Revolutionizing the modern welding industry, iron arc welding has become an indispensable tool in metal fabrication and construction. This advanced welding technique is acclaimed for its accuracy, strength, and versatility, making it a top choice for welding professionals across various sectors. As someone deeply entrenched in the field of welding and metal fabrication, I've seen firsthand the profound impact iron arc welding has had, invigorating industries with more efficient production and durable product outcomes.
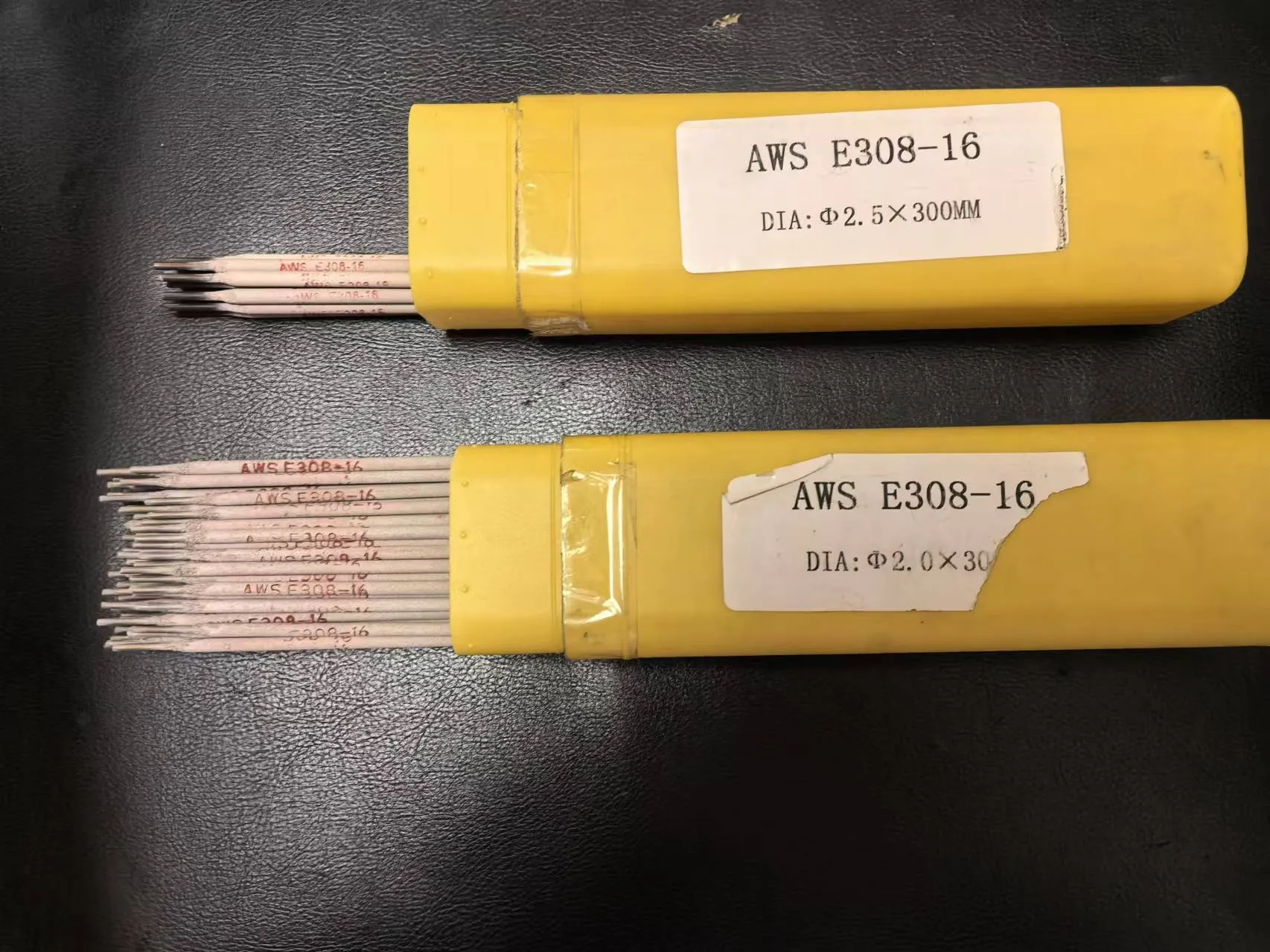
Iron arc welding involves the use of consumable electrodes to create exceptional bonds between metal components. This method utilizes the benefits of both AC and DC currents, typically depending on the specific requirements of the project. One of the notable advantages of iron arc welding is its compatibility with thick metals, including all grades of steel and iron, allowing for robust fabrication.
With over two decades of expertise in welding, observing the transformation from traditional techniques to modern, sophisticated methodologies like iron arc welding has been enlightening. The core strength of iron arc welding lies in its ability to produce high-quality welds consistently. It's especially beneficial where structural integrity and durability are paramount, such as in the construction of bridges, skyscrapers, and heavy machinery. The precision achieved with iron arc welding minimizes the risks of post-weld failures, crucial for high-stakes projects.
