Nickel 99 TIG welding rods are among the most sought-after tools in the welding industry, particularly for those dealing with specialized applications involving cast iron. As an expert in the field, it’s essential to appreciate the unique properties that make Nickel 99 rods an indispensable asset for welders seeking durability and precision.
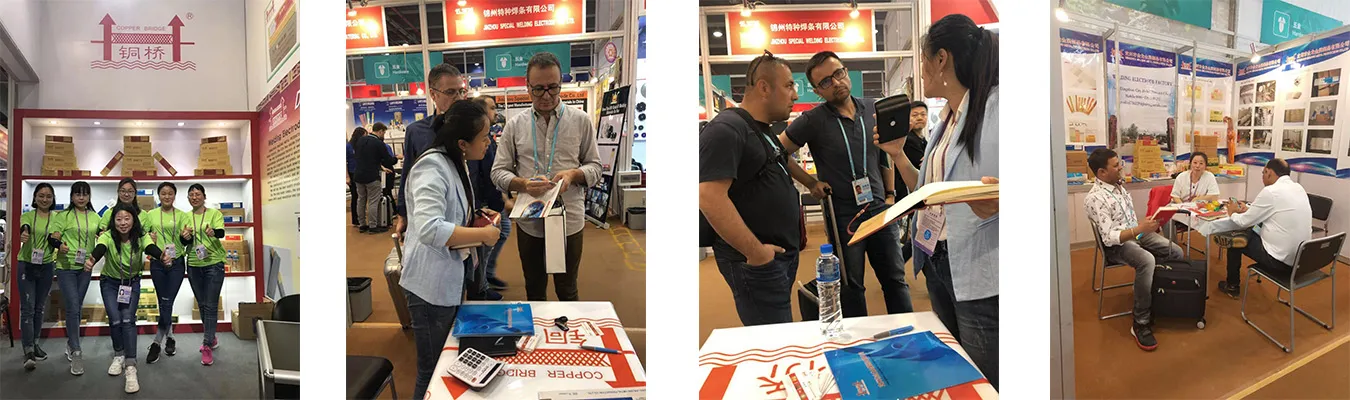
The allure of Nickel 99 stems from its exceptional compatibility with cast iron. Cast iron, notoriously known for its brittleness and susceptibility to cracking, requires a filler metal that can accommodate its unique properties. Nickel 99 rods, with their high nickel content, offer the ideal solution. They provide a soft and malleable weld that effectively absorbs the stress and prevents the typical cracking problems associated with cast iron welding.
From a professional perspective, employing Nickel 99 TIG rods ensures a seamless welding process. These rods are specifically formulated to create strong, machinable joints that can withstand substantial mechanical stress. The high nickel concentration, usually around 99%, allows for a weld that maintains its integrity even under vibration, thermal expansion, and contraction. This makes them particularly valuable in industries where mechanical components are subject to continuous motion and temperature fluctuations.
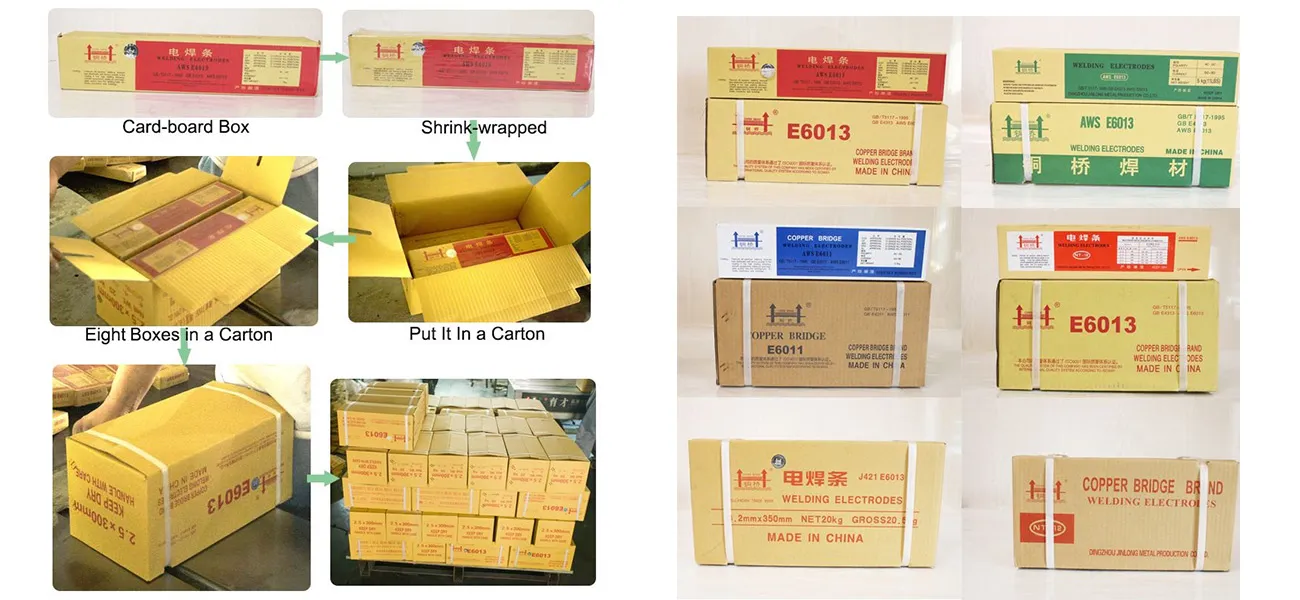
When it comes to technical specifications, Nickel 99 rods are engineered to deliver a stable arc, which is crucial for precise welds. The stability of the arc allows for better control over the heat input, reducing the risk of widening the heat-affected zone—a common issue that can compromise the structural properties of the base material. Additionally, the welds produced are highly resistant to corrosion, extending the lifespan of the welded structure significantly.
In practice,
the efficiency of Nickel 99 TIG welding rods is evident during the post-welding phase. The machinability of the welds facilitates any finishing touches, such as grinding or drilling, without the complications that often arise with other filler metals. This attribute is especially critical in automotive and construction industries where exact specifications and finishes are paramount.
nickel 99 tig welding rod
Experts in metallurgy acknowledge the adaptability of Nickel 99 TIG rods across varied applications. For instance, they are irreplaceable in repairing engine blocks and exhaust manifolds. The high compatibility with different forms of cast iron, including gray, malleable, and ductile iron, showcases their versatility. Furthermore, these rods serve as a robust solution for joining cast iron to dissimilar metals like steel and stainless steel, broadening their utility in composite structures.
Reliable sources within the sector attest to the cost-effectiveness of Nickel 99 rods in the long run. While the upfront costs might be higher compared to other filler metals, the reduced need for repairs and maintenance of the welds offsets initial expenditures. The integrity and durability of the welds decrease downtime and increase productivity, which is a critical factor for operational efficiency in manufacturing and repair services.
Finally, the credibility of Nickel 99 rods is well-supported by comprehensive research and industry standards. These rods adhere to stringent quality controls, ensuring consistency in performance across diverse working conditions. Leading manufacturers provide certification and technical support, reflecting the trust that professionals place in these products for precision welding tasks.
In summary, Nickel 99 TIG welding rods are a cornerstone for professionals dealing with cast iron welding. Their superior properties ensure strong, durable, and corrosion-resistant welds that meet the high demands of industrial applications. Whether in automotive repair, construction, or metallurgy, these rods provide a reliable, efficient, and cost-effective solution that enhances the overall quality and longevity of welded structures. The unmatched expertise and credibility inherent in the use of Nickel 99 continue to solidify its standing as an authoritative choice in the realm of specialized welding.