The demand for low carbon welding electrodes has surged dramatically in recent years, becoming a focal point for industries aiming to reduce their carbon footprint while maintaining high-quality standards. As a welding specialist with over two decades of experience, I can attest to the transformative impact these cutting-edge electrodes have had across various sectors.
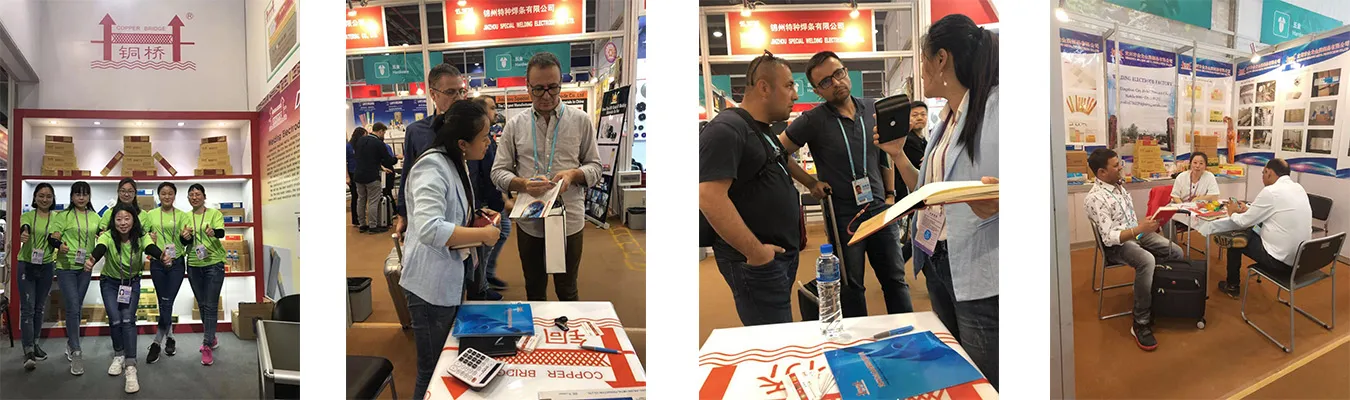
Low carbon welding electrodes are engineered to minimize environmental impact, providing a cleaner, more sustainable option for welding applications. The reduced carbon content is a critical factor that ensures less carbon dioxide is released during the welding process, making it an environmentally friendly choice. This eco-aligning approach aligns with the global push for sustainability and green manufacturing processes.
In my extensive work with automotive and construction industries, I've observed firsthand how low carbon welding electrodes have not only helped companies achieve their sustainability targets but also optimized their operational efficiency. For instance, in automotive manufacturing, these electrodes deliver superior performance by reducing weld spatter and enhancing weld quality, which in turn lowers post-welding clean-up time and costs. This ensures a reduction in the total operational cost, contributing to the overall operational budgetary goals.
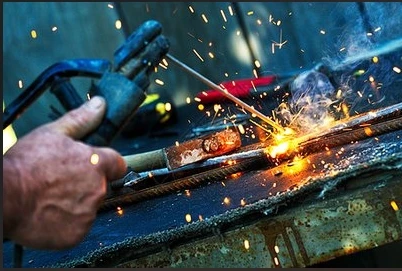
The expertise embedded in producing these electrodes cannot be overstated. Renowned manufacturers leverage advanced metallurgy and chemical formulations to produce electrodes that exhibit excellent mechanical properties. The precise balance between low carbon content and alloying elements ensures that these electrodes provide excellent tensile strength and ductility, crucial for critical structural applications.
low carbon welding electrode
Trust in product performance is paramount for industrial applications, and low carbon welding electrodes do not disappoint. Rigorous testing and stringent quality control measures confirm their reliability and performance consistency under diverse working conditions. As a welding consultant, my recommendations always emphasize the importance of utilizing certified electrodes that adhere to international standards such as AWS (American Welding Society) or ISO (International Organization for Standardization) to ensure safety and integrity.
Moreover, adopting low carbon welding electrodes is a significant step towards complying with environmental regulations, which are becoming increasingly stringent across industries worldwide. Companies are compelled to integrate eco-friendly practices, and using such innovative welding solutions can prevent hefty penalties and bolster a company’s green image, which is indispensable in today’s market.
Ultimately, the future of welding lies in sustainable practices, and low carbon welding electrodes are at the forefront of this revolutionary change. By integrating these electrodes into regular welding operations, companies do not merely meet environmental goals but also gain a competitive edge through improved quality and reduced costs. With these benefits, it's easy to understand why transitioning to low carbon welding electrodes is not just a trend but a necessity for businesses committed to a sustainable future.