Selecting the right filler rod for TIG welding stainless steel is crucial for achieving strong, precise, and aesthetically pleasing welds. TIG welding, known for its precision and control, is a preferred method when working with stainless steel due to its ability to produce clean and high-quality joints. Understanding the properties, selection criteria, and applications of SS filler rods can significantly enhance the reliability and performance of your welding projects.
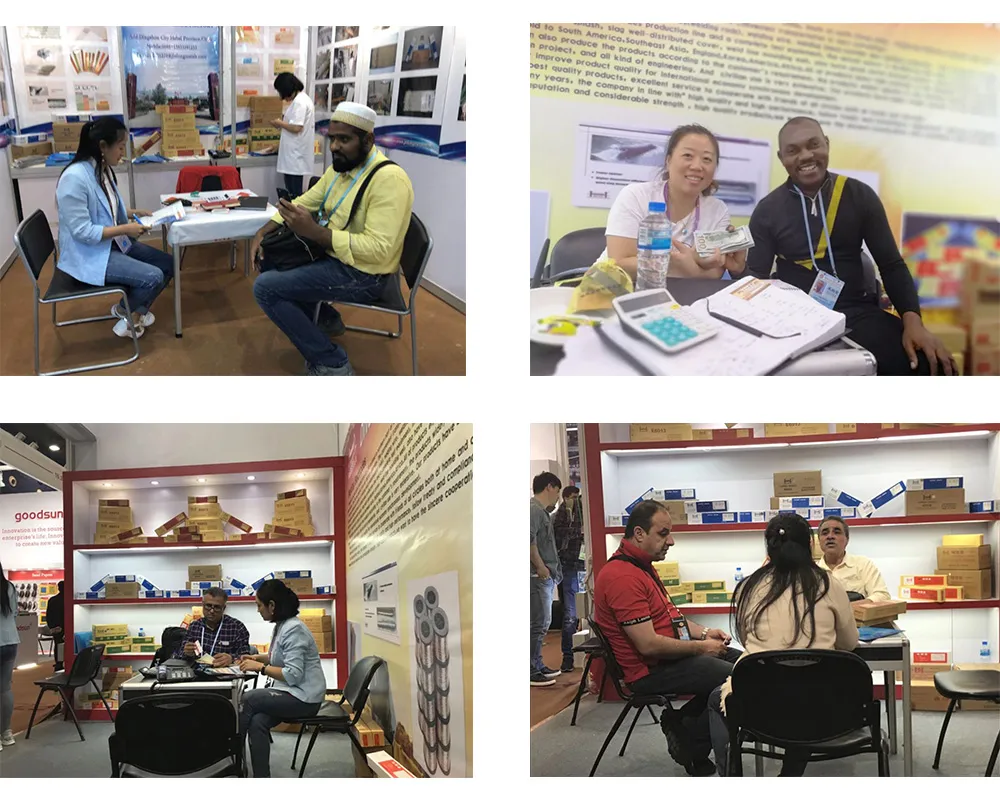
When working with stainless steel, corrosion resistance, strength, and aesthetic finish are critical factors to consider.
The SS filler rods for TIG welding are designed specifically to complement these requirements. Typically, the commonly used filler rods for stainless steel TIG welding are 308L, 309L, and 316L, each offering unique benefits tailored to specific types of stainless steel.
308L is widely used for welding similar base metals such as 304L or 308L stainless steels and is well-regarded for its excellent corrosion resistance and strength. The low carbon content in 308L enhances its resistance to intergranular corrosion, which can be a concern in welding due to the high temperatures involved.
