The use of the 7018 welding rod is an essential skill for anyone serious about welding, whether you're an amateur enthusiast or a seasoned professional. Known for its versatility and strength, the 7018 welding rod is highly regarded in the welding community for its ability to produce clean and robust welds, particularly in structural steel applications. This article delves into the nuances of the 7018 welding rod, offering insights grounded in experience and expertise that will enhance your welding projects significantly.
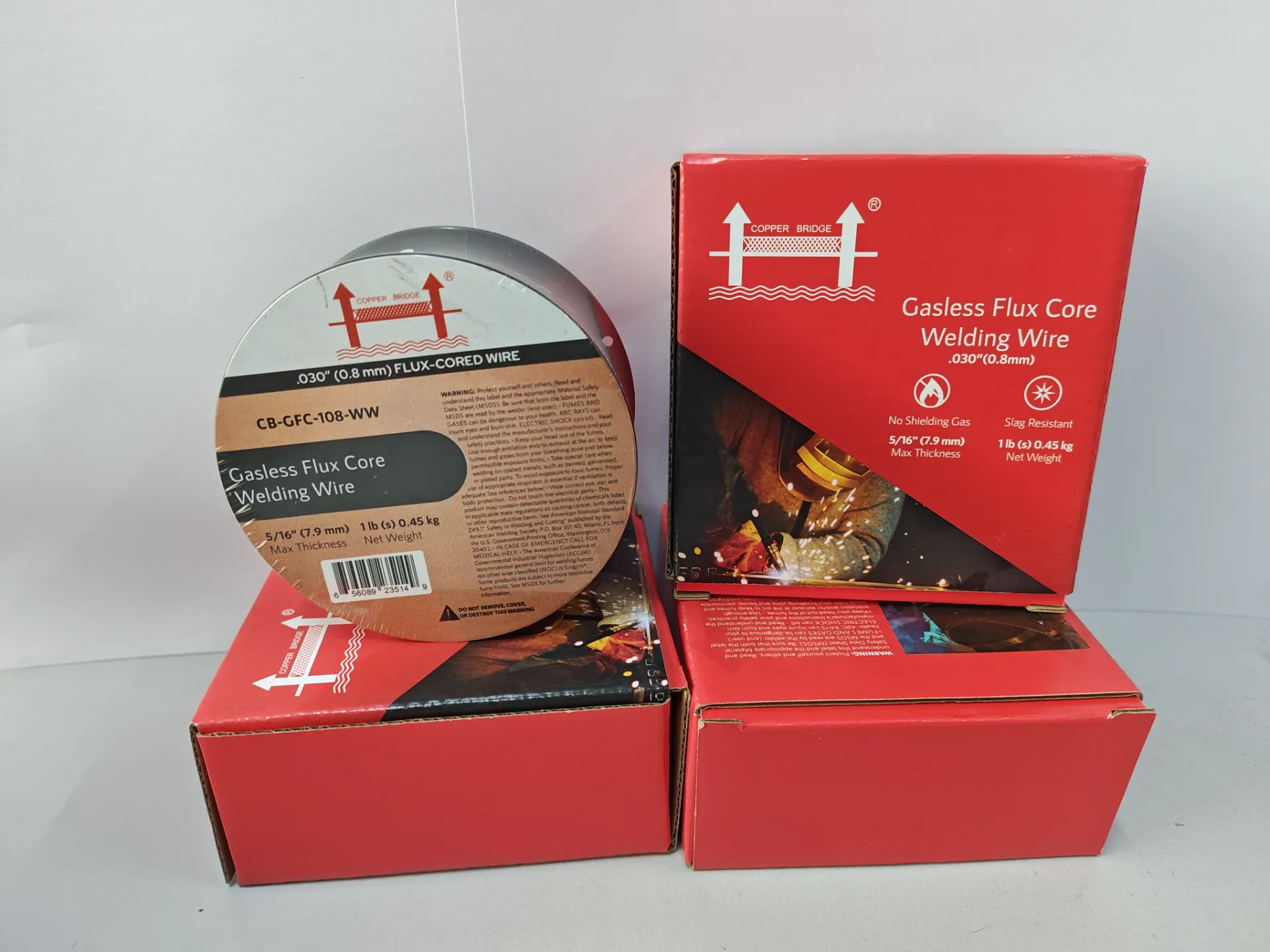
To begin with, the 7018 is a low-hydrogen, all-position electrode, making it ideal for welding carbon steel and similar metals. Its designation specifies its tensile strength and usability the “70” indicates a tensile strength of 70,000 psi, while the “1” denotes its suitability for all welding positions, including flat, horizontal, vertical, and overhead. The “8” refers to the characteristics of the flux coating, which contributes to the weld’s smooth finish and minimal spatter.
One of the standout features of the 7018 rod is its low hydrogen content. This characteristic is critical because excessive hydrogen can lead to weld cracking, especially in thicker materials. By keeping hydrogen levels low, the 7018 rod minimizes the risk of hydrogen-induced cold cracking, ensuring the structural integrity of your welds.
