Mastering the art of repairing cast iron structures requires both expertise and specific tools, and among those, the oxy-acetylene cast iron welding rod holds a place of prominence. Leveraging this tool not only demands technical knowledge but also a comprehensive understanding of metallurgical processes. This article discusses the advantages and technical specifics of using oxy-acetylene rods for cast iron welding, aiming to provide profound insights for professionals and enthusiasts in the welding industry.
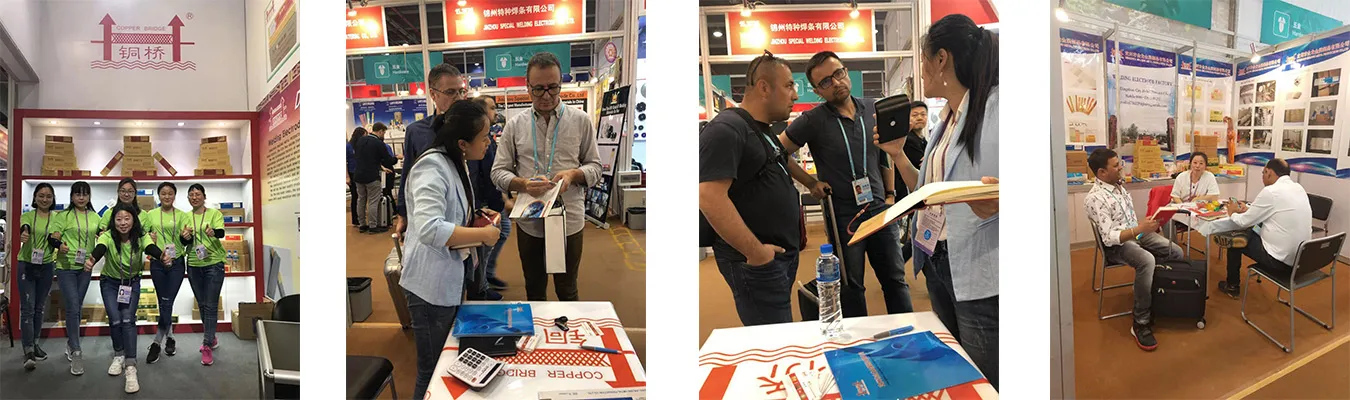
Oxy-acetylene welding, also known as gas welding, employs a flame produced by a mixture of oxygen and acetylene gas to melt the base metals. When it comes to cast iron, which is notoriously difficult to weld due to its high carbon content, an oxy-acetylene cast iron welding rod can be a game-changer. These rods are typically composed of a copper-bonded layer, enhancing the adhesion properties needed for effective cast iron recovery and repair.
The utilization of these specialized rods requires precise control and a keen eye for detail. Professionals in the field often emphasize the importance of preheating the cast iron component to avoid cracking. This step is crucial because cast iron has a tendency to expand and contract rapidly when subjected to sudden temperature changes. By uniformly heating the area to a moderate temperature, one can significantly minimize thermal stress, a key factor in preventing structural fractures.
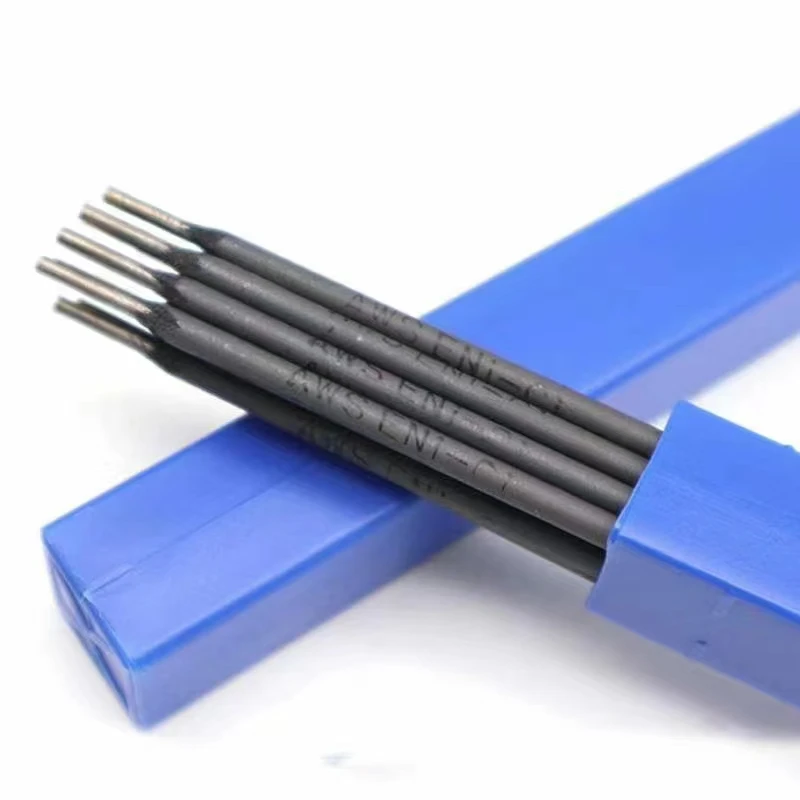
Another expert tip is to perform a slow cooling process post-welding to mitigate internal stress. The slow release of heat reduces the risk of brittleness and enhances the resilience of the weld. A controlled cooling environment, often achieved with thermal blankets, is essential to maintain the integrity of the weld. This method ensures that the molecular structure of the cast iron realigns properly, thereby increasing the durability of the repair.
oxy acetylene cast iron welding rod
Furthermore, the composition of the welding rod itself plays a critical role. Experienced welders tend to select rods with high nickel content when working with cast iron. This choice is due to nickel’s ability to absorb more carbon, which helps in reducing the brittleness common in standard cast iron welding practices. High-nickel content rods offer the flexibility and strength needed for a robust, long-lasting bond.
From a practical standpoint, mastering oxy-acetylene welding using these rods requires hands-on experience and knowledge of the material properties involved. Many welding experts advocate for obtaining certifications and undertaking continuous professional development to maintain high standards in workmanship. Being part of professional welding forums and communities also provides an invaluable resource for staying updated with the latest techniques and innovations in the field.
Moreover,
credibility in using oxy-acetylene cast iron welding rods also comes from understanding safety precautions. Proper handling of the acetylene torch and working in well-ventilated environments are critical to ensuring the safety of the welder and the surrounding area. The gasses involved are highly combustible, and adherence to safety protocols cannot be overstated.
In conclusion, the adept use of oxy-acetylene cast iron welding rods is a testament to a welder's expertise and understanding of both the science and art of metalwork. As advancements continue in welding technology, staying informed and exploring new techniques will solidify one's status as an authoritative and trustworthy figure in the industry. This dedication to excellence not only enhances the quality of individual work but also advances the craft of welding as a whole, setting higher standards and pushing the boundaries of what’s possible in metal repair and fabrication.