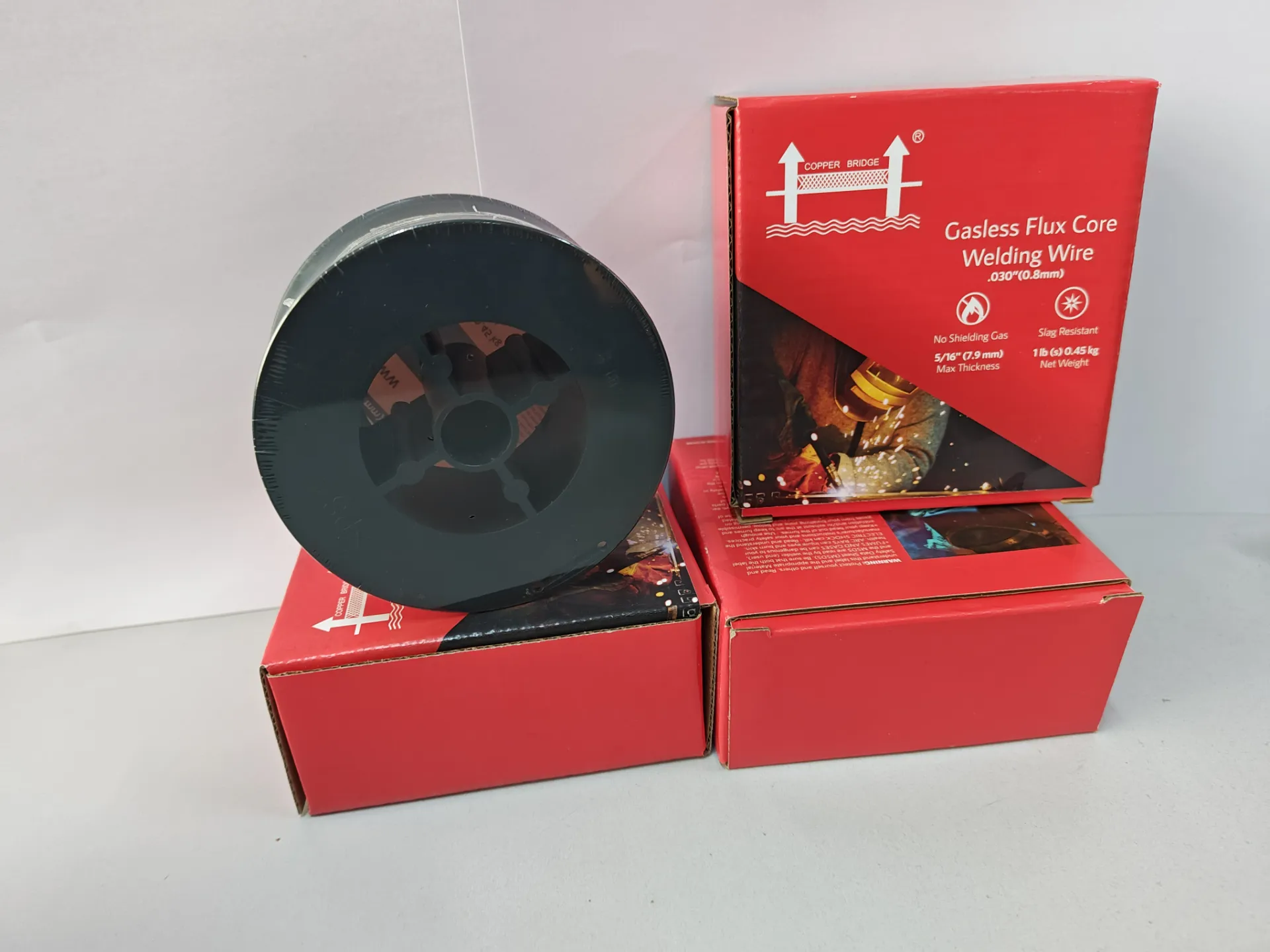
309L filler rods are employed when welding dissimilar stainless steels, such as stainless to carbon steel. This rod is also used for welding base metals of 309 stainless steel due to its high chromium and nickel content, which provide superior oxidation resistance. This attribute makes 309L ideal for applications subjected to high temperatures, such as in furnace parts or similar environments.
For applications demanding higher corrosion resistance, especially in chloride environments, 316L is the preferred choice. Its molybdenum content provides additional resistance to pitting and crevice corrosion, making it suitable for marine environments or chemical processing applications. Like 308L, the low carbon content of 316L prevents carbide precipitation, thereby maintaining its corrosion resistance after welding.
Expert TIG welders often emphasize the importance of proper filler rod selection to ensure that the mechanical properties of the weld match those of the base metal. This compatibility is essential for structural integrity and prolonging the lifespan of the welded assembly. A mismatch can lead to weak welds, causing premature failure under stress or exposure to corrosive elements.
ss filler rod for tig welding
Additionally, these filler rods are known for their reliable performance across various positions and joint designs. They provide a smooth arc operation and predictable bead appearance, which is vital for projects where the aesthetic appeal of the weld is as important as its function.
The technique used in TIG welding stainless steel also involves expertise. A successful weld requires careful control over heat input to prevent warping or distortion of the metal. Using a proper back-purge with argon gas is another critical practice to protect the weld's backside from oxidation, which can compromise its corrosion resistance.
Authoritative industry sources recommend conducting a thorough analysis of the base material and its operational environment before selecting a filler rod. This analysis should include the chemical composition, mechanical properties, and exposure conditions. Manufacturers often provide datasheets that detail these properties for filler rods, offering valuable guidance for making an informed choice.
Trustworthiness in the choice of a filler rod provider is equally important. Opt for reputable manufacturers with certifications and quality assurance processes that guarantee reliable and consistent products. Regularly updated standards from organizations like the American Welding Society (AWS) offer a benchmark for quality that trustworthy manufacturers adhere to.
In conclusion, the selection of an SS filler rod for TIG welding is not merely a technical decision but a crucial step that determines the quality and durability of the welded structure. Leveraging professional expertise, adhering to authoritative guidelines, and relying on certified products from reputable manufacturers are essential strategies for achieving optimal welding outcomes, ultimately enhancing both the performance and longevity of stainless steel applications.