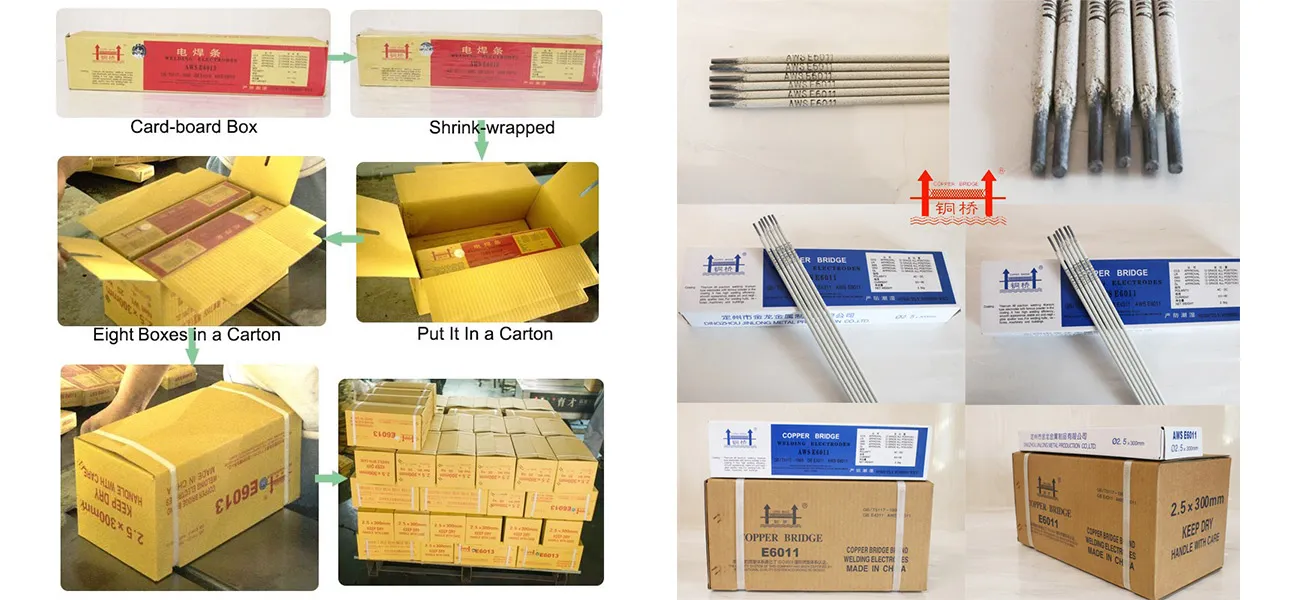
For optimal performance, maintaining the correct storage conditions for 7018 rods is crucial. These electrodes are highly susceptible to moisture absorption due to their low-hydrogen coating. Once they absorb moisture, the rods can compromise the quality of the welds by introducing hydrogen. To prevent this, store the rods in an electrode oven or container at the manufacturer's recommended temperature—typically around 250°F to 300°F—until they are ready for use.
When preparing to weld with a 7018 rod, one must achieve a proper setup for the welding equipment. Most often, the rod is used with a DC (Direct Current) power source, set to electrode positive (DCEP) to optimize penetration and arc stability. It’s also essential to select the right amperage based on the diameter of the rod and the material thickness; a 1/8 inch 7018 rod, for instance, generally requires an amperage range between 90 and 150 amps.
how to use 7018 welding rod
As with any welding operation, surface preparation cannot be understated. Ensure the metal surface is clean and free from rust, dust, grease, and other contaminants. This preparation is pivotal for achieving a solid fusion between the electrode and the base metal.
During the welding process itself, maintaining the correct technique is paramount. The 7018 rod should be held at a slight drag angle, around 10 to 15 degrees from vertical, which promotes a stable arc and prevents slag inclusions. Unlike some other electrodes, a slight weave motion can be used with the 7018 to create a wider bead and ensure a thorough covering of the weld joint.
An often-discussed topic among experienced welders is the rod’s open arc time—essentially, how long the rod can be exposed to the air before it begins to absorb moisture. Though opinions vary, most experts agree that a strict two-hour exposure limit should be adhered to before re-baking the rods to remove any moisture. This step is particularly crucial if you are working in humid environments or with thicker welds that could magnify the impact of hydrogen absorption.
In conclusion,
mastering the use of the 7018 welding rod requires both knowledge and practice. By understanding its properties, storage needs, and welding techniques, you position yourself to achieve impeccable weld quality—characterized by strength, durability, and a clean finish. These outcomes are not just beneficial from a technical standpoint but also reinforce the trustworthiness and expertise fundamental to sustained excellence in welding practices. Always emphasize safety, adequate training, and a commitment to ongoing learning as you engage with this essential welding tool.