Understanding the amperage requirements for a 3/32-inch welding rod is essential for achieving optimal weld quality and performance. This article delves into the specifics of using a 3/32-inch welding rod, providing insights from professional welders and industry experts.
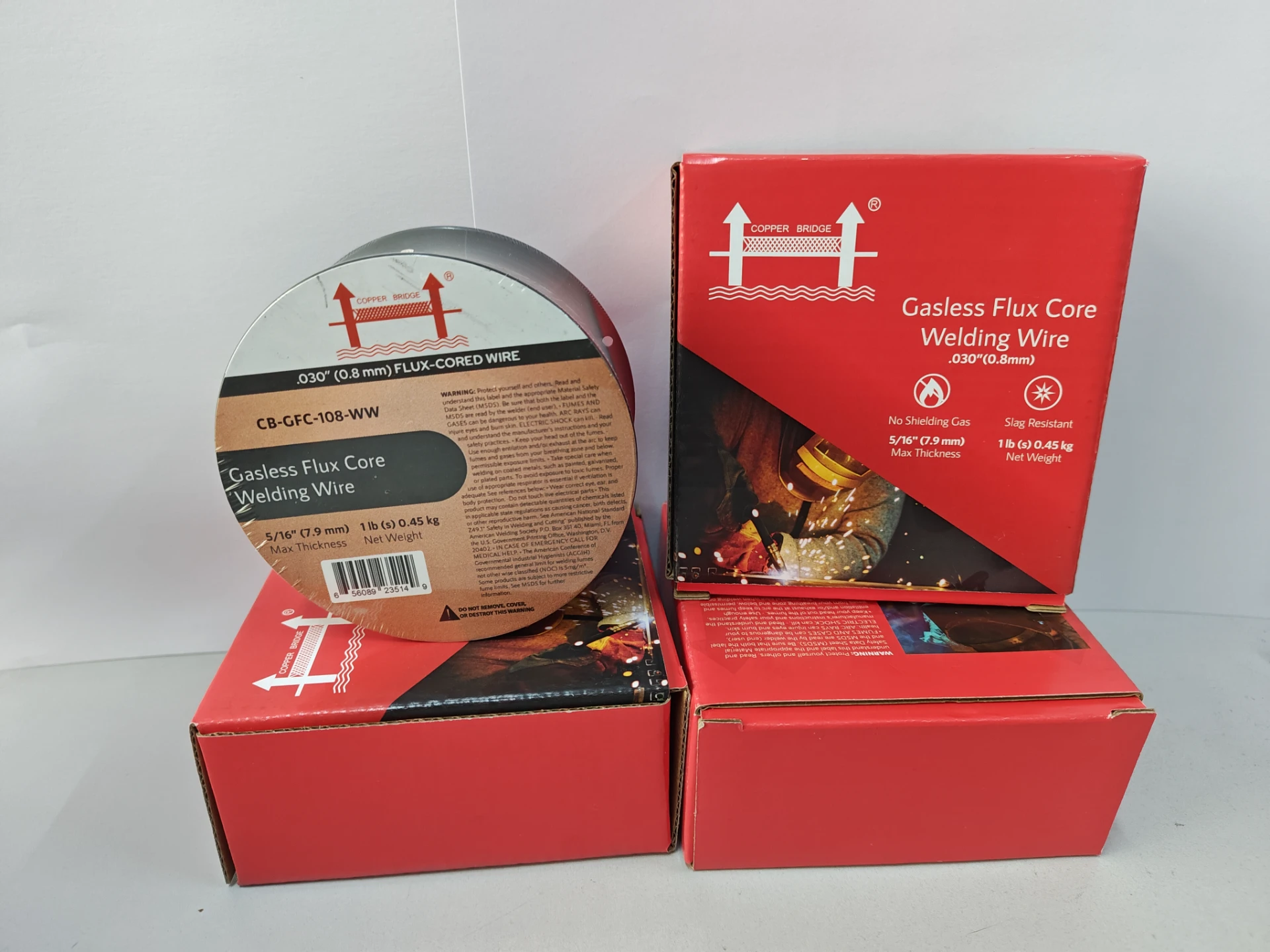
A 3/32-inch welding rod is commonly used in Shielded Metal Arc Welding (SMAW) due to its versatility and ease of use. These electrodes are ideal for various metals and thicknesses, making them a staple in both industrial and hobbyist applications. To maximize their potential, selecting the correct amperage is crucial.
The amperage range for a 3/32-inch welding rod typically falls between 40 to 90 amps. However, this range isn't set in stone; slight variations occur based on the rod type, material thickness, and intended weld characteristics. Let us explore these factors in detail.
