In the world of metal fabrication, selecting the right welding electrode is crucial for the efficiency and quality of a project. Specifically, when dealing with materials such as mild steel (MS) and stainless steel (SS), the decision becomes even more critical due to the unique properties each metal possesses. Welding electrodes are pivotal in determining the integrity and strength of the weld, impacting the longevity and safety of the resulting structure.
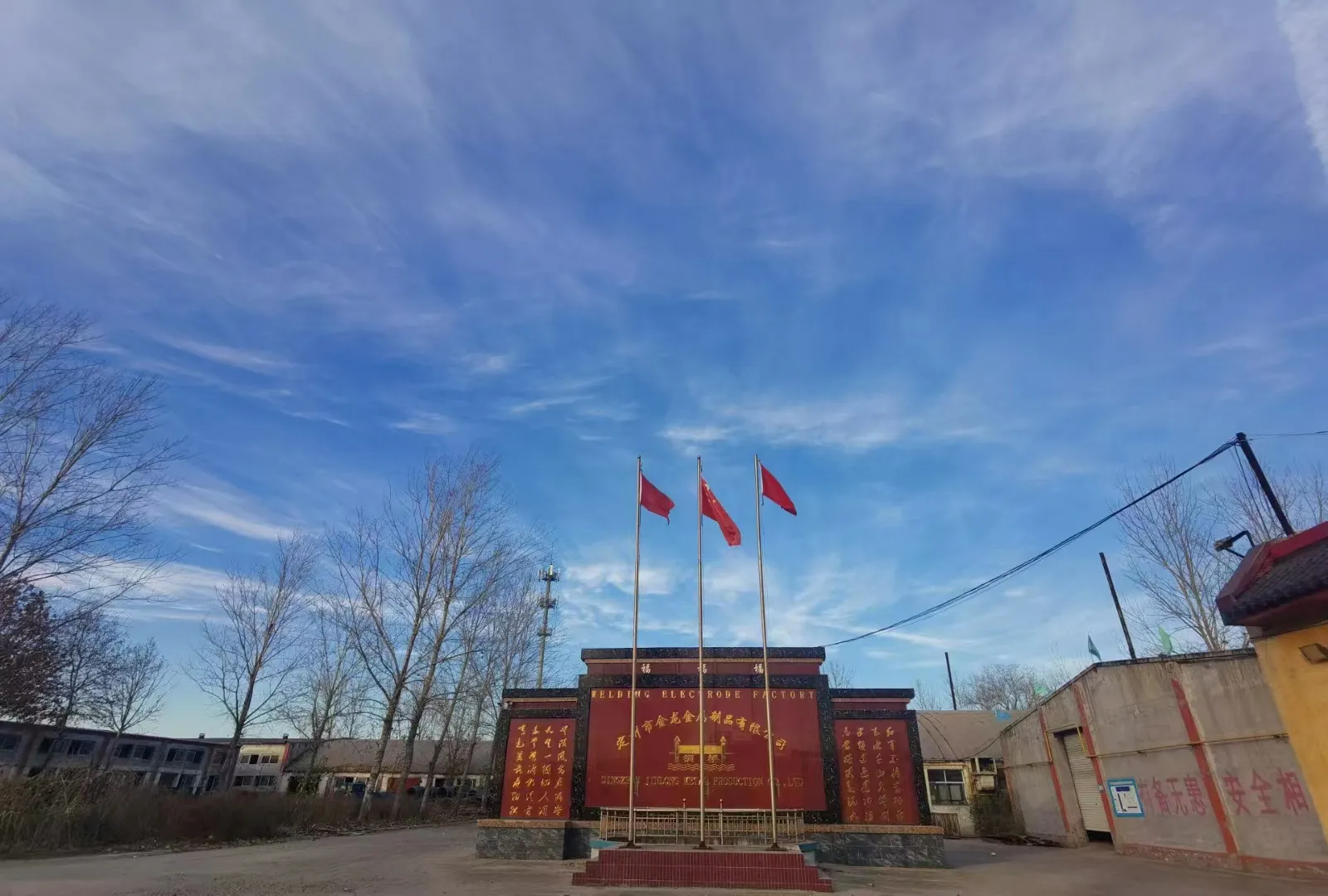
The MS to SS welding electrode serves as a bridge between two vastly different materials, each with their own characteristics mild steel, known for its ductility and malleability, and stainless steel, revered for its corrosion resistance and strength. The choice of electrode must accommodate these properties to ensure a seamless and durable bond.
