Nickel 99 TIG rods have emerged as a vital component in the toolkit of welding professionals dealing with various challenging applications, particularly in the repair and joining of cast iron. The unique composition and properties of this welding rod ensure superior performance, making it indispensable for projects requiring strength, durability, and resilience.
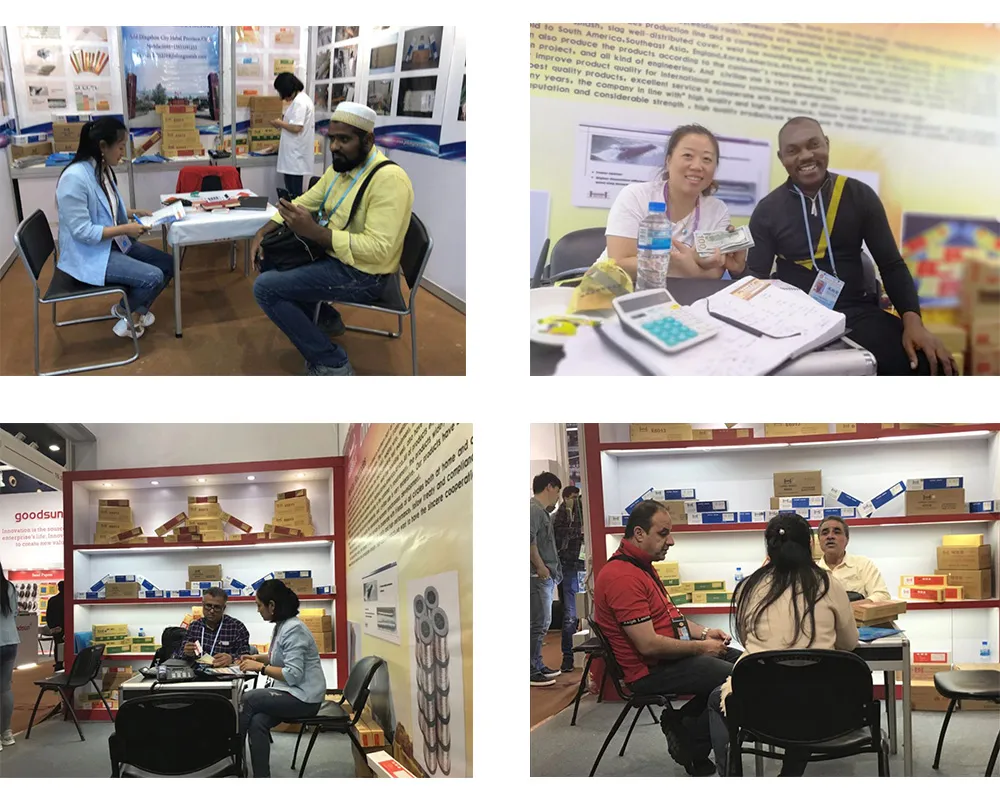
Boasting a composition predominantly made up of nickel, typically at 99%, these TIG rods offer unparalleled compatibility with a wide array of metals, with a special affinity for cast iron. The high nickel content is primarily responsible for its ability to mitigate the inherent brittleness of the base metal, reducing the risk of fractures.
One of the critical factors driving the demand for Nickel 99 TIG rods is their exceptional adaptability. In the welding community, cast iron is notoriously difficult to work with, primarily due to its high carbon content, making it prone to cracking when subjected to thermal stress. However, the Nickel 99 rod significantly reduces these risks, as the nickel complements the microstructure of cast iron, allowing the welded joint to absorb thermal expansion without succumbing to stress.
