The welding world often introduces a myriad of electrodes, each offering distinct advantages depending on the application. Among them, the AWS E6011 electrode stands out for its exceptional versatility and adaptability, making it a staple choice for many welding professionals.
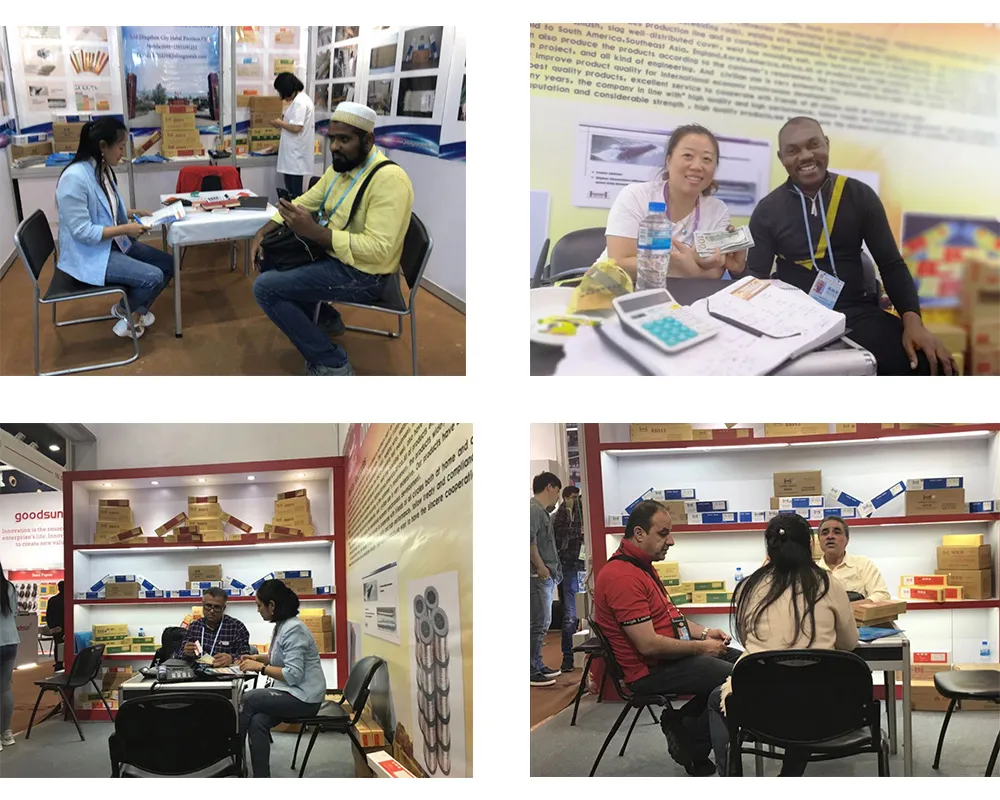
The AWS E6011 electrode is recognized for its unique ability to produce a deep penetration weld, which is crucial for working with materials that might have surfaces covered in rust, paint, or mill scale. This feature is particularly beneficial in industries where surface preparation cannot always be executed to perfection, such as in pipeline or farm equipment repairs.
One of the distinguishing features of the E6011 is its cellulose-based flux coating. This coating allows the electrode to produce an intense arc, which can effectively tackle dirty or oxidized surfaces, often eliminating the need for extensive pre-cleaning. Moreover, this type of coating is responsible for the electrode's capability to weld in all positions, including vertical and overhead, which enhances its utility across various applications.
