MS to CI welding electrodes represent a critical aspect of modern industrial fabrication processes. These electrodes, designed to efficiently join mild steel (MS) to cast iron (CI), offer unique challenges and solutions that merit careful consideration. As industries increasingly demand durable and reliable welding techniques, understanding the properties and applications of MS to CI electrodes becomes essential for fabricators and engineers globally.
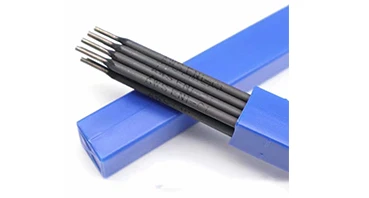
When it comes to welding mild steel to cast iron, the disparity in properties between the two metals poses significant challenges. Mild steel, known for its ductility and relatively low carbon content, contrasts sharply with the high carbon content and brittleness inherent in cast iron. This inherent difference requires specialized electrodes capable of mitigating potential issues such as cracking and weak bonding.
A key feature of MS to CI welding electrodes is their ability to produce a weld joint that accommodates the metallurgical differences between mild steel and cast iron. These electrodes are typically coated with specific flux compositions that stabilize the arc, reduce porosity, and enhance the tensile strength of the weld. By facilitating a smooth transition between the two metals, these electrodes help prevent the common issue of cracking in the heat-affected zone.
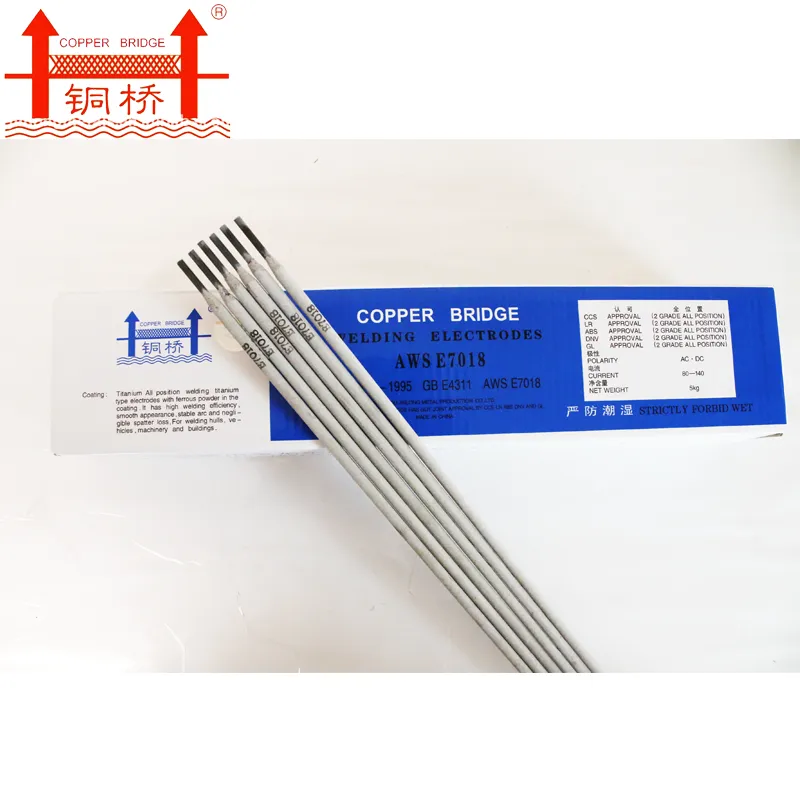
The selection of the appropriate welding electrode depends on several critical factors. One of the primary considerations is the specific application and the characteristics of the cast iron involved. For instance, grey cast iron, white cast iron, and ductile iron each present distinct challenges and require adapted approaches. MS to CI electrodes are often formulated with nickel or copper-based alloys, which not only improve flexibility and strength but also aid in reducing residual stresses in the weld area.
In terms of technique, achieving successful welds between mild steel and cast iron hinges on careful preparation and execution. Preheating the cast iron is generally recommended to minimize the risk of thermal shock and stress concentration, conditions that can lead to cracking. Post-weld heat treatment is another recommended practice to gradually relieve stresses introduced during welding, ensuring a more stable bond.
ms to ci welding electrode
Safety and reliability are paramount in welding processes, particularly when handling materials with disparate physical properties. Professional welders must ensure that their equipment is properly calibrated and that safety protocols are diligently followed. The use of protective gear, proper ventilation, and adherence to recommended operating procedures enhance the trustworthiness of the welding process and the longevity of the welds.
The application of MS to CI welding electrodes extends across various sectors, from automotive manufacturing to structural engineering. In the automotive industry, for example, these electrodes are often used to repair cast iron engine blocks and other critical components, a testament to their versatility and reliability. In construction, they are employed to join structural components, where durability is paramount.
Authoritative expertise in the use of MS to CI welding electrodes not only involves mastering the technical aspects of welding but also understanding the implications of each material's reaction to heat and stress. Professionals must balance theoretical knowledge with empirical experience, constantly adapting to advancements in welding technology and material sciences.
To cultivate expertise in this field, continuous education and hands-on training are crucial. Keeping abreast of new developments, such as improved electrode coatings and advanced welding techniques, ensures that professionals remain at the forefront of industry standards. Certification programs and technical workshops offer valuable opportunities for welders to hone their skills and expand their knowledge base.
In conclusion, MS to CI welding electrodes play an instrumental role in bridging the gap between two inherently different materials, providing robust solutions to complex industrial challenges. By combining expert knowledge with practical experience, welding professionals can optimize their use of these electrodes, contributing to safer, stronger, and more reliable metal fabrications. As industries continue to evolve, the continuous refinement and innovation in welding electrodes ensure that they meet the growing demands for quality and performance.