Welding, as an essential aspect of many industries, heavily relies on the quality of welding rods used in the process. Understanding the intricacies of an ordinary welding rod can significantly impact the efficiency and strength of welding projects. Whether you're an industry veteran or new to welding, knowing more about these fundamental tools can increase your project's success rate and ensure a high-level finish.
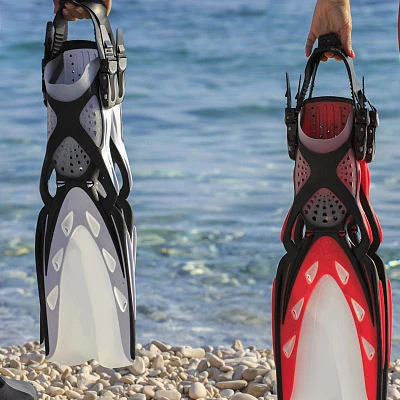
An ordinary welding rod, often referred to as a filler rod, plays a crucial role in connecting metal pieces through the application of heat. Depending on the composition and coating of the rod, it can influence the weld's penetration, strength, and finish quality. This is exactly why selecting the right welding rod is paramount for any project.
Working with welding rods is about understanding the interaction between the rod material and the base metals. Typically, welding rods are made from materials like mild steel, stainless steel, cast iron, or aluminum. Each type of material brings unique properties to the table. For example, mild steel rods are commonly used due to their versatility, while stainless steel rods offer excellent corrosion resistance, making them ideal for projects exposed to the elements.
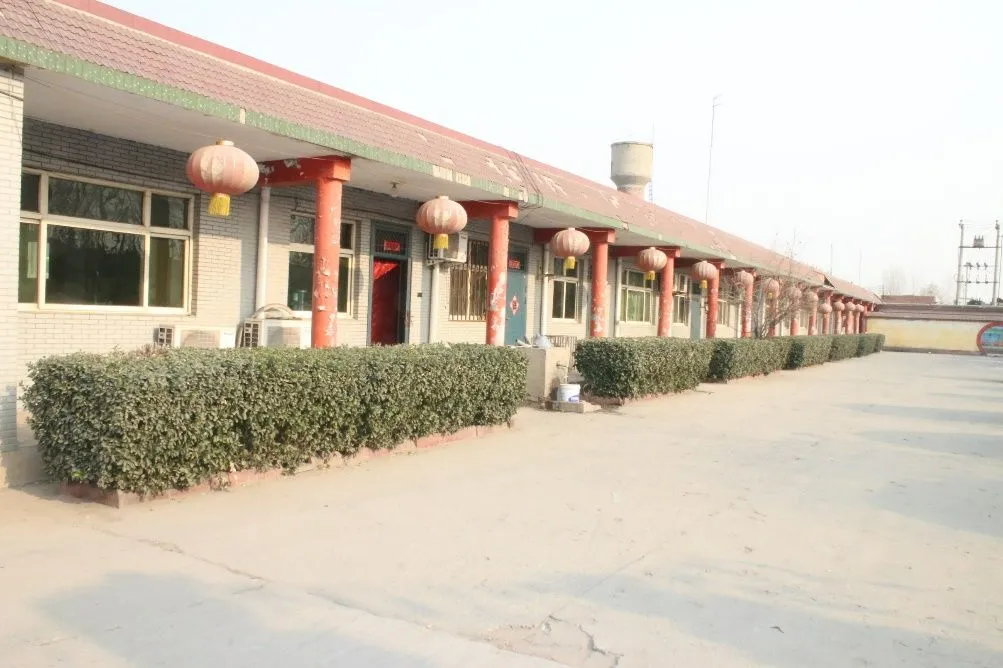
Coating on an ordinary welding rod can range from cellulose to mineral-based coatings and even flux coatings. A cellulose-coated rod provides a deep penetrating arc, which is suitable for vertical down welding. On the other hand, a mineral-coated rod may be used for a clean finish, shielding the molten pool from impurities in the air.
When it comes to nuances in application, the diameter of an ordinary welding rod determines the depth and width of the weld. Smaller diameters allow for greater control, whereas larger rods can handle heavier welds. The choice of rod diameter should align with the thickness of the metal being welded and the position in which welding takes place.
A key aspect of selecting welding rods is also understanding the amperage range needed for various rods. Each rod will function optimally within a specific amperage range. Using the incorrect amperage can cause poor penetration or excessive spatters, compromising the weld quality.
ordinary welding rod
Real-world experience underlines the importance of selecting the correct welding rod. For instance, a fabrication company faced issues with brittle welds using regular mild steel rods on high-stress applications. The solution was to switch to low-hydrogen welding rods, which dramatically increased the durability and performance of the welds by reducing the hydrogen content that can cause cracking.
Moreover, understanding how welding rods are stored and maintained can affect their longevity and performance. Ordinary welding rods should be stored in a dry and cool environment to prevent moisture absorption, which could potentially lead to weld defects like porosity. Investing in proper storage facilities shows professionalism and concern for product quality, boosting client confidence.
Providing safety during welding operations is an aspect where the choice of welding rod also plays a role. Some rods emit hazardous fumes and require appropriate ventilation and protective equipment during use. Understanding these safety implications showcases expertise in handling welding equipment, ensuring safe and efficient project execution.
Conclusively, the expertise and experience associated with welding rods transcends basic knowledge. It's about leveraging the intricate details of rod selection, application techniques, and safety precautions to execute superior welding projects. Industry professionals should not underestimate the role of ordinary welding rods, as they can be pivotal in ensuring project success and maintaining the integrity of metal structures.
Choosing the right welding rod requires not just technical know-how but also a consideration of the environmental conditions and specific project demands. This extensive understanding leads to authoritative project outcomes and fosters trust with clients who rely on high-quality, durable metal fabrications.