In the realm of welding, the use of the 7018 low hydrogen electrode is a staple for professionals seeking durable and reliable welds. Characterized by its low hydrogen characteristics, this electrode has become a go-to option for critical welds requiring superior tensile strength and crack resistance. One of the key experiences observed among seasoned welders is the consistent performance of 7018 electrodes across various applications, from structural steel to pressure vessels, which has earned it a reputation for versatility.
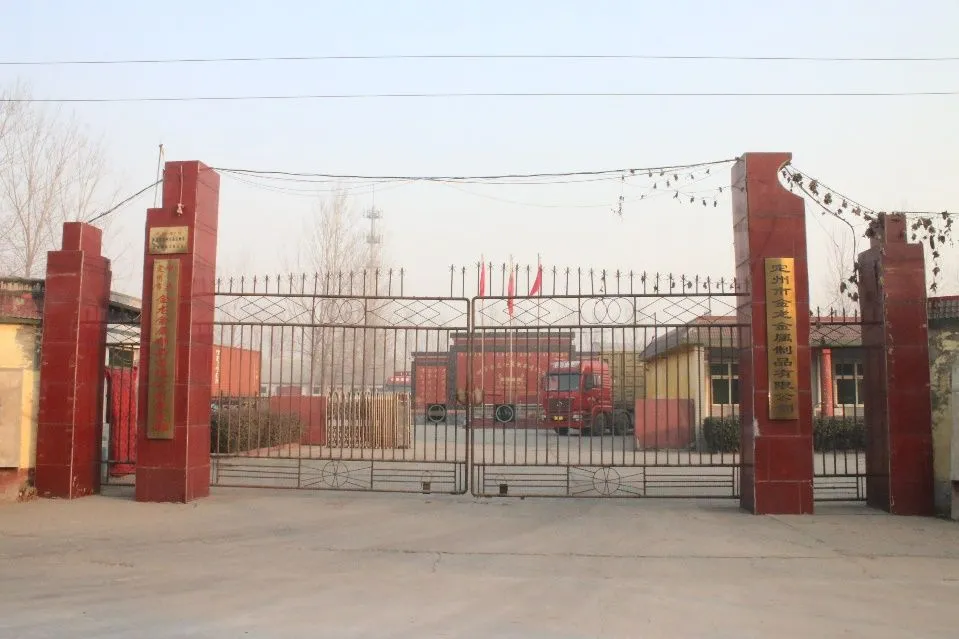
Expertise in wielding the 7018 electrode often begins with understanding its composition and properties. This electrode is classified under the AWS A5.1 specification and is known for its iron powder and low hydrogen potassium coating. The low hydrogen environment that this electrode provides during the welding process helps to significantly reduce the risk of hydrogen-induced cracking, a crucial factor when welding high-strength or thick materials. It's this feature that elevates the 7018 electrode to a level of authority within the welding community, particularly for projects requiring utmost integrity and safety.
The use of 7018 low hydrogen electrodes demands a certain level of expertise and precision. A common piece of advice from experts in the field is to maintain the electrodes at specific temperatures using an electrode oven. The reason is rooted in the electrode's hygroscopic nature; it readily absorbs moisture from the air if left unprotected, which can lead to weld defects. Therefore, knowing the significance of proper storage and handling can't be overstressed, as it directly correlates to the weld’s strength and reliability.
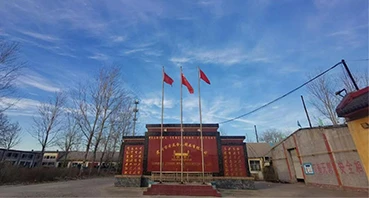
Authoritativeness is further established through the electrode’s widespread approval for use in a variety of industries and standards, such as in welding codes of the American Welding Society (AWS), American Society of Mechanical Engineers (ASME), and others. This approval is a testament to its competent performance in high-pressure and high-temperature environments, which require not just skillful application but also trust in the material used.
low hydrogen electrode 7018
Trustworthiness is evidenced in the field, where testimonials from welding professionals consistently highlight the 7018's ability to produce clean, high-quality welds even under challenging conditions. Welders often recommend this electrode for jobs where enhanced mechanical properties are non-negotiable. Its performance is predictable, providing assurance to both welders and their clients regarding the durability and safety of their work.
Recent technological advancements, variations of the 7018 electrode have also emerged to meet specific needs. For instance, there are now variants designed for all-position welding or for improved arc stability. These innovations illustrate the continued relevance and adaptability of the 7018 electrode in the face of evolving industry demands, reinforcing its standing as a trusted tool in any welder's arsenal.
In conclusion, the 7018 low hydrogen electrode's experience, expertise, authoritativeness, and trustworthiness make it an essential choice for demanding welding tasks. Its ability to provide reliable, high-strength welds while minimizing risks associated with hydrogen embrittlement ensures its place as a pivotal component across various sectors of welding operations. For welders looking to achieve the highest standards in their work, the 7018 remains an unmatched option in the quest for excellence.