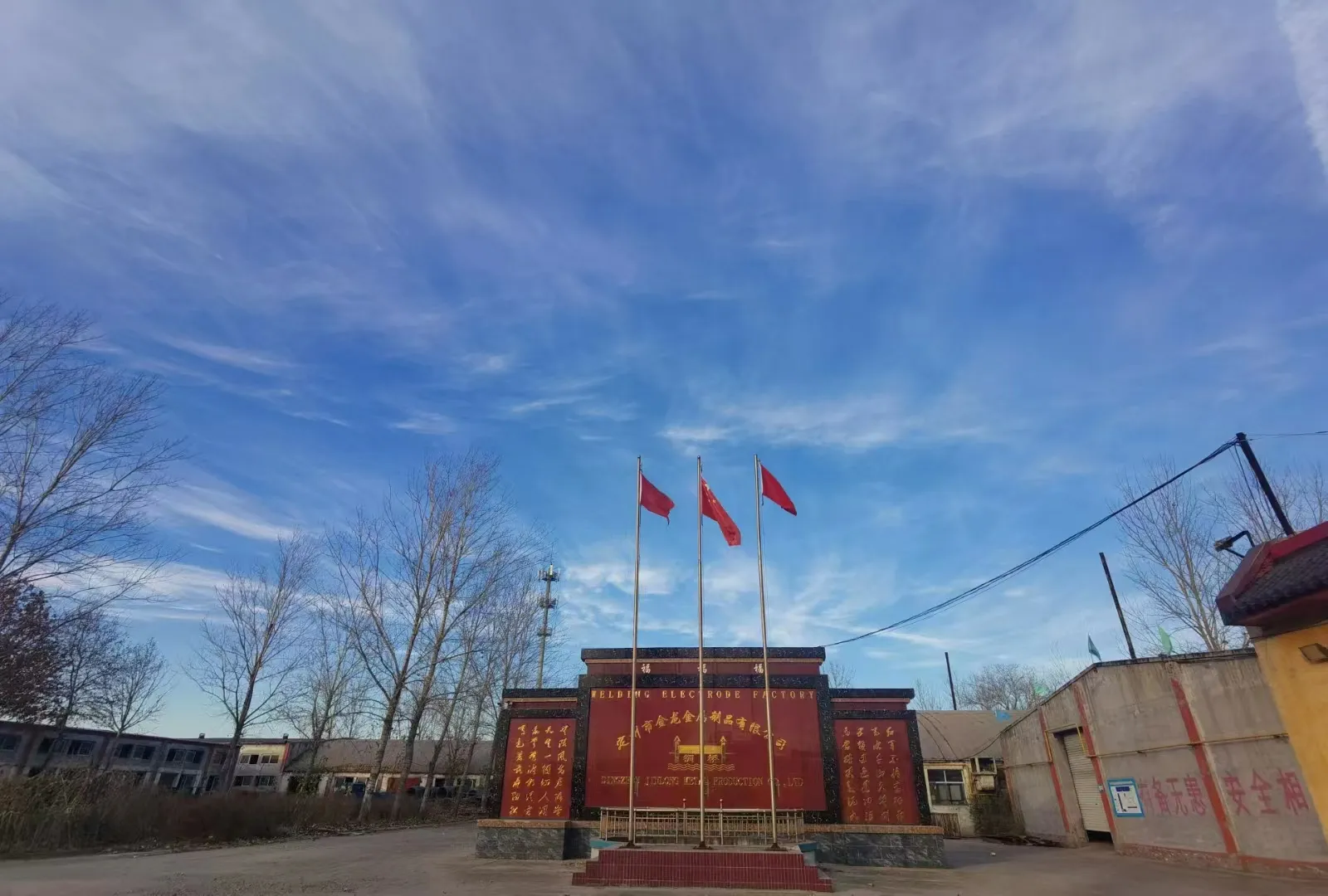
In terms of expertise, understanding the operating characteristics of the E6011 is vital. It runs on both AC and DC (either polarity), providing flexibility in settings where power sources may differ. The AC compatibility is particularly advantageous for welders who rely on power from generators, which might provide inconsistent current. For welders aiming to maximize their performance with E6011, a nuanced comprehension of adjusting current and maintaining correct arc length is crucial. Proper technique ensures minimized slag inclusions and optimal bead appearance.
From an authoritative perspective, the E6011 is often recommended by seasoned professionals for repair and maintenance tasks. Its capacity to weld through contamination with minimal difficulty saves not only time but also resources, aligning well with industrial efficiency standards. Additionally, industry experts emphasize the importance of post-weld operations, such as cleaning and inspection, to maintain structural integrity, particularly when E6011 is used in load-bearing applications.
welding aws e6011
Trustworthiness in utilizing AWS E6011 electrodes is upheld by adhering to best practices and recommendations laid out by manufacturing guidelines. Ensuring that the storage conditions prevent moisture absorption — which could lead to hydrogen-induced cracking — is a critical step in maintaining the electrode’s integrity and performance. Reliability also hinges on ongoing education and skill development for operators, ensuring that they remain informed about the latest techniques and safety protocols.
Moreover, testimonials from users in various sectors serve as a testament to the electrode's adaptability. Stories from welders repairing heavy machinery or restoring structural components in situ testify to the E6011's flexibility and rugged performance. Such real-world experiences not only validate the electrode's specifications but also build trust for new users considering it for challenging projects.
While E6011 might not always be the go-to choice for fine, intricate welds, its robustness and resilience make it an invaluable tool for rough, heavy-duty jobs where performance under challenging conditions is non-negotiable. It's a balance of expertise in handling and knowledge of application scenarios that empowers welders to optimize the use of E6011 electrodes to their full potential.
In conclusion, the AWS E6011 electrode embodies a blend of experience, expertise, authoritativeness, and trustworthiness, catering to the diverse needs of the welding industry. For those seeking a reliable solution in adverse conditions, its widespread acceptance and proven track record offer a compelling reason to incorporate this electrode into their toolkit.