Experience in welding these materials reveals that the compatibility of thermal expansion rates, tensile strength, and chemical compositions must be meticulously addressed.
A favorite among seasoned welders is the use of austenitic stainless steel electrodes. Due to their excellent fusion capabilities, they mitigate the issues of thermal stress and corrosion at the weld joint. Especially, the E309L electrode is renowned for its capacity to join MS to SS effectively, offering a low carbon content that minimizes carbide precipitation and, hence, enhances corrosion resistance.
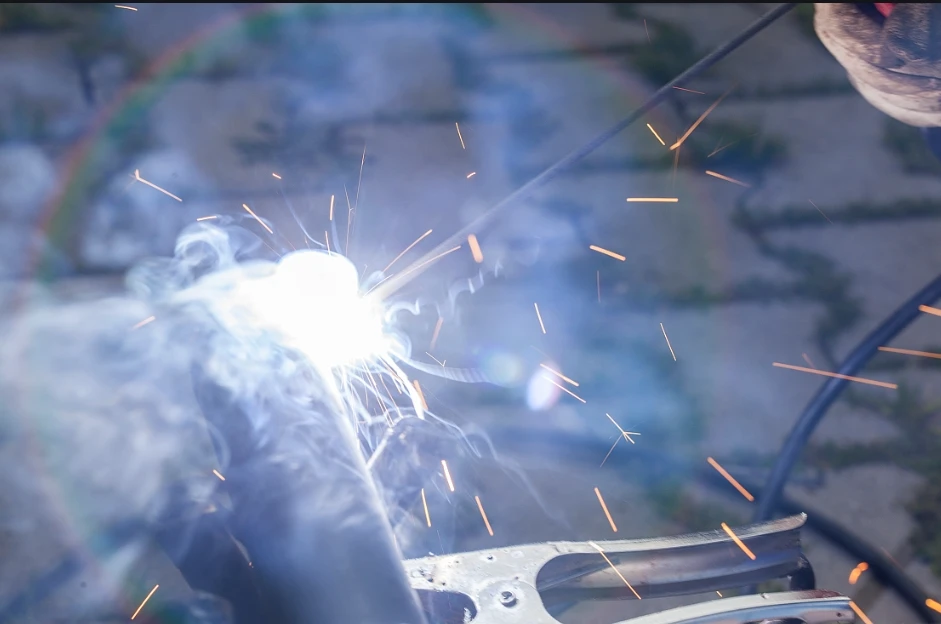
The expertise involved in using these electrodes goes beyond just selection; it extends into the realm of technique. The amperage settings, welding speed, and electrode angle need precision adjustments to accommodate the differential in melting points and heat conductivity between mild steel and stainless steel. Proper preheating of mild steel and controlling the interpass temperature when welding can prevent common issues such as heat affected zone (HAZ) cracking and distortion.
Authoritativeness in this arena is often exemplified by adhering to recognized standards such as those set by the American Welding Society (AWS). Compliance with these standards in electrode selection and usage practices not only ensures structural integrity but also aligns with safety protocols critical for industrial projects. Certifications and documented performance evaluations of specific electrodes, such as E309L, form a compelling basis for their recommended use.
ms to ss welding electrode
Trustworthiness, equally significant, is derived from the traceability and quality assurance of the welding electrodes used. Ensuring that the electrodes are sourced from reputable manufacturers with ISO certification assures consistent performance and adherence to required specifications. Furthermore, tracking the batch numbers and understanding manufacturer guidelines on shelf life and storage conditions preserve the electrodes' integrity, thus guaranteeing optimal results when applied.
Practically, using an MS to SS welding electrode requires welders to conduct test welds to calibrate their settings according to the specifics of the task at hand. This trial phase is crucial for adjusting to environmental conditions such as humidity and ambient temperature, which may affect the welding procedure.
Feedback from operational case studies also proves invaluable, as firsthand accounts from industries such as petrochemicals, automotive manufacturing, and construction illuminate best practices and cautionary tales. These insights fortify the knowledge base, leading to enhanced decision-making and innovation in electrode application strategies.
In summary, the strategic selection and application of MS to SS welding electrodes impact not only the project's immediate success but also the long-term resilience of the welded structure. Real-world experience, technical expertise, adherence to authoritative guidelines, and the reliance on trustworthy manufacturing practices collectively define the proficiency required in leveraging these welding electrodes. Such thoroughness ensures that the final welds not only meet but exceed industry standards, paving the way for robust and enduring constructions.