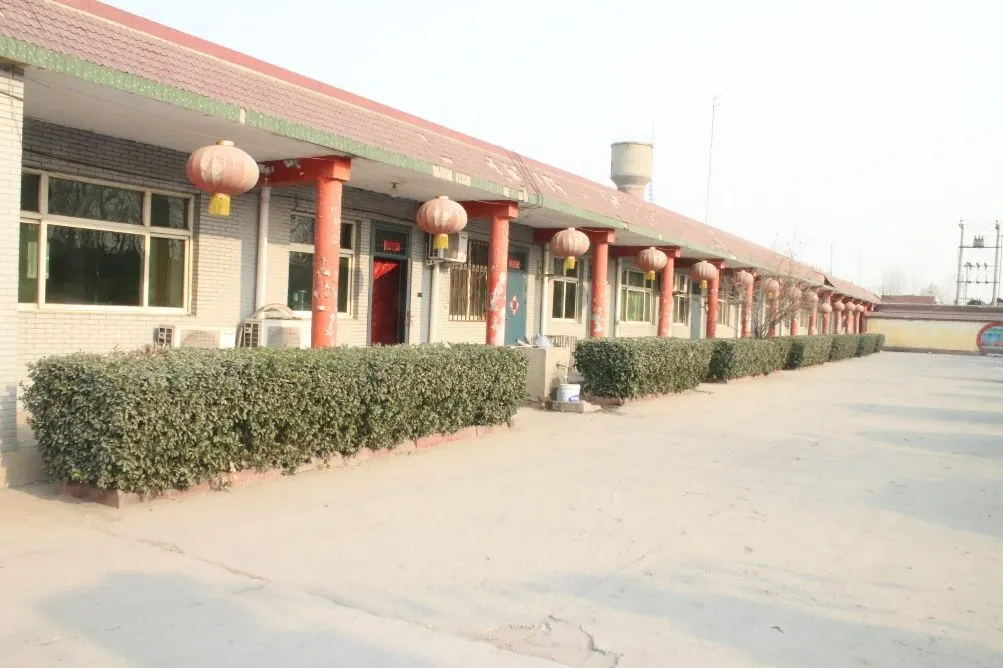
An expert welder knows that using this particular rod improves not only the mechanical properties of the joint but also its aesthetics. The bead produced is smooth and refined, decreasing the need for extensive post-weld processing, which in turn mitigates labor costs. For industries such as automotive or heavy machinery, where the longevity and appearance of the weld are paramount, Nickel 99 TIG rods offer an ideal solution.
Furthermore, these rods exhibit impressive corrosion resistance, a necessary attribute for components exposed to harsh environments, such as exhaust systems or marine applications. This resistance ensures that the integrity of the weld is maintained over time, significantly extending the service life of the components, which is a decisive factor for end-users aiming to minimize maintenance expenditures.
nickel 99 tig rod
From a technical standpoint,
using Nickel 99 TIG rods requires a certain level of expertise. Proper preheating of the base material often plays a crucial role before welding to prevent thermal shock and ensure optimal fusion. Additionally, controlled cooling is integral to maintaining the ductility of the joint, often necessitating the use of thermal blankets or slow air cooling methods.
For practitioners in the field, selecting Nickel 99 rods is often dictated by the nature of repair work. Historic building restorations and the maintenance of classic vehicles are among the popular applications. Here, preserving the original structure’s integrity and appearance is critical, and these rods rise to the occasion by facilitating unobtrusive, durable repairs which blend seamlessly with existing materials.
Considering their authoritative standing in the industry, these rods are often recommended by seasoned professionals and industry bodies for specific repair tasks. Their proven track record endows them with a trust factor that few alternatives can match, resulting in consistent repeat use by operators who demand precision and reliability.
In terms of trustworthiness, manufacturers often conduct rigorous testing to ensure each batch meets specific mechanical properties and performance criteria before reaching the market. This quality assurance inspires confidence among users, who rely on these rods to meet demanding welding challenges.
In conclusion, Nickel 99 TIG rods are not merely a choice but a necessity for welding professionals focused on quality and long-term results. Through a combination of high nickel content, adaptability to tough working conditions, and proven industry standing, these rods provide a compelling proposition for achieving superior welding outcomes. As demands for specialized repairs and restorations grow, the importance of using the right materials cannot be overstated, and Nickel 99 TIG rods stand at the forefront as a testament to innovation and reliability in the world of metalworking.