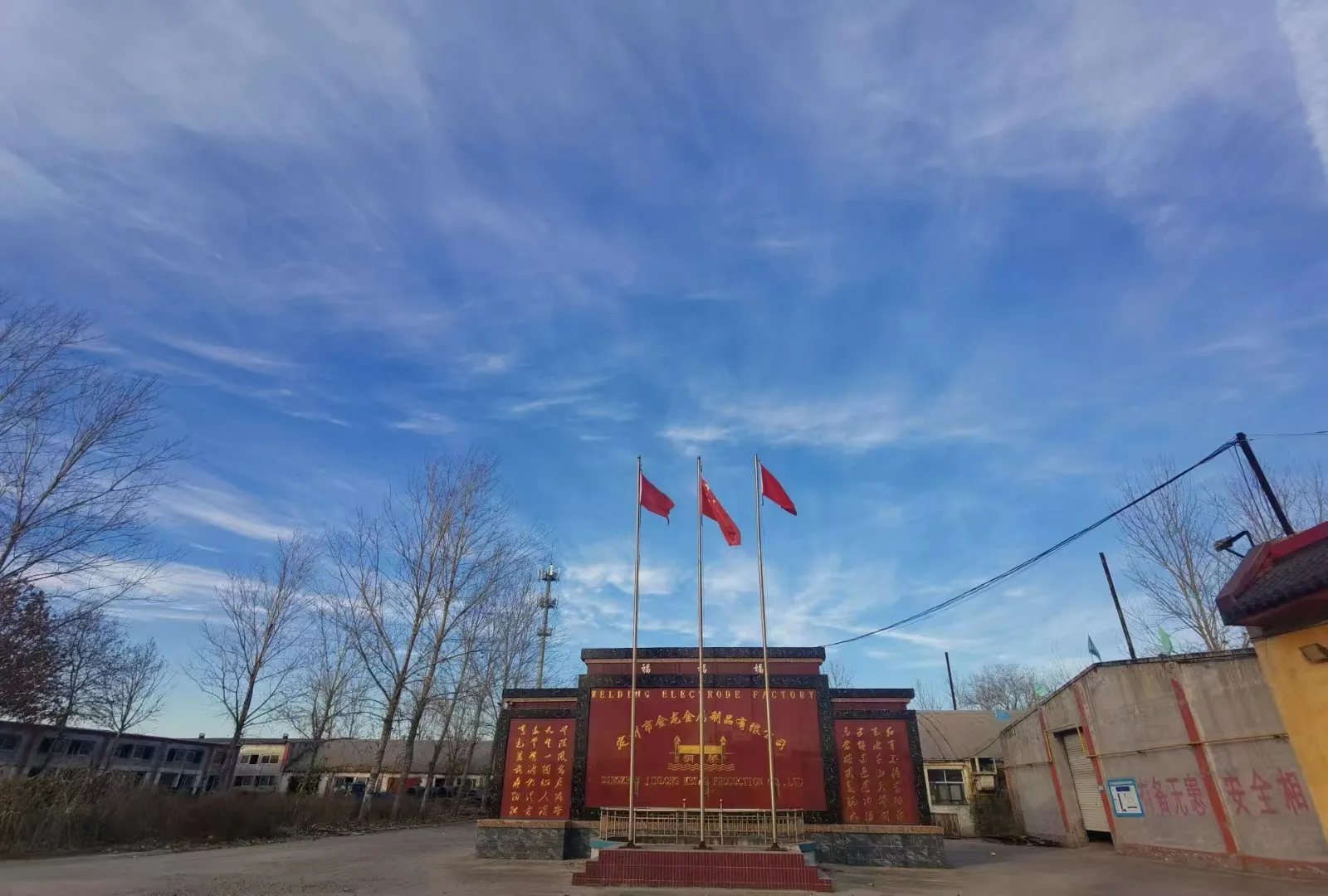
First and foremost, it's essential to consider the type of welding rod being used. A popular choice is the E7018 rod, known for its excellent arc stability and strong welds. These electrodes usually require an amperage setting between 70 to 90 amps. Meanwhile, the E6013 rod, favored for its easy slag removal and smooth bead appearance, operates efficiently between 40 to 80 amps. It's vital to refer to the manufacturer's guidelines or a welding chart to determine the exact specifications for the electrode in use.
Metal thickness is another determining factor. Thinner materials require lower amperage settings to prevent burn-through, while thicker materials demand higher amperage for adequate penetration. For instance, when welding thin sheet metal, it's wise to start at the lower end of the recommended amperage range, around 40 to 50 amps. Conversely, thicker plates can tolerate higher settings near the upper limit of 80 to 90 amps.
Welding technique also impacts amperage selection. For overhead or vertical welding, lower amperage helps maintain control and minimize spatter, whereas flat or horizontal welding may benefit from higher amperage for faster travel speeds.
how many amps for 3/32 welding rod
Your welding machine's capabilities are another consideration. Ensure that your machine can handle the chosen amperage range consistently without overheating. It's beneficial to invest in a welding machine that offers adjustable amperage settings to accommodate different welding needs.
Besides technical parameters, factors such as environmental conditions can also influence amperage choice. Colder temperatures can cause the base metal to require a slightly higher amperage for proper heat input. Similarly, working in a draughty environment might necessitate adjustments to maintain arc stability.
From professional experience, trial and error often play a role in honing the ideal amperage settings. Seasoned welders emphasize the importance of practicing on scrap material to dial in settings before committing to the final project. This ensures that the welds are clean, strong, and visually appealing.
Additionally, utilizing advanced welding techniques and tools can enhance the weld quality. Techniques like backstepping or employing different electrode angles can achieve better results, often leading to adjustments in amperage settings as one gains proficiency.
For those seeking authoritative advice, welding certifications and courses offer invaluable insights into the complexities of welding, including the intricacies of amperage settings. These educational paths furnish welders with the skills to make informed decisions tailored to specific project requirements.
In conclusion, selecting the correct amperage for a 3/32-inch welding rod involves a nuanced understanding of the electrode type, metal thickness, and welding position. By considering these variables and refining one's technique through experience and education, welders can achieve superior results consistently. Trusting in this balanced approach ensures that any welding task is approached with precision and confidence, upholding both the craftsmanship and reliability associated with professional welding practices.