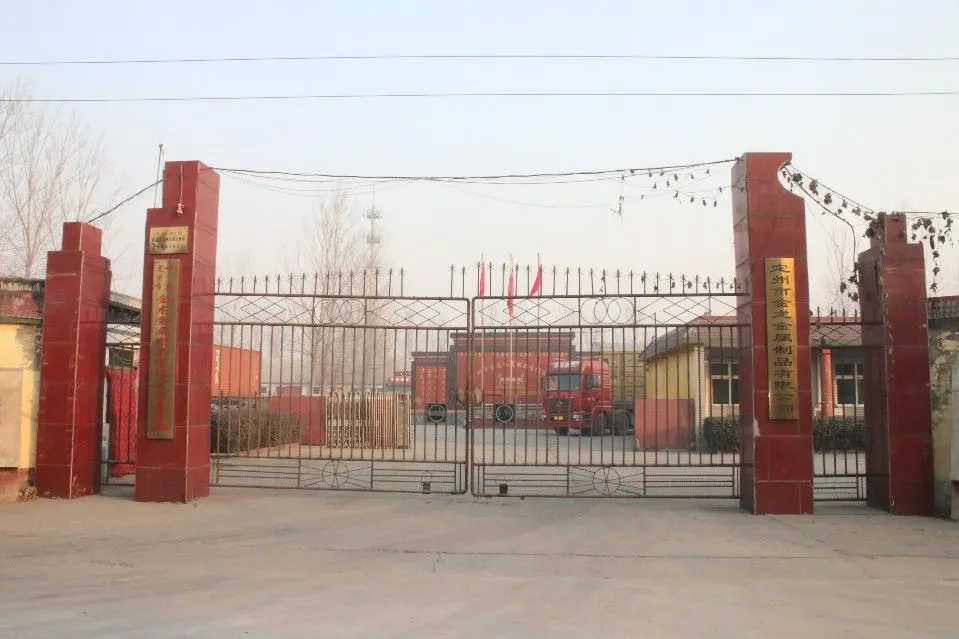
When working with stainless steel pipes, the choice of welding rod significantly affects the structural integrity and longevity of the weld. The most commonly used welding rods for stainless steel pipes are 308L, 309L, and 316L, each catering to specific needs based on the pipe material and application.
308L is ideal for welding 18-8 stainless steels, often referred to as 304. This rod offers a low carbon content, which plays a pivotal role in curbing carbide precipitation, thus preventing intergranular corrosion. Using 308L rods ensures robust and long-lasting joints, particularly significant in environments exposed to high temperatures and corrosive elements.
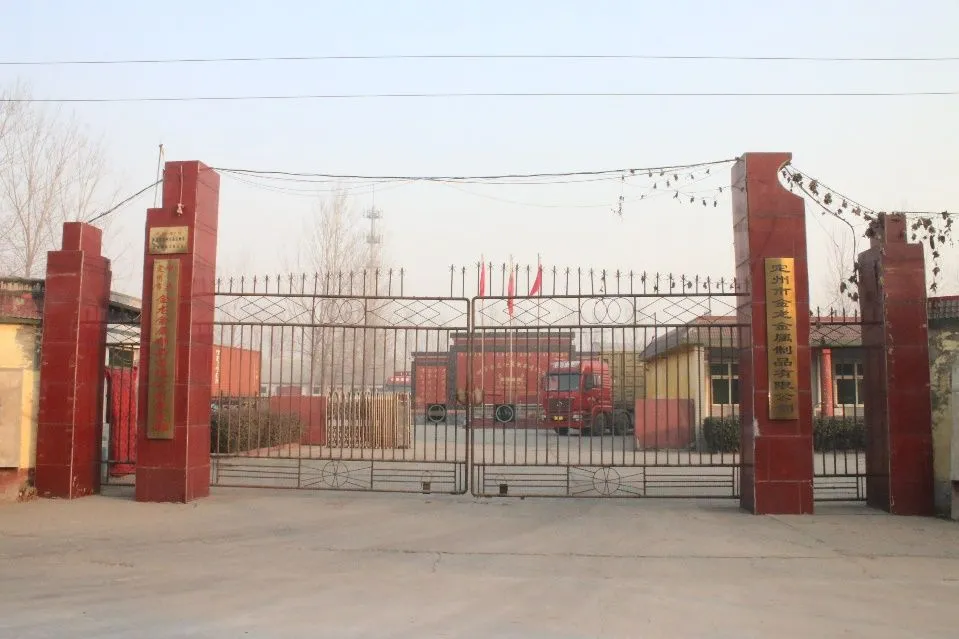
309L rods come into play when welding dissimilar metals, such as joining stainless steel to carbon steel. Their formulation is calibrated to minimize brittleness and cracking, common challenges in heterogeneous metal welding. This rod is a definitive choice for projects that demand flexibility and adaptability, without compromising on weld quality.
For applications involving marine or high chloride environments, 316L rods are indispensable. They contain molybdenum, boosting their resistance to pitting and crevice corrosion. This added layer of protection makes them suitable for harsh environments, ensuring the welded joints endure both exposure and stress over time.
The technical proficiency of using these rods extends beyond selection. The methodology is integral too. In my extensive professional practice, meticulous preparation of the stainless steel surface before welding cannot be understated. Cleaning the surface of contaminants like oil, dirt, and rust is paramount to preventing weld defects such as porosity. Employing a groove angle of 30 degrees and maintaining a wider root opening can aid in achieving better penetration, especially for thicker pipes.
ss pipe welding rod
Preheating is another technique that should not be overlooked. Although stainless steel requires minimal preheating compared to other metals, a uniform temperature helps reduce thermal distortion, an enhancement that can't be ignored for achieving precision welds.
Aside from the technical aspect, understanding the nuancs of rod handling and storage ensures their longevity and performance. Rods should be stored in controlled environments to prevent moisture absorption which can cause hydrogen embrittlement in welds, a pervasive problem that compromises weld stability.
Leveraging state-of-the-art welding machines with adaptable settings can optimize the usage of these rods, ensuring the maintenance of steady heat input, which is crucial in controlling the microstructure of the weld metal and heat-affected zones.
Finally, documentation and continual education are instrumental in ensuring weld quality and safety. Each project offers learning curves; keeping a log facilitates reflection and improvement. Attending regular training and certification programs keeps one abreast of the latest in technology and safety standards, reinforcing one's authority and trustworthiness in the field.
Navigating the complexities of welding stainless steel pipes involves an amalgamation of expertise and practical knowledge. By understanding the intricacies of welding rods and incorporating best practices, professionals can achieve superior outcomes that stand the test of time and elements, thereby attaining greater client satisfaction and establishing industry reliability.