Electrode selection is a pivotal part in achieving superior welding results. For experienced welders and newbies alike, understanding the nuances of electrode choices ensures not only optimal performance but also the safety and durability of the welded project. A deep dive into this technical yet critical aspect of welding unveils the key elements that any professional should consider when selecting the right electrode.
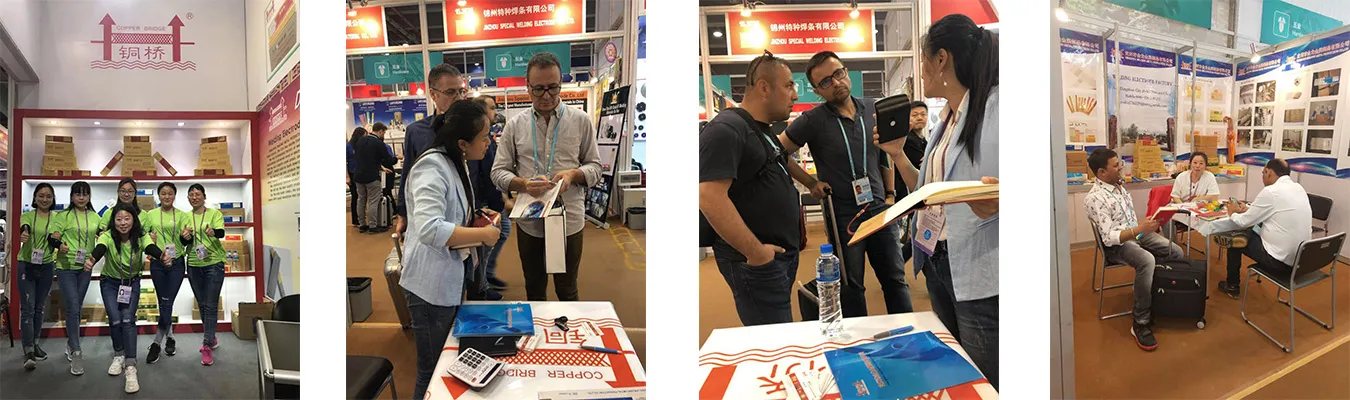
The core type of weld being undertaken greatly influences electrode choice. For shielded metal arc welding (SMAW), commonly referred to as stick welding, the consumable electrodes play a dual role. They serve as the filler metal and provide the arc shield. Choosing the right one, like E6010 or E7018, can drastically affect the weld’s tensile strength, penetration, and accommodation to positions. For instance, E6010 excels in vertical or overhead positions due to its deep penetration and fast-freeze characteristics, making it ideal for pipeline or structural work. In contrast, E7018 is favored for its smooth arc and versatility in working on both AC and DC currents, well-suited for tasks requiring high deposition rates.
Material compatibility cannot be overstated when selecting electrodes. The electrode must match the base metal to maintain integrity. For carbon steel, mild steel electrodes are typically sufficient, but stainless steel or other high alloy metals require specialized electrodes, such as those with chromium or nickel cores. These ensure corrosion resistance and maintain mechanical properties in harsh environments. This compatibility extends to the consideration of metallurgical properties, like yield strength and ductility, which are crucial for welds subjected to dynamic stresses.
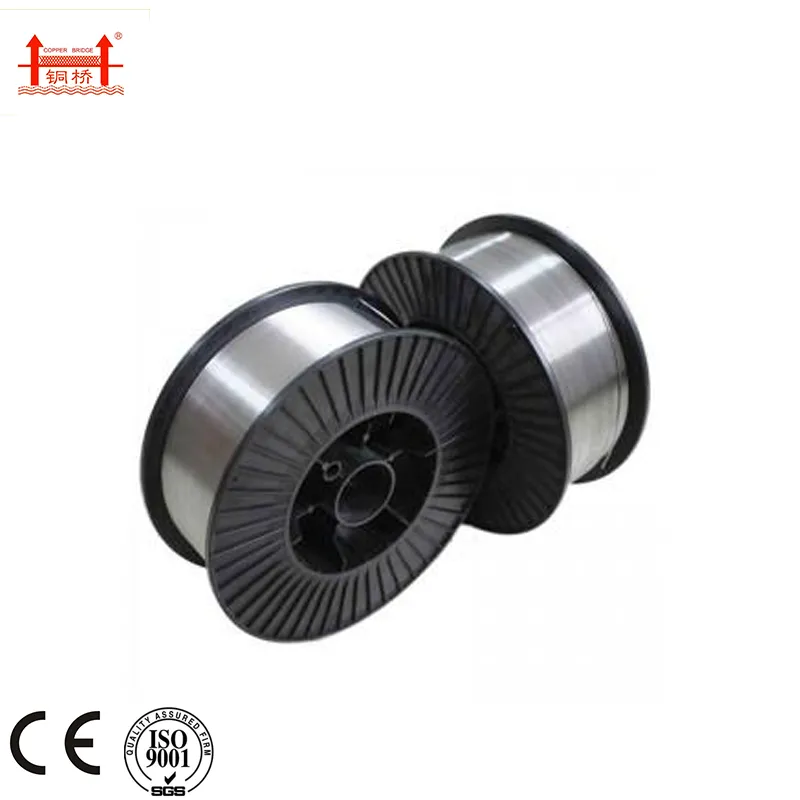
Thickness of the base material is another deciding factor. Thicker materials demand electrodes that provide deeper penetration, while thinner materials need rods that can maintain a stable arc without burn-through. Adjustable arc settings, incidentally, also play a role here, allowing fine-tuning of current to achieve the desired results without compromising the base metal.
selection of electrode in welding
The working environment strongly dictates electrode choice as well. Outdoor projects might expose welds to the elements, making cellulose-coated rods such as E6010 advantageous for their ability to withstand windy conditions without excessive spatter or slag. Conversely, in a controlled indoor environment where aesthetics matter, rutile-coated electrodes like E7014 can provide a cleaner finish.
Expertise in electrode selection extends beyond avoiding defects; it enhances performance. A mischosen electrode could lead to poor weld quality, increasing susceptibility to cracking or porosity. Therefore, professionals must evaluate electrodes’ characteristics, such as tensile strength, usability, and the specific welding position, to circumvent potential failures. This is where established guidelines from authoritative bodies, such as the American Welding Society, become vital resources in ensuring compliance and excellence.
Trust in electrode brands forms another layer of selection criteria. Renowned manufacturers subject their products to rigorous quality control, providing a guarantee of performance consistency. The market offers an extensive range of electrodes, each promising distinctive features; however, welding experts often rely on trusted brands, acknowledging their contributions to successful projects globally.
In conclusion, the right electrode selection is a fusion of material compatibility, environmental considerations, and product reliability. Skilled welders leverage these facets, drawing on experience and technical knowledge to enhance project outcomes. Mastery of electrode dynamics doesn't just come from academic understanding but also from hands-on application and continuous research, shaped by innovations within the welding sphere. As welding technology evolves, staying abreast of emerging electrode formulations will enable practitioners to push the boundaries of what's possible, guaranteeing not just competence but also craftsmanship in every weld produced.