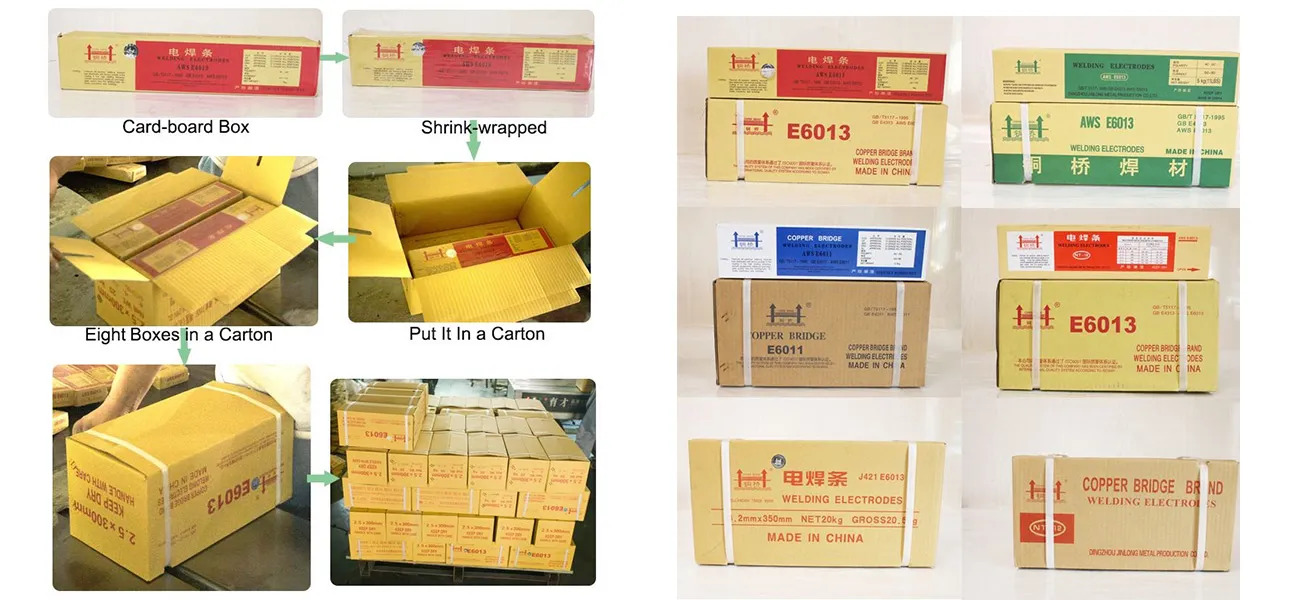
To establish a credible presence in the market, it's essential to understand the intricate details of iron arc welding. You'll need a profound comprehension of variables such as electrode selection, current control, and heat adjustment. Each of these factors can significantly affect the quality and resilience of the weld. For instance, choosing the correct type of electrode—whether it's rutile, basic, or cellulose—will determine the weld's penetration and overall performance.
Iron arc welding also offers remarkable versatility when it comes to the types of joints that can be formed, including butt, lap, and corner joints. This flexibility enables welders to adapt to diverse project requirements without necessitating a change in methodology or tools. Different positions, such as flat, horizontal, vertical, and overhead, are easily managed with iron arc welding, offering unparalleled adaptability.
iron arc welding
Safety, a pivotal concern within the welding industry, is effectively managed with iron arc welding. Modern equipment incorporates advanced safety features, such as voltage regulators and thermal overload protection, ensuring that operators are shielded from potential hazards. The relatively low fume emissions compared to other welding methods also minimize respiratory risks, contributing to a healthier working environment.
Trustworthiness in iron arc welding comes from its track record of success in critical applications and its endorsement by leading industry bodies. Standards set by organizations like the American Welding Society (AWS) and the International Organization for Standardization (ISO) provide guidelines that assure quality and safety, promoting widespread adoption of iron arc welding in demanding industries.
The adoption of iron arc welding is further bolstered by continuous innovations in equipment and techniques. Advances in automation and computer-controlled welding systems have increased precision whilst reducing the likelihood of human error. Such developments make iron arc welding an attractive option for manufacturers looking to optimize production lines and achieve consistent, high-quality results.
Emphasizing continuous training and development for welders ensures the highest standards of expertise are met. Understanding the nuances of operating modern iron arc welding equipment, assessing project requirements accurately, and adhering to safety protocols are imperative for maintaining a superior standard of workmanship.
In conclusion, iron arc welding stands as a pillar of modern metal fabrication, defined by its excellence in delivering strong, reliable welds. Its understanding and mastery elevate a welding professional's capability to produce superior outcomes, safeguard structural integrity, and drive the industry's evolution forward. As industries demand ever-higher standards of production and durability, professionals equipped with the knowledge and skills in iron arc welding sit at the forefront of innovation